Product
JP
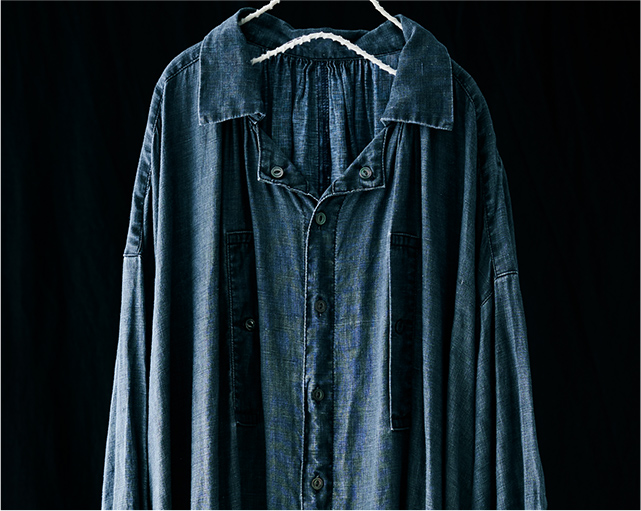
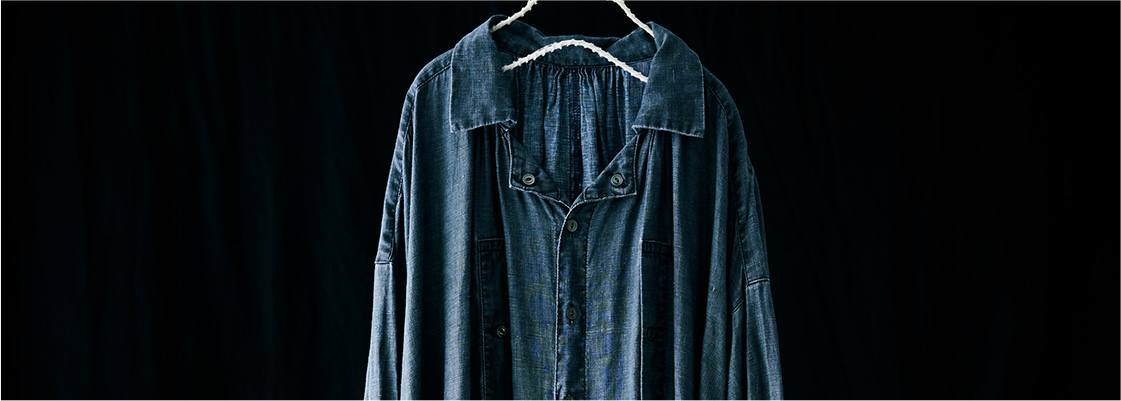
服を作るための紡績、撚糸、染色、製織、
整理加工、縫製などの過程では、
たくさんの選択肢があります。
そのすべてにおいて、
〈ネストローブ/コンフェ クト〉では、
効率を重視するよりも、
素材にストレスをかけず、
その結果として、風合いがよくなり、
着心地がよくなることを選んでいます。
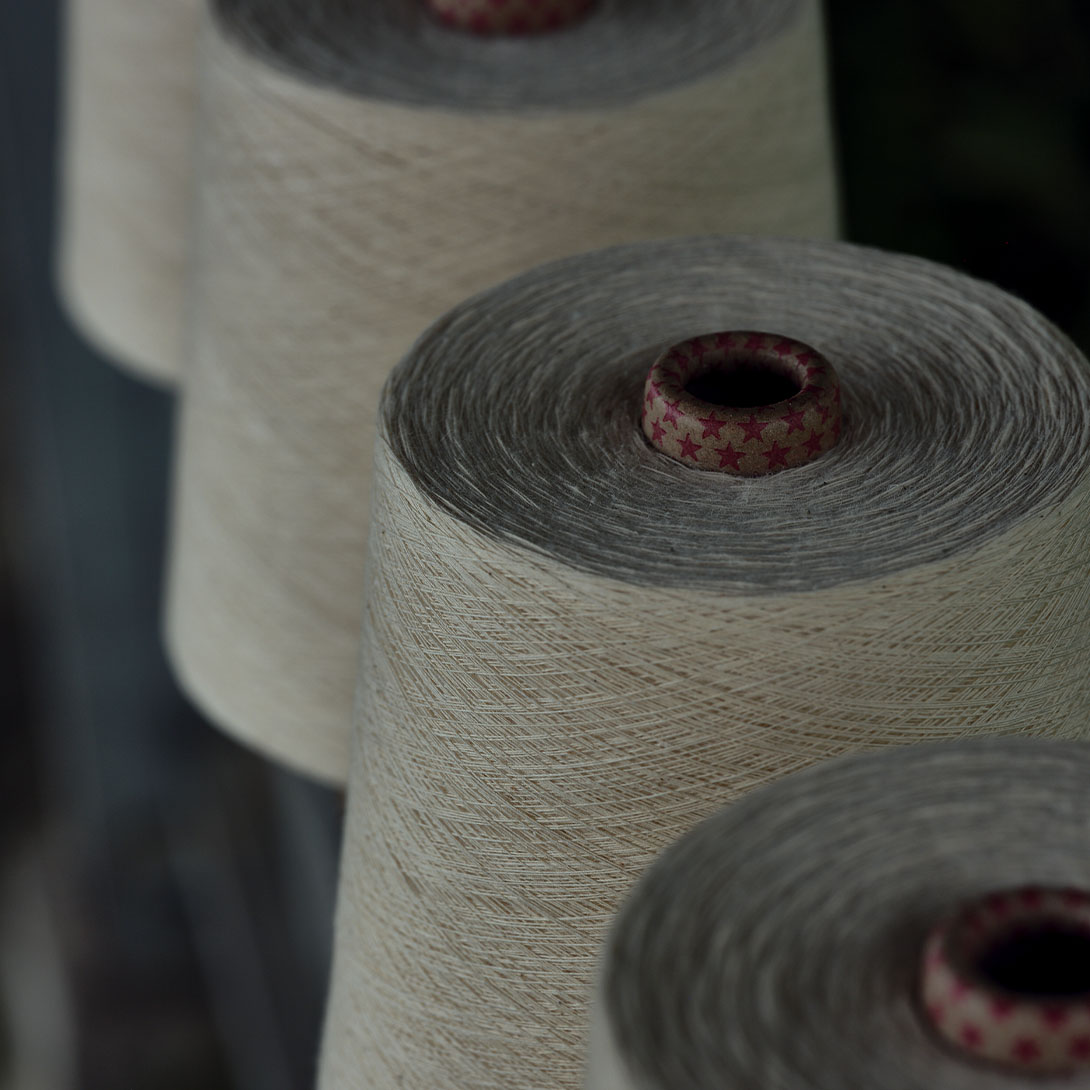
- 紡績・撚糸
-
糸を紡ぎ、撚りをかける
More
コットンの糸は、原綿を混打綿機を使って解きほぐし、原綿に付着している葉かすや種子片、砂塵などのゴミを除去してからシート状に伸ばします。これをカード機で梳って繊維を1本1本分離し、並行に引き揃え、小さいゴミや短い繊維を取り除きます。残った長い繊維を並行状態に揃えて紐状にし、さらに梳って繊維を整えていきます。次に練条機で引き延ばしながら繊維をまっすぐにし、太さのムラをなくしてから、粗紡機でさらに引き延ばしながら撚りをかけ、ボビンに巻き取ります。これをさらに引き伸ばして所定の太さにし、撚りをかけたものを円錐状に巻き取り、紡績工程の完了。
ウールの紡毛紡績の場合も工程はほとんど同じです。目指す色を表現するべくブレンドした原料をホッパーという機械に通し、繊維を掻き揃えてシート状に。さらに叩いてフィルム状にしたものを縦方向に細かく分割し、120本 ほどの篠という状態にミュールという機械で撚りをかければ、ウール糸の完成。例えばノイルといわれる紡績中に出た羊毛くずや、不要になった繊維(衣料、糸、布地)などを専用の反毛機械を使って綿状に戻したものなども再利用して紡いでいます。
口に紡績でひいた糸を撚り合わせる撚糸作業が必要です。糸は撚り合わせることで強度が出てしなやかになり、撚りをかける回数や方向を変えることで、その糸で作られる生地の風合いや質感が変わってきます。例えば強く撚りをかけた糸だとシャリ感のある生地になるように、同じ色、同じ番手の糸でも、撚り方が違うだけで色の見え方も変わります。撚糸からこだわることで、生地の加工とはまた別の、繊細なニュアンスを作り出せるのです。
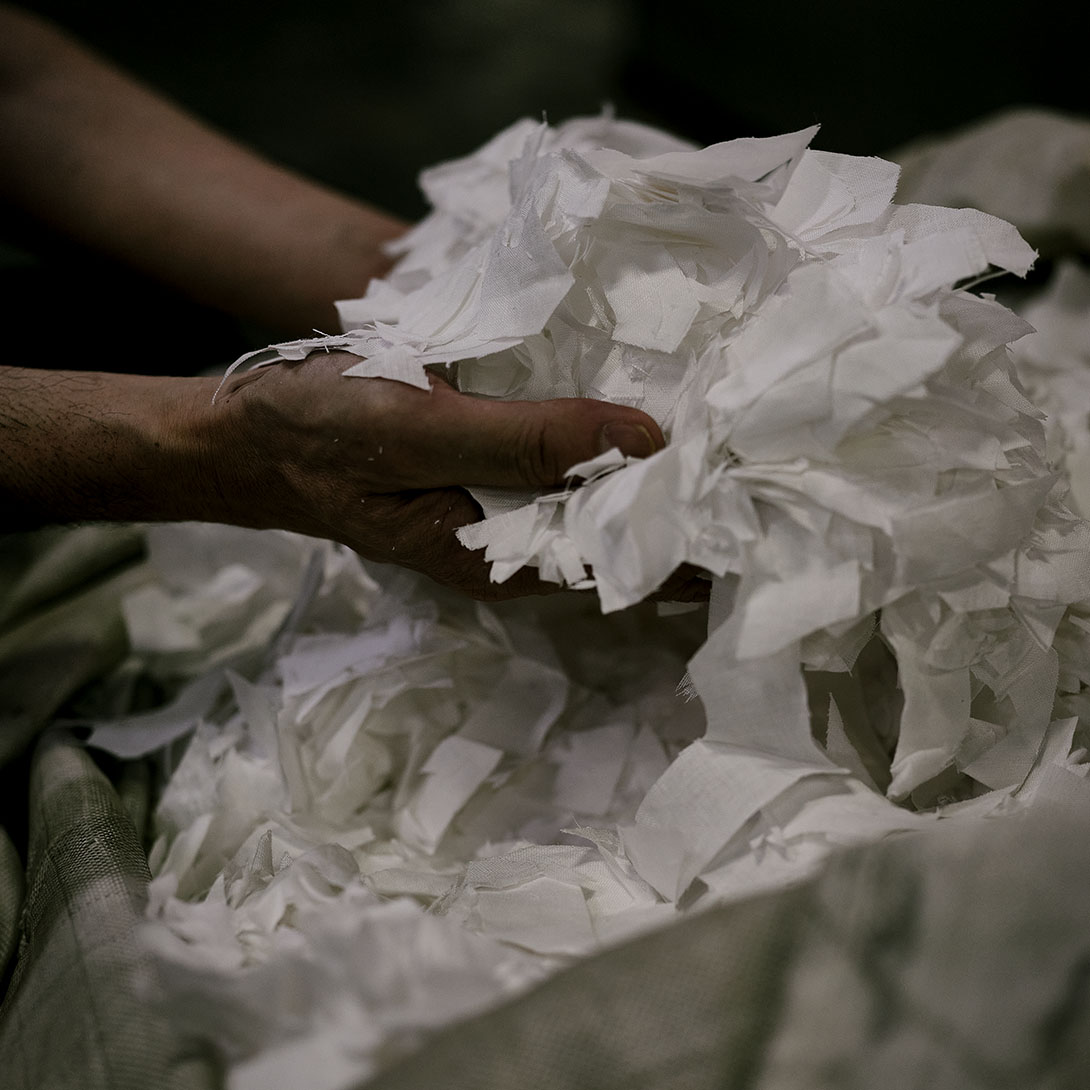
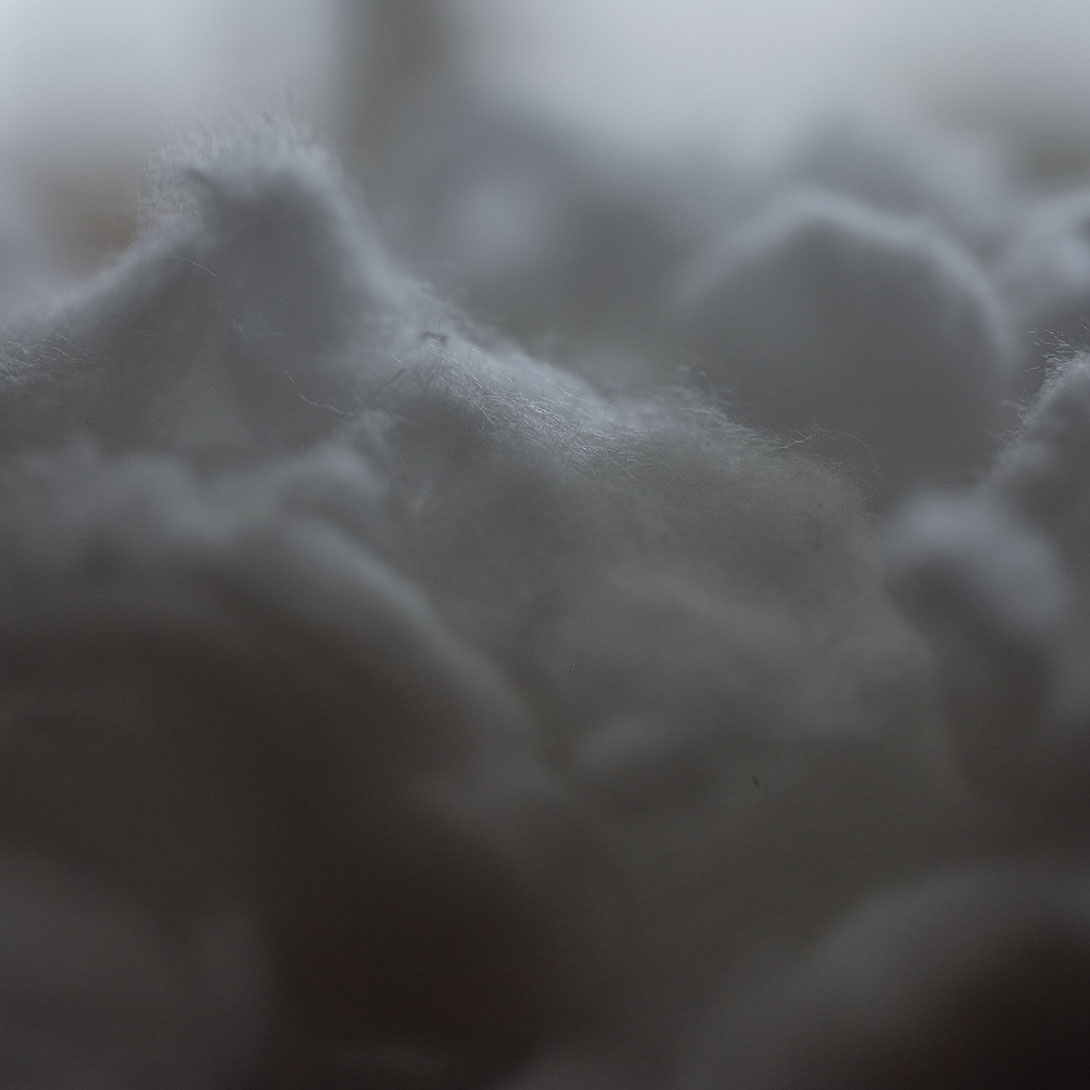
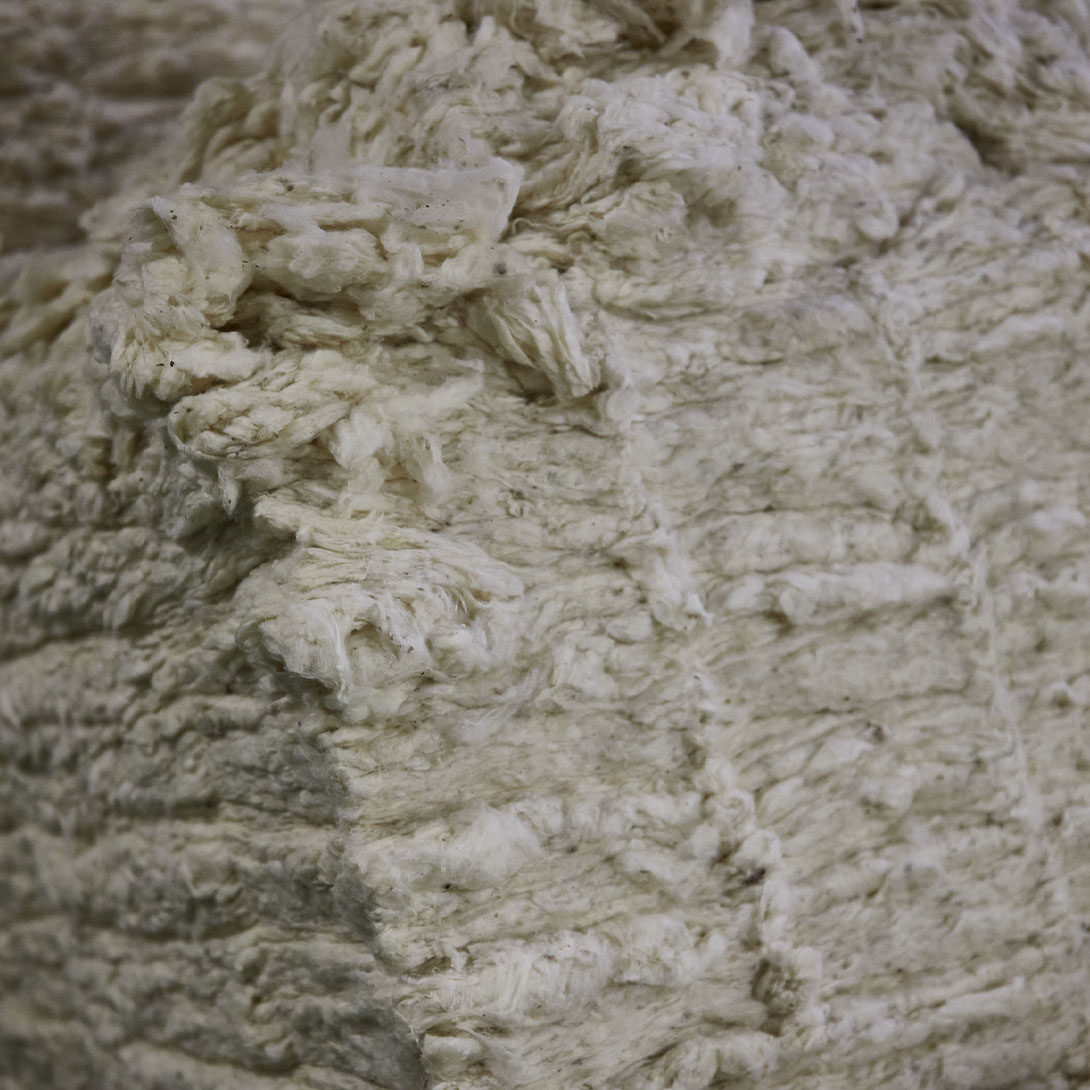
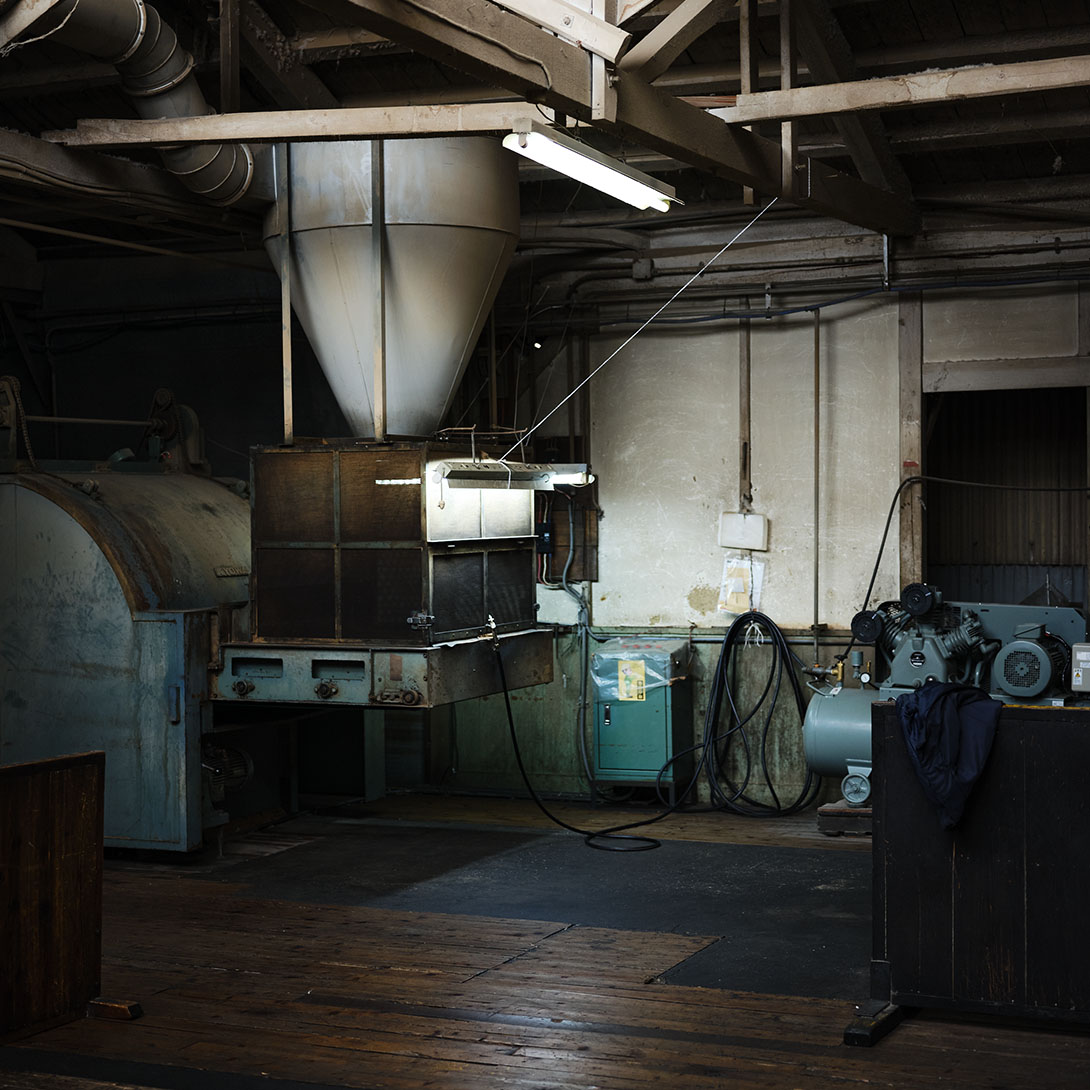
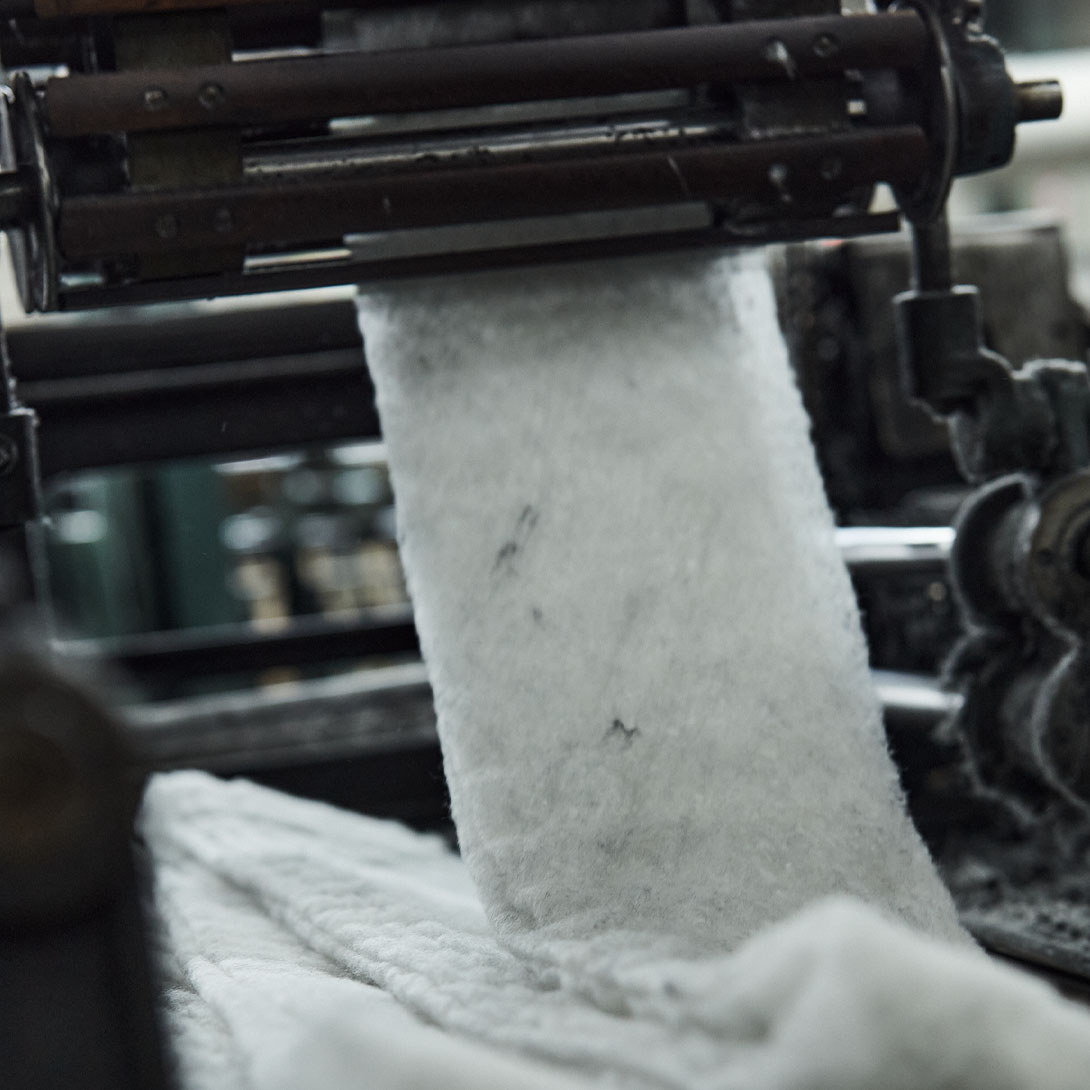
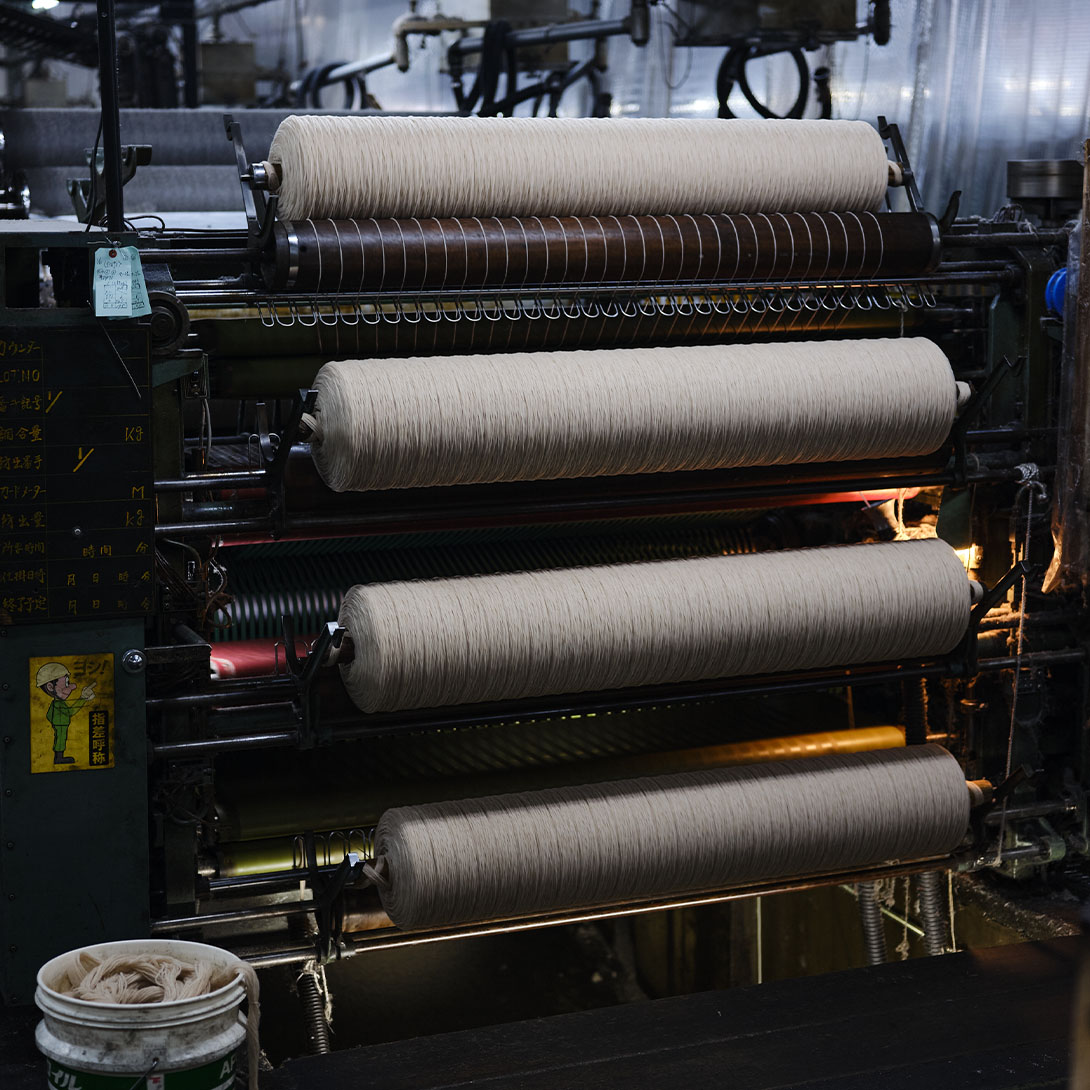
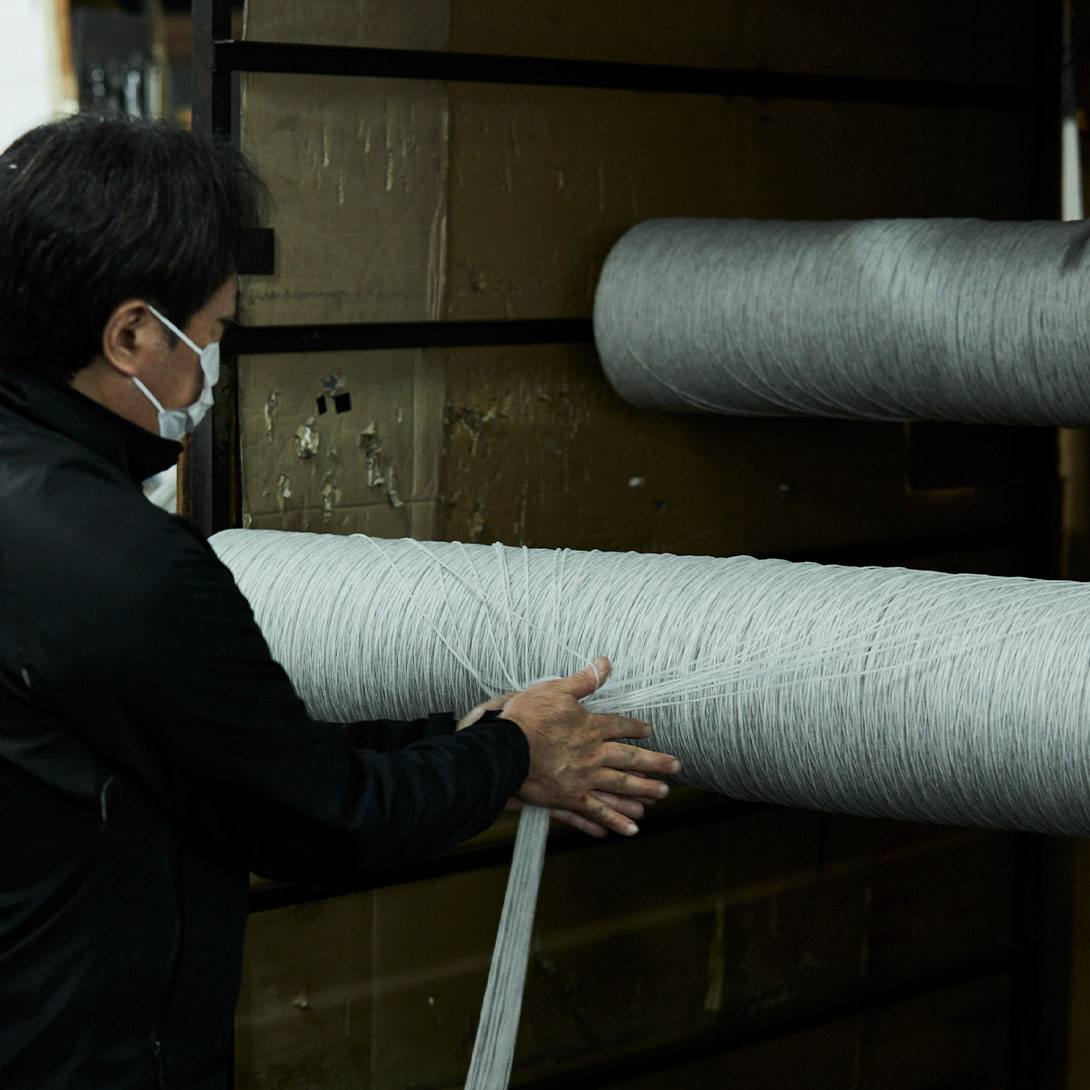
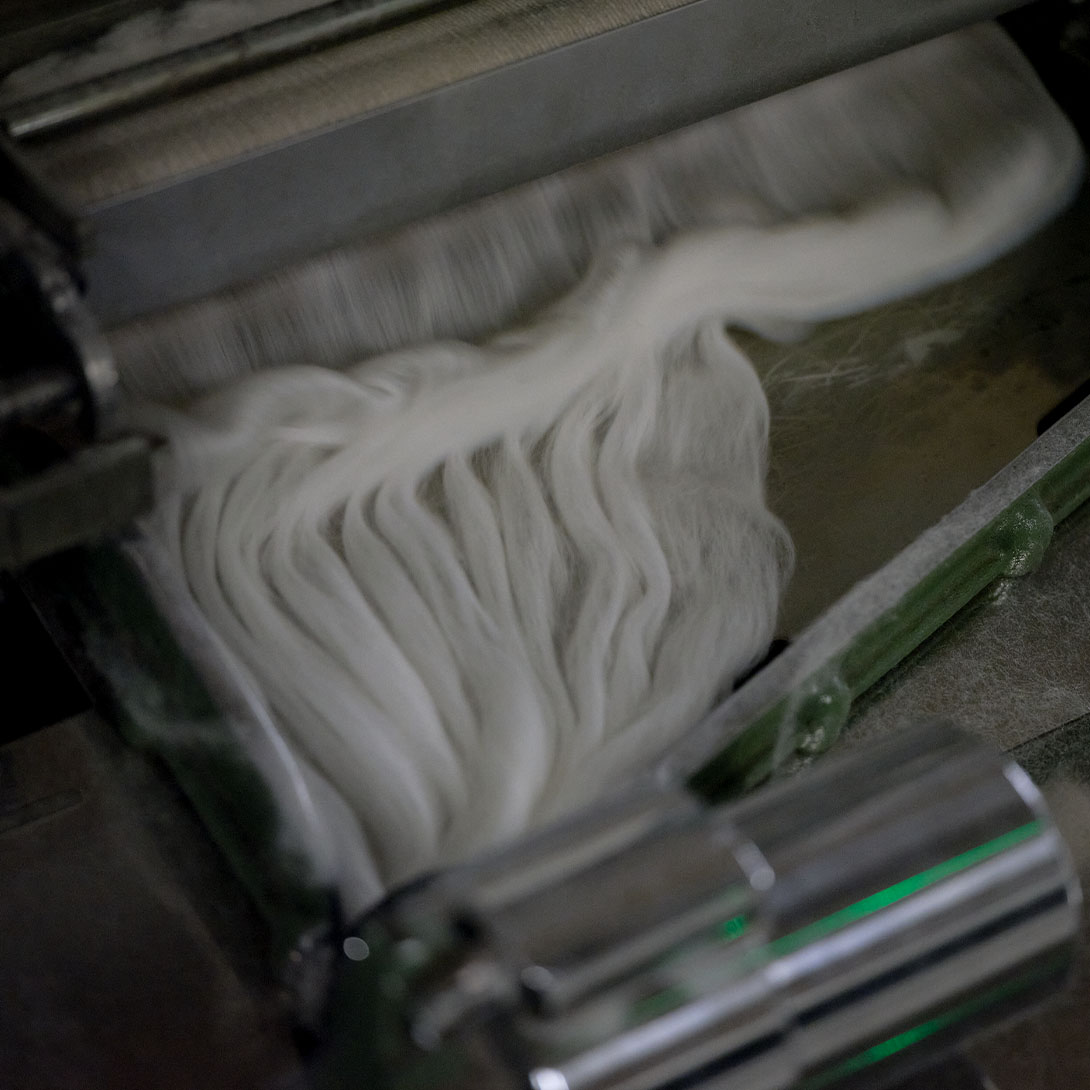
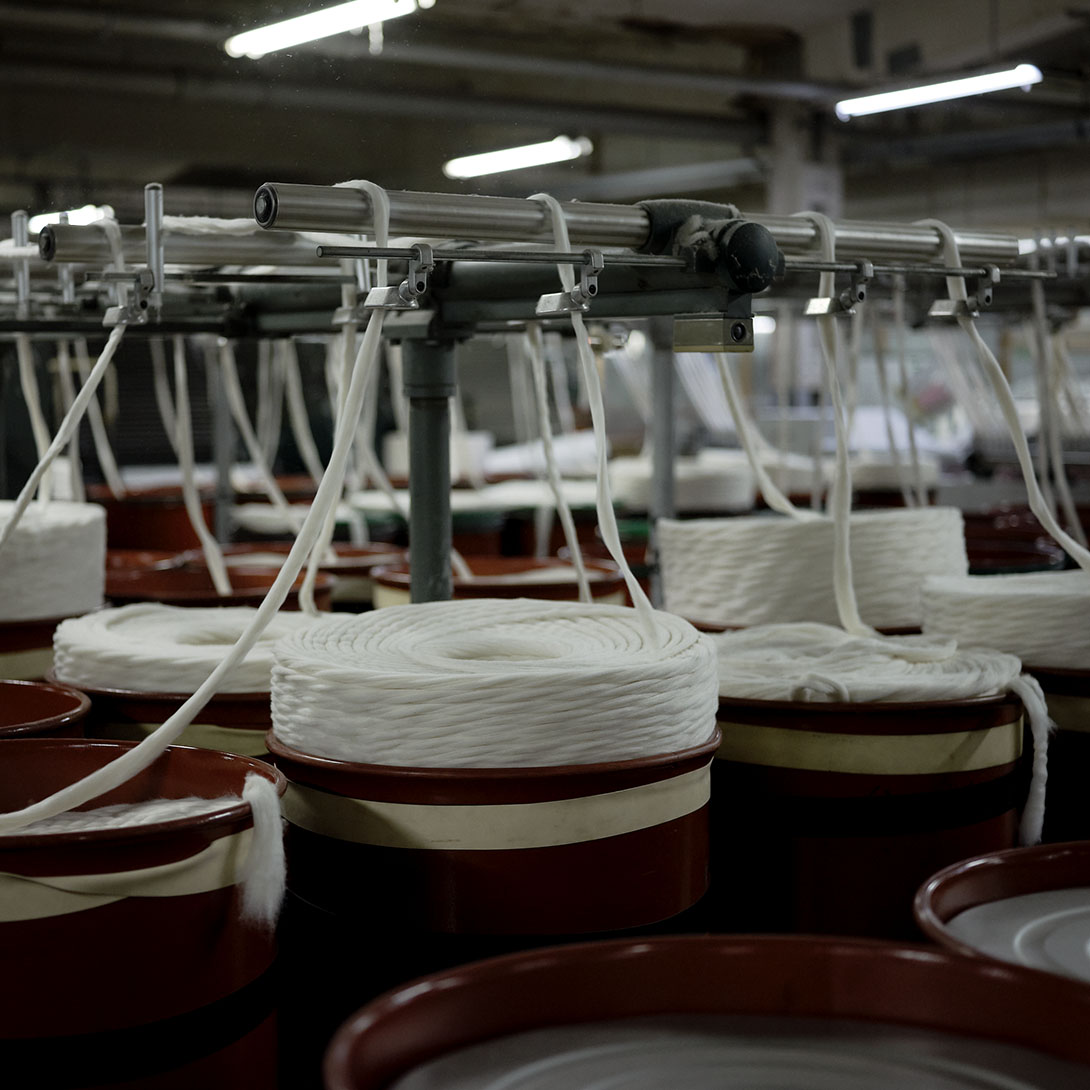
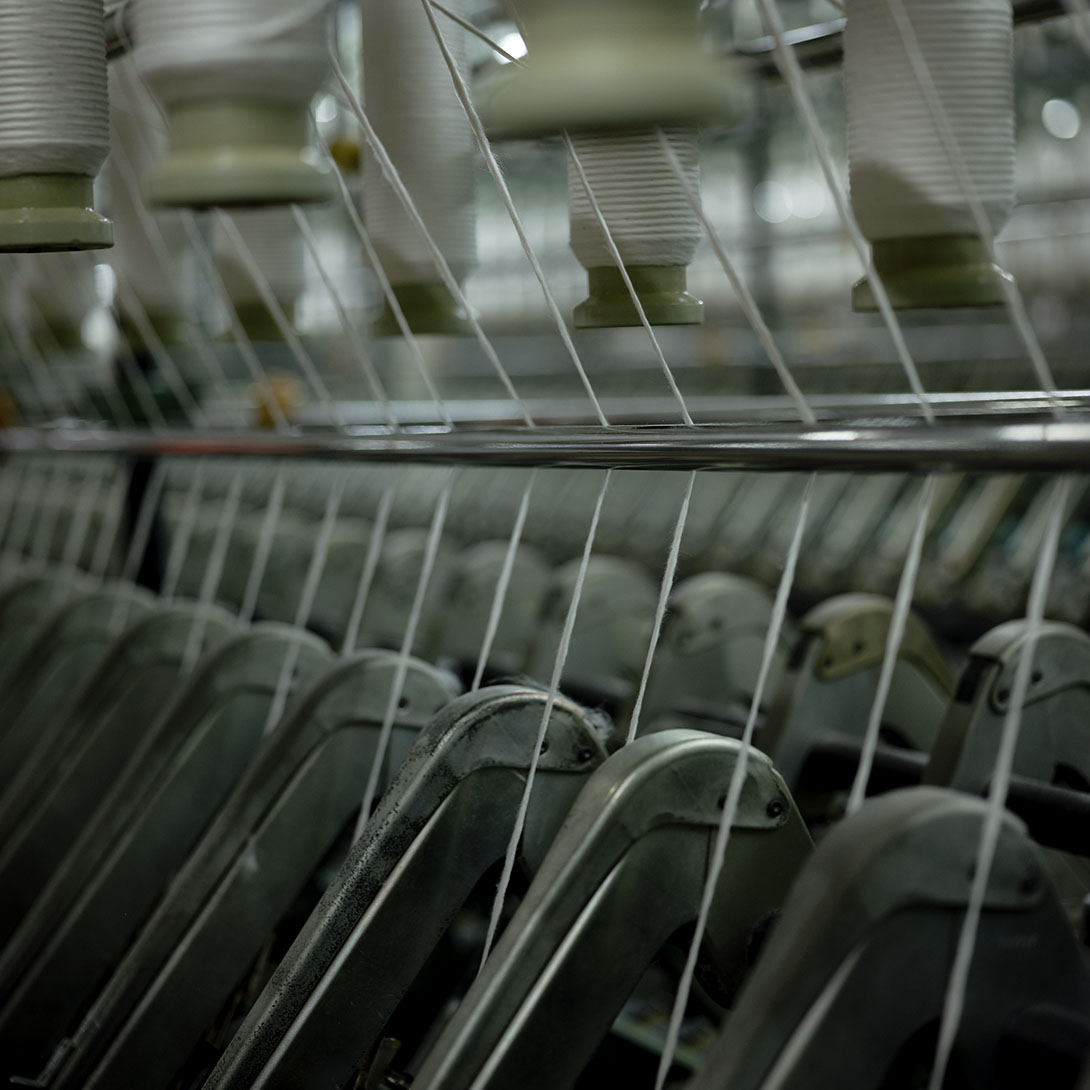
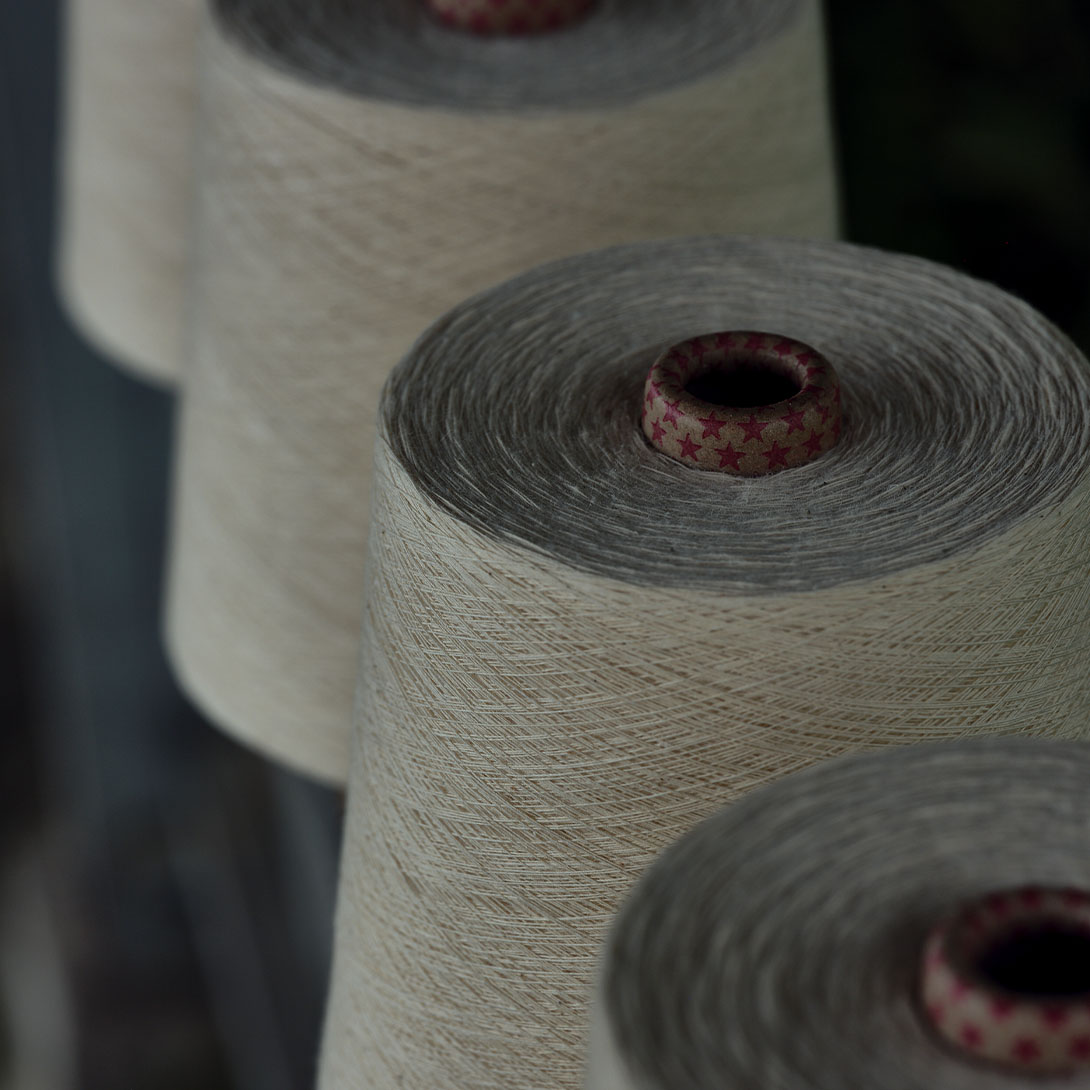
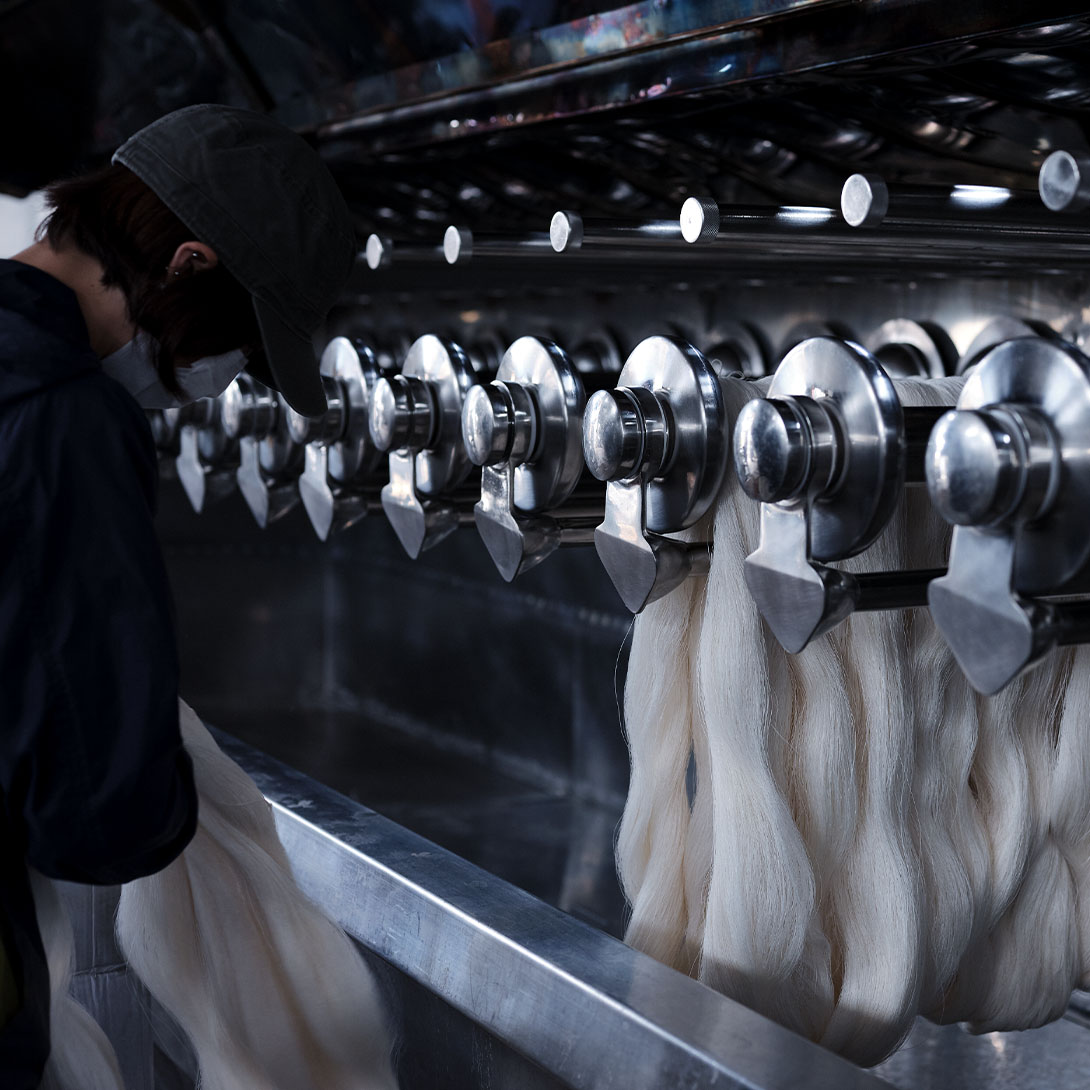
- 染色
-
糸・生地を染める
More
- 糸を染める
- 原糸を染める場合、「チーズ染め」や「かせ染め」という方法があります。チーズという大きな糸巻きを機械にいくつもセットすると内側から染料が出てきて、一気に染めることができるのが「チーズ染め」。対して、糸を束にした状態のかせを棒にかけ、染料をかけていくのが「かせ染め」。もちろん「チーズ染め」のほうが、倍ほど効率がいいのですが、〈ネストローブ/コンフェ クト〉では、糸にストレスを与えない「かせ染め」を選んでいます。6 0〜8 0 度ほどの染料をかけると、本来なら糸は縮みますが、チーズに巻いて伸びきった状態だと、縮みたくても縮めないのです。「かせ染め」ならば、縮みたいときに縮むことができるので、風合いも着心地もよくなるのです。
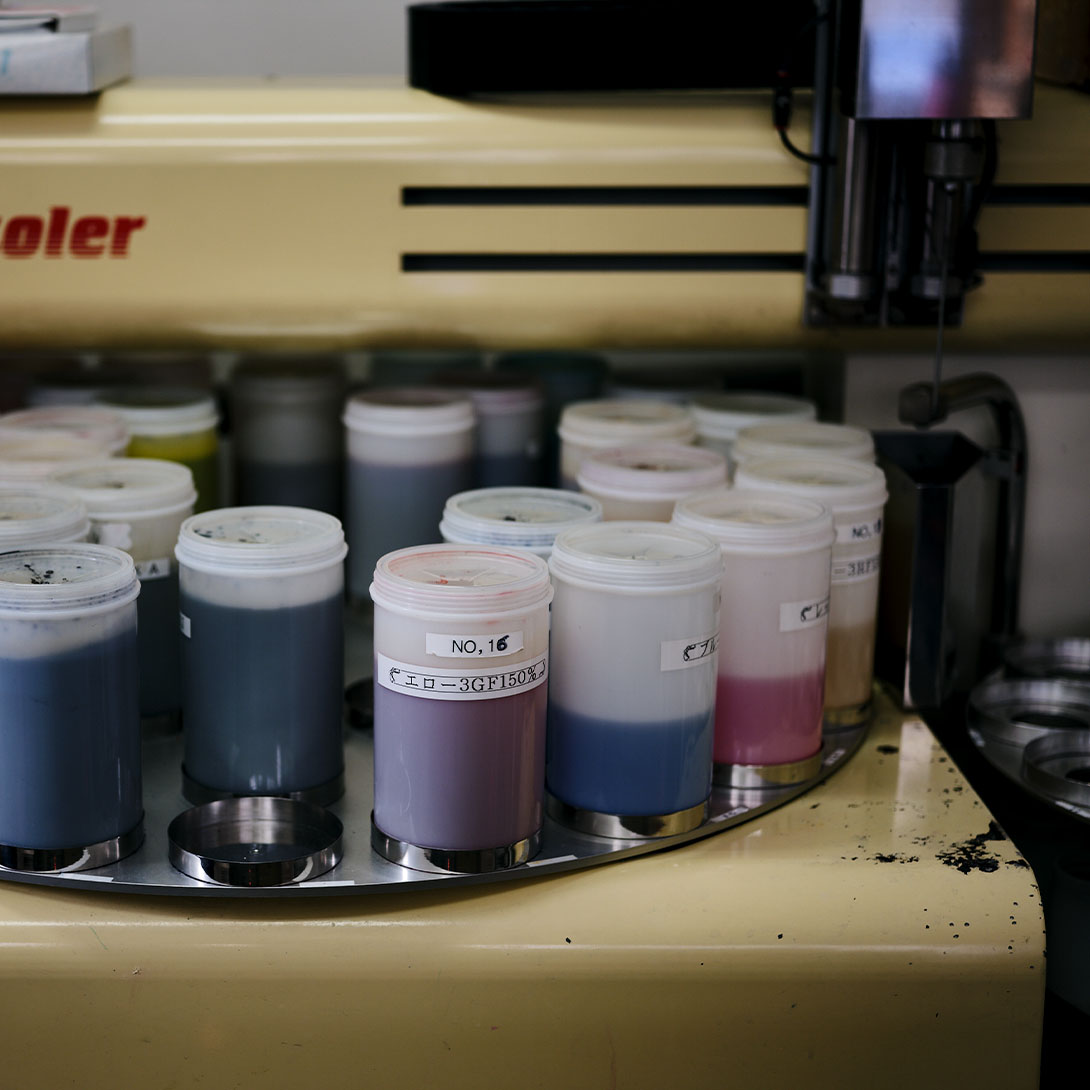
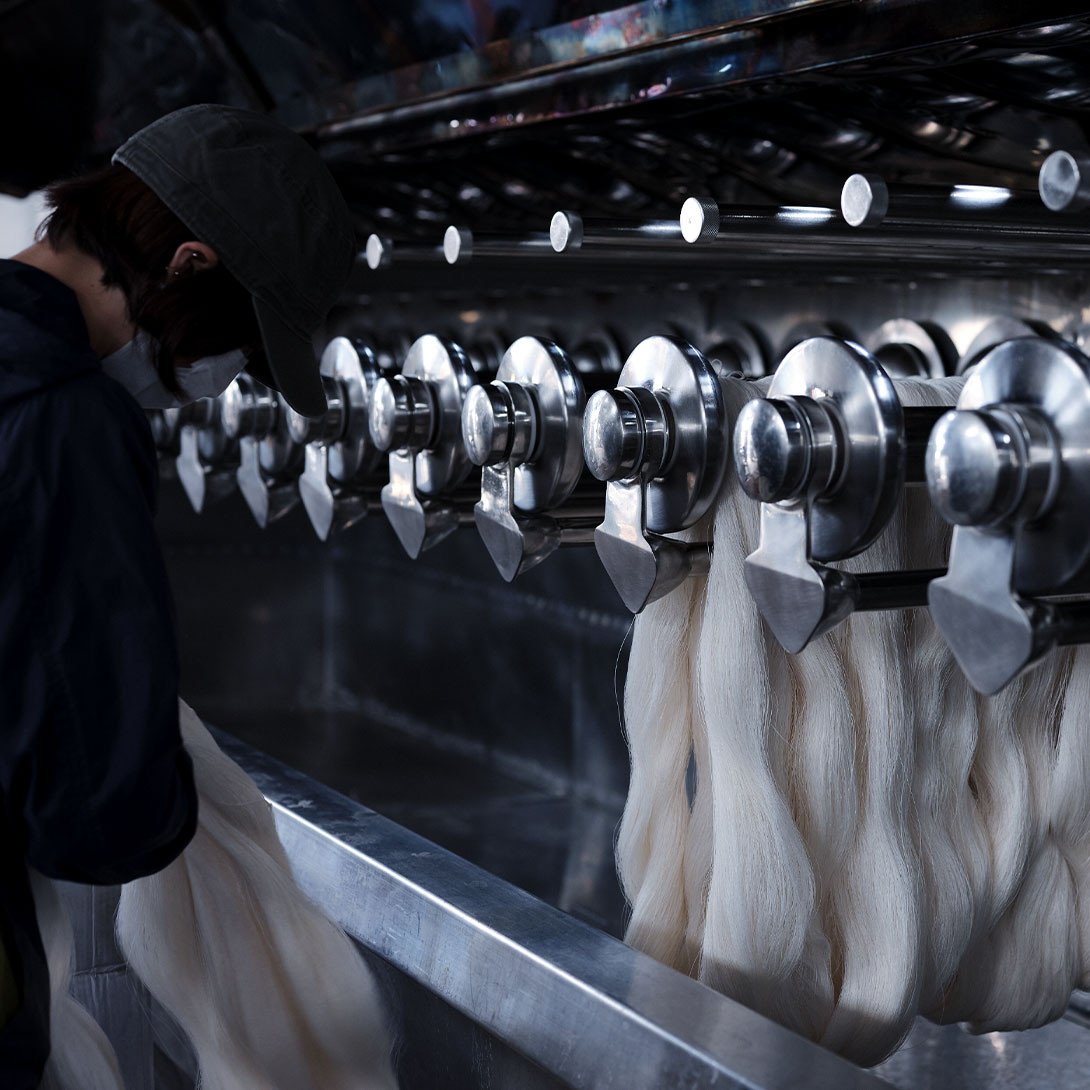
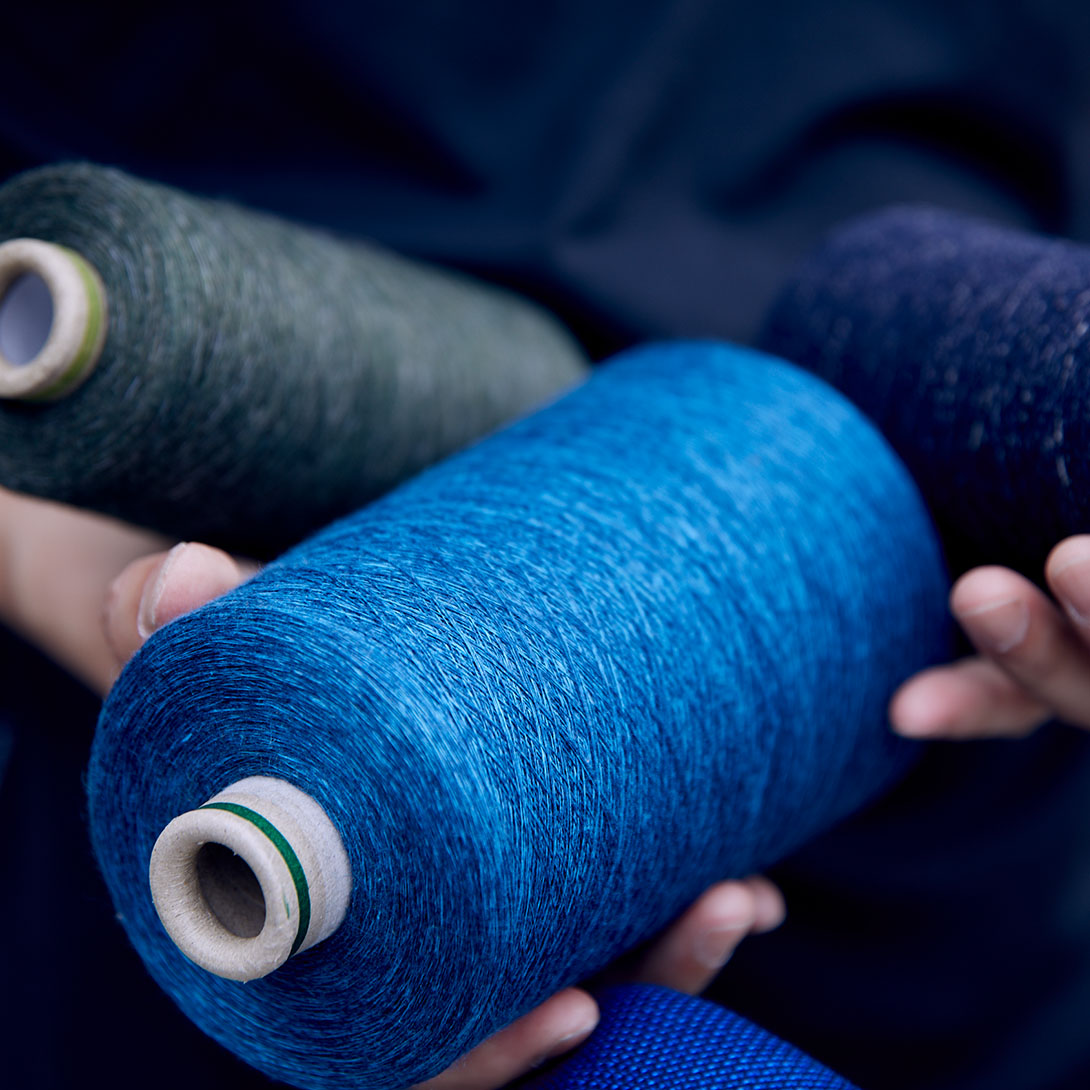
- 生地を染める
- ヴィンテージのような風合いを出すために糸の表面だけを染める「中白染め」「ロープ染色」という手法も定番です。この手法で染めた糸で作った服は、着込んでいくと染まらなかった芯の白がちらちらと見えるようになり、それが風合いとなっていくのです。
また生地を染める場合も、糸からこだわって織っていただいた天然素材の持つ豊かな表情を最大限に活かすべく、釜染めしてから天日干しをしています。「釜」と呼ばれている大きな洗濯機のようなワッシャー機の中に染料と精錬した白生地を入れ、正転と反転を繰り返しながら温度を上げ、染めますが、生地にテンションをかけないので、15 ~ 20% 近く縮みます。機械のなかで回転するうちにくしゃくしゃになるので、多少のムラや染料溜まり、特有のシボも出て、それが風合いになるのです。それを機械的な圧力や張力をかけることなく、天日干しでふっくらと乾燥させています。
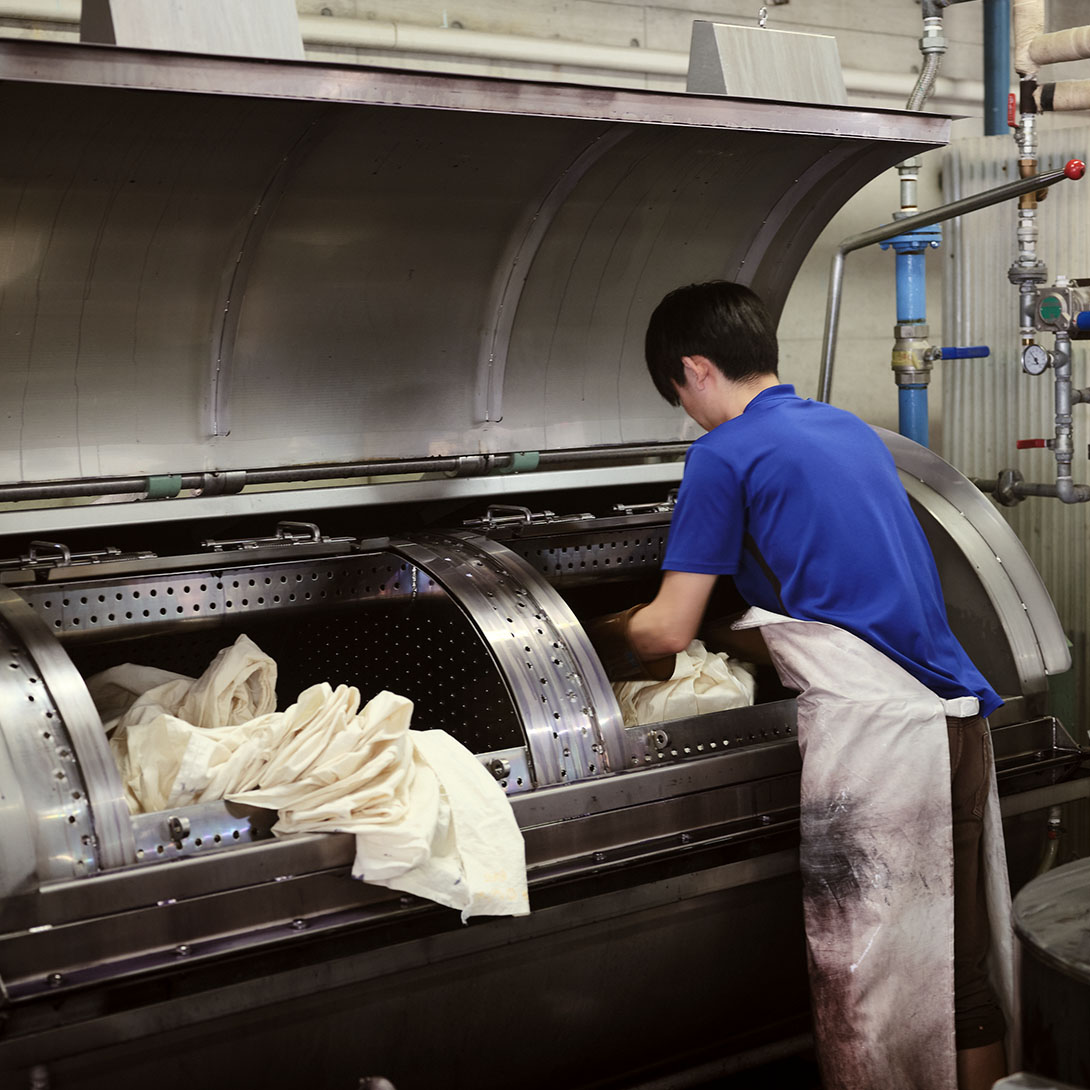
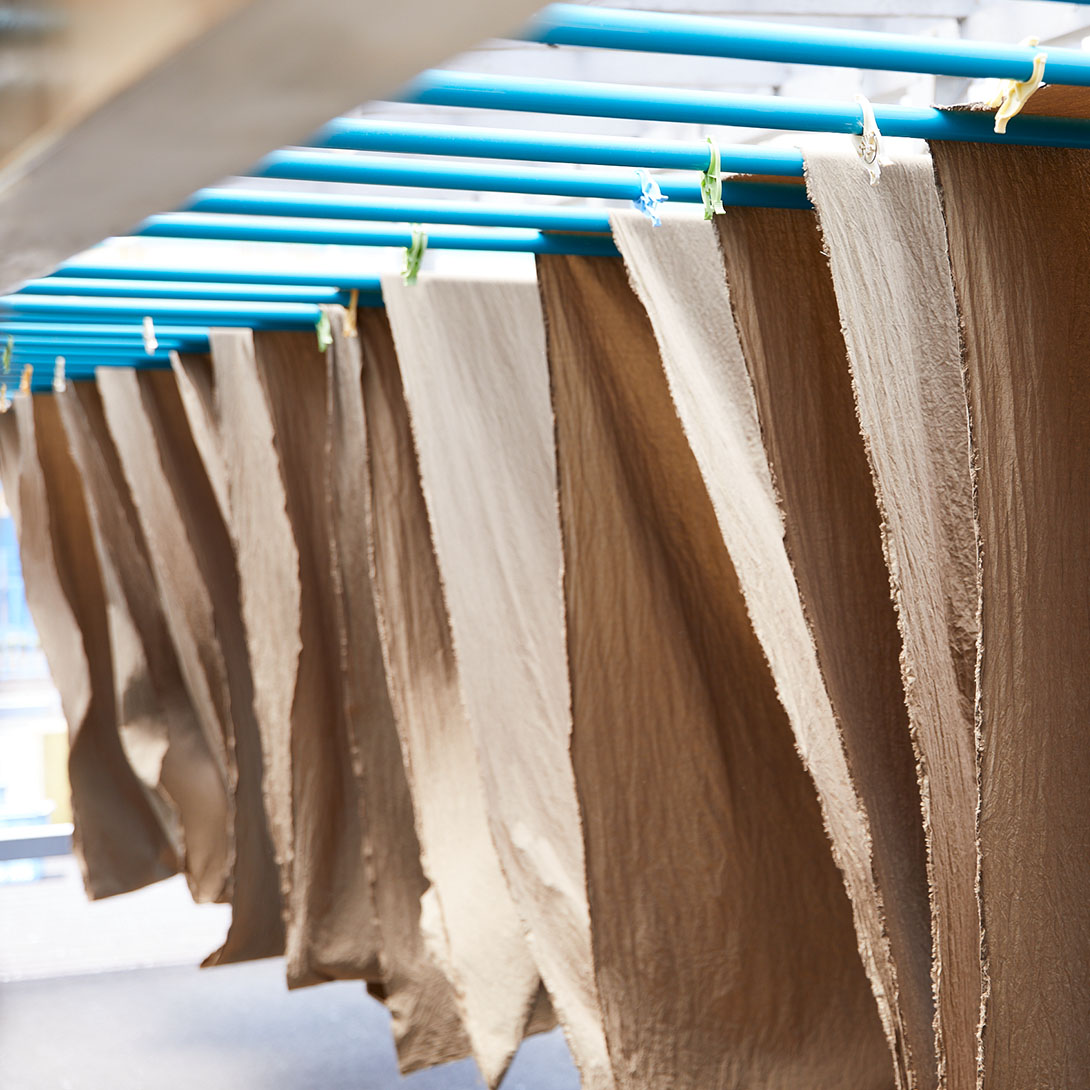
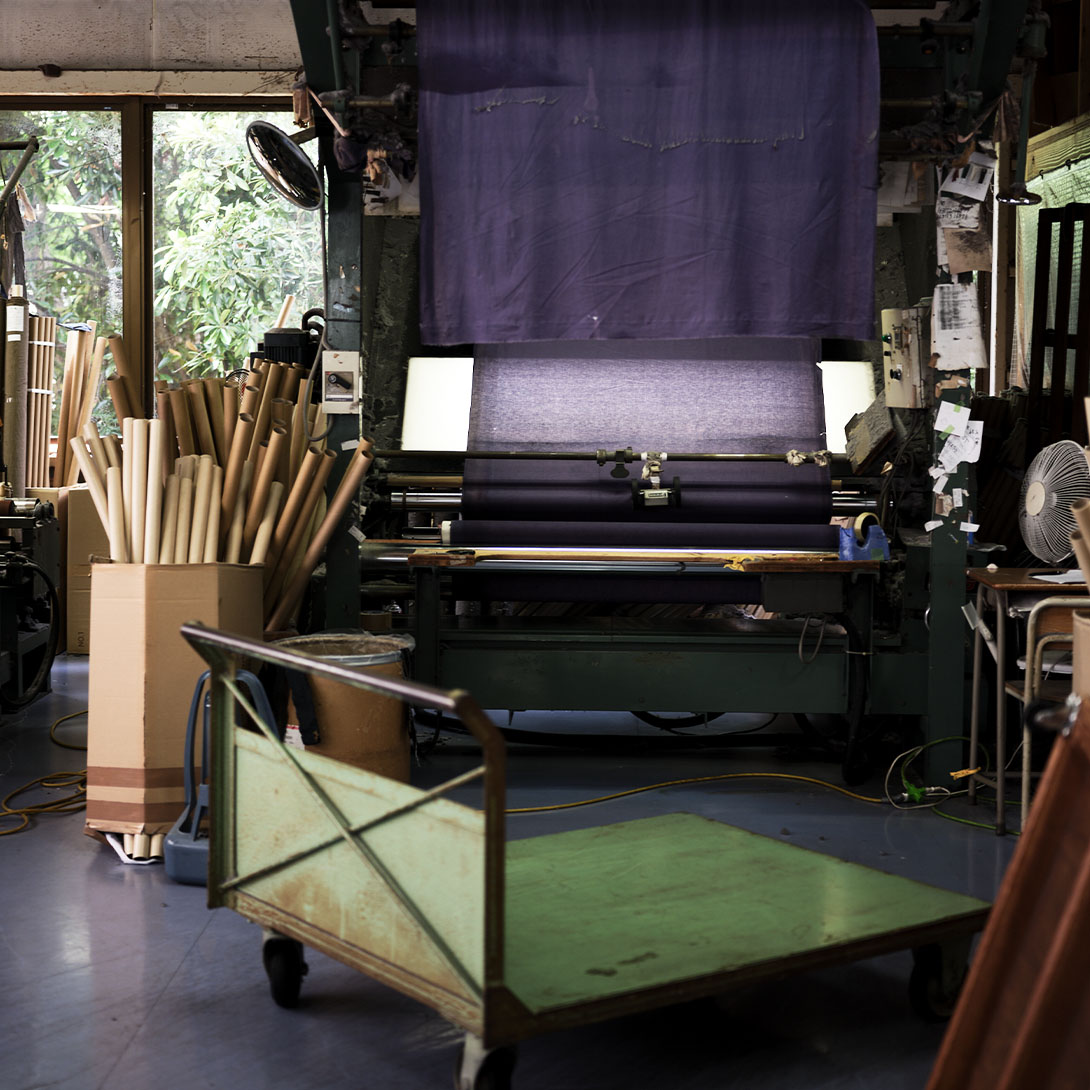
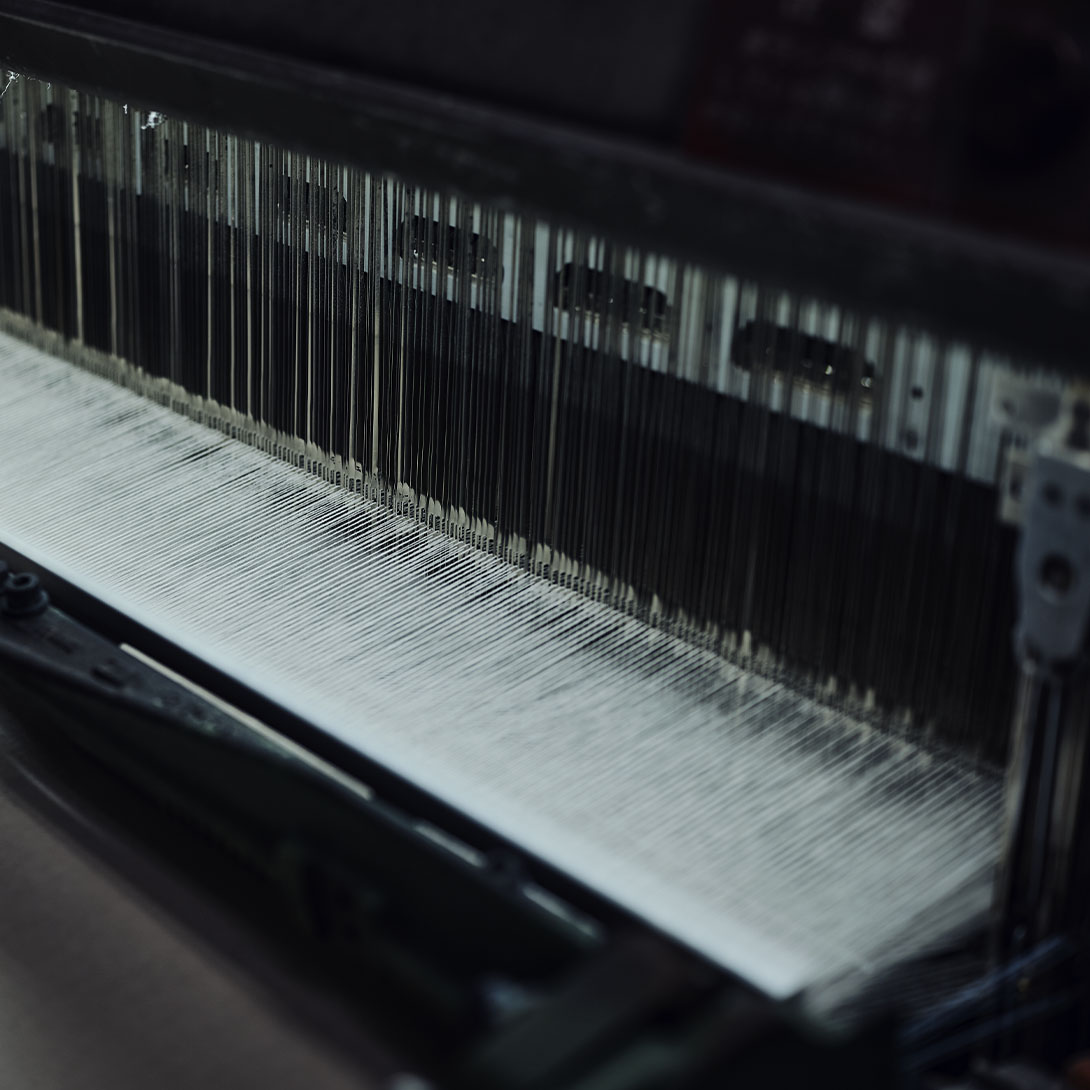
- 製織
-
布帛生地を織る
More
製織工場では、織機に経糸をかけ、経糸の間に緯糸を通していくという作業を行います。
まずは、膨大な数の糸を設計図に基づいて経糸を準備する整経作業。そして、緯糸を入れるための綜絖、筬差しを織機にセットし、張力を調整しながら生地を織り上げます。それぞれの工程で、布の組織や生地のハリ、風合いが決まります。経糸と緯糸を組み合わせるだけでも、無限大のバリエーションができるのです。ただしリネンは摩擦に弱く切れやすいため、それぞれの工場で工夫して織り上げています。
また、昔ながらのシャトル織機も使っています。シャトル織機は低速で、狭い幅の生地しか織れませんが、経糸にも緯糸にも負担をかけないので、表面に凹凸感のあるふっくらと高密度な生地が織れるのです。風合いは加工仕上げで調整できる部分もありますが、シャトル織機で織り上げた生地で作った服は、着込んでいったときの体に馴染む感じや、経年変化の表情が特に魅力です。
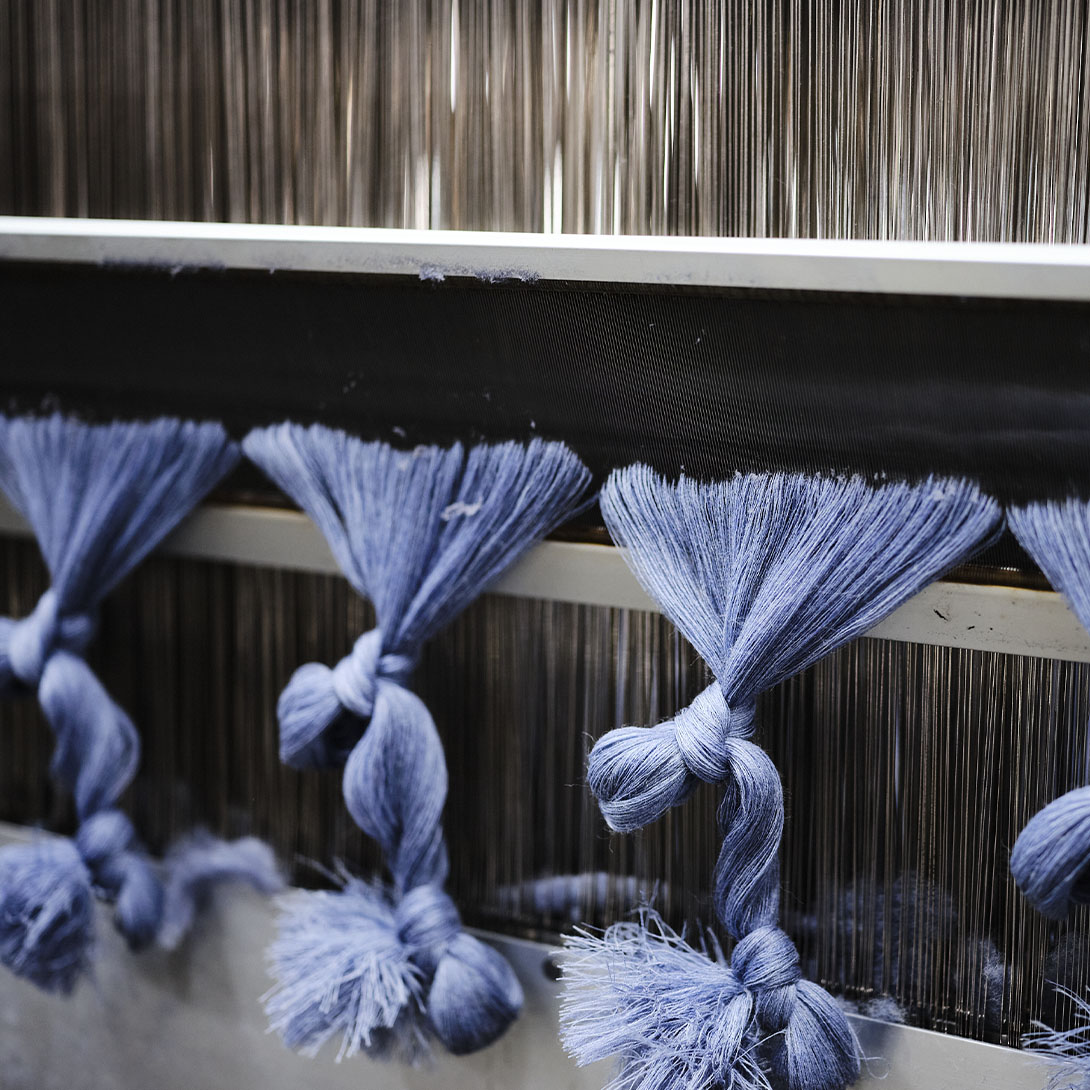
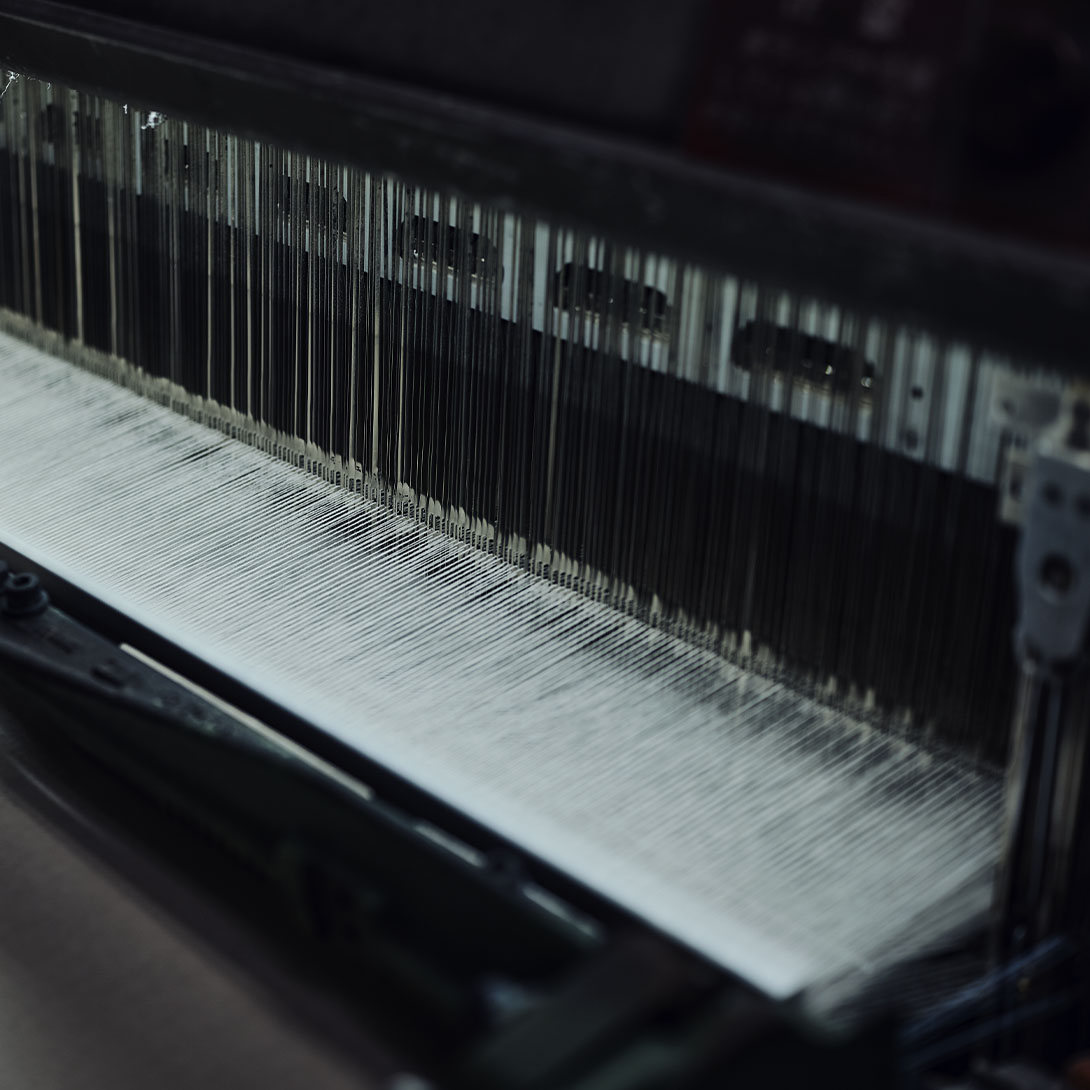
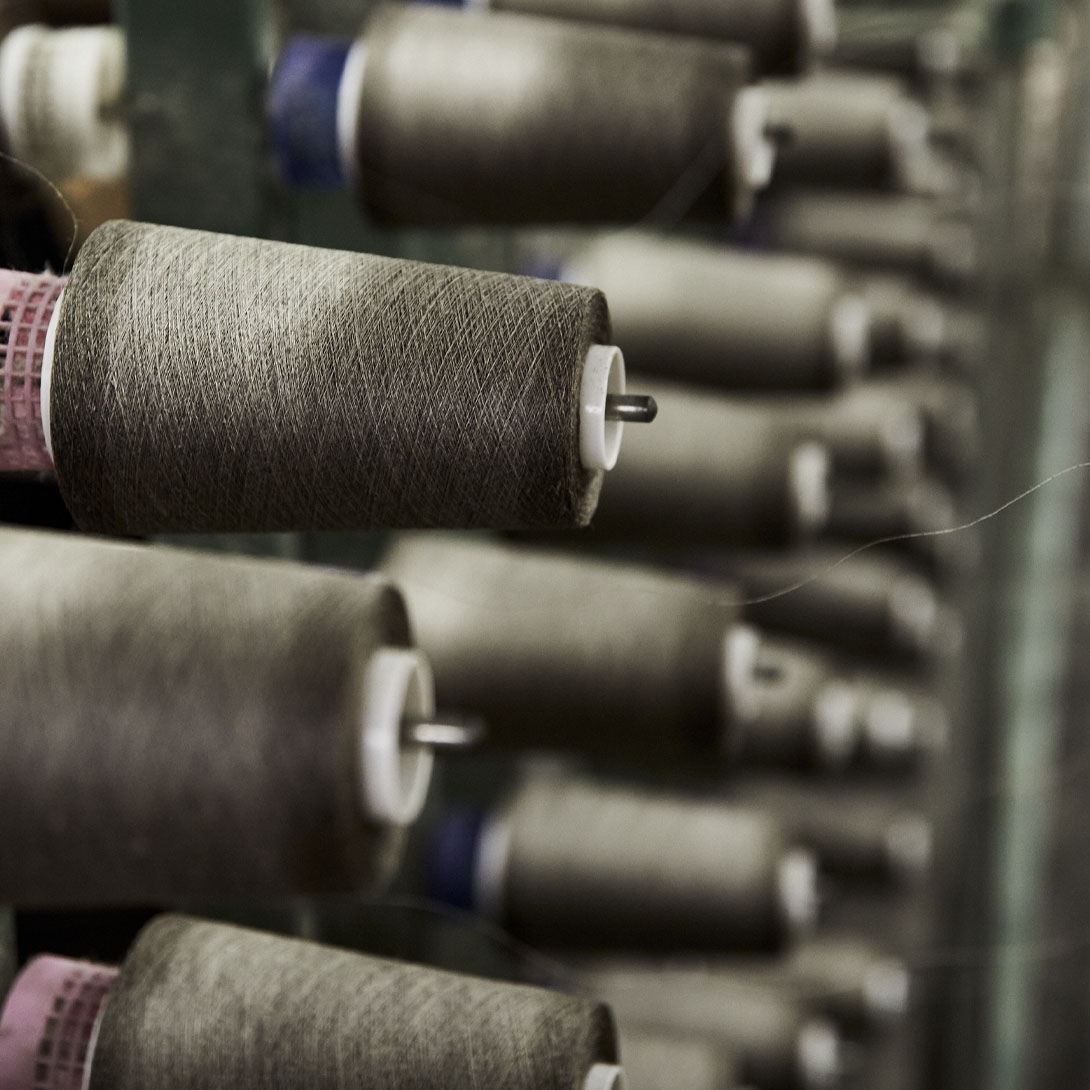
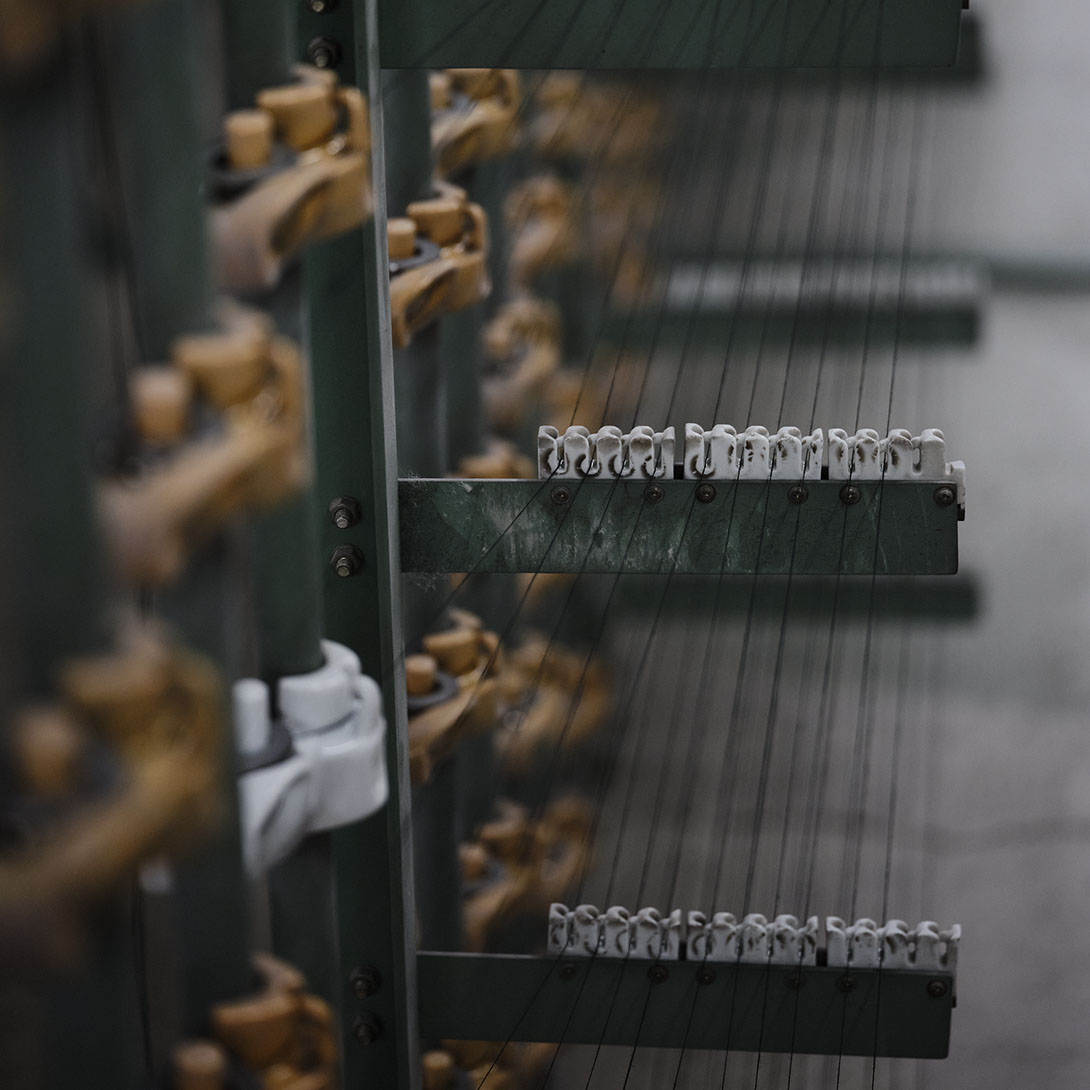
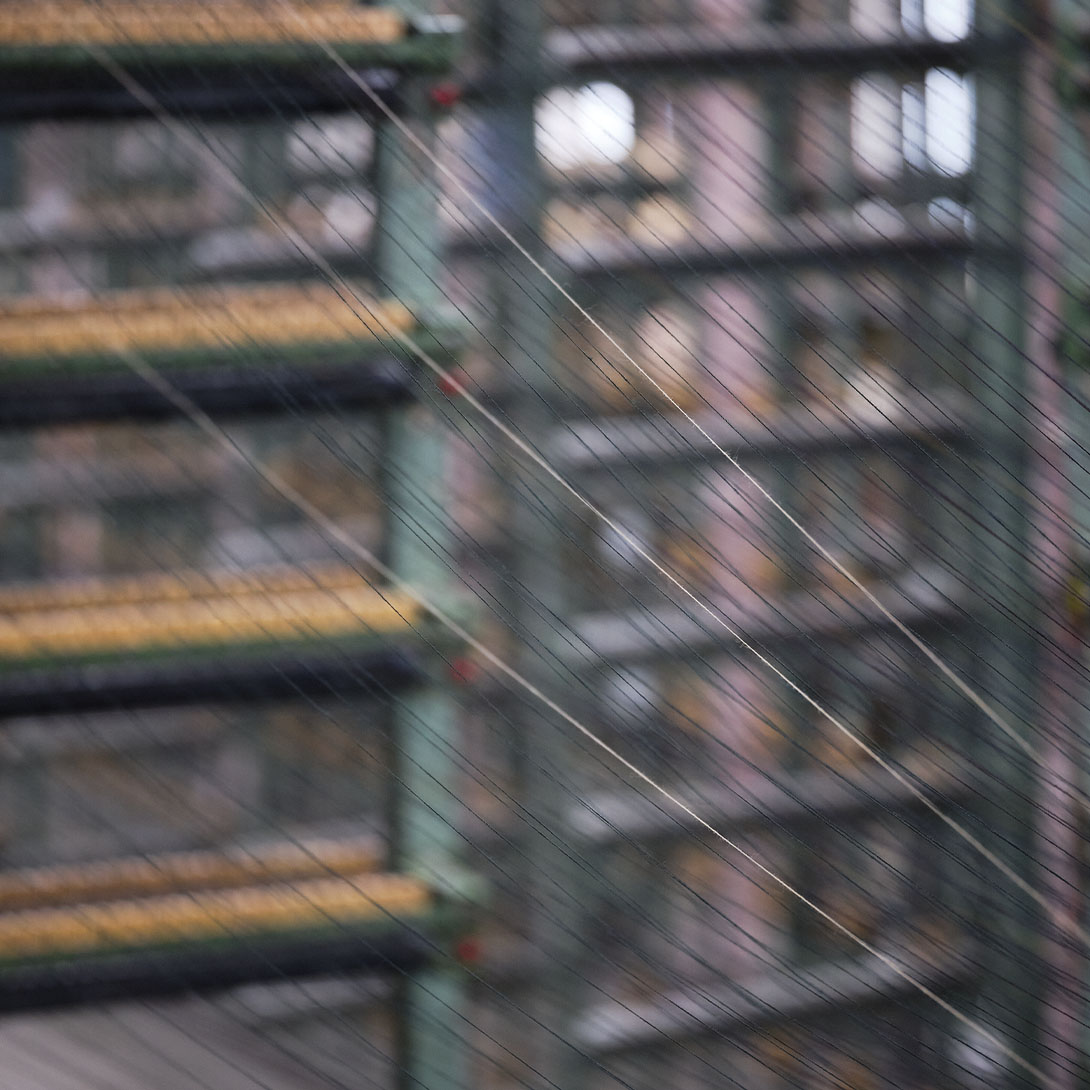
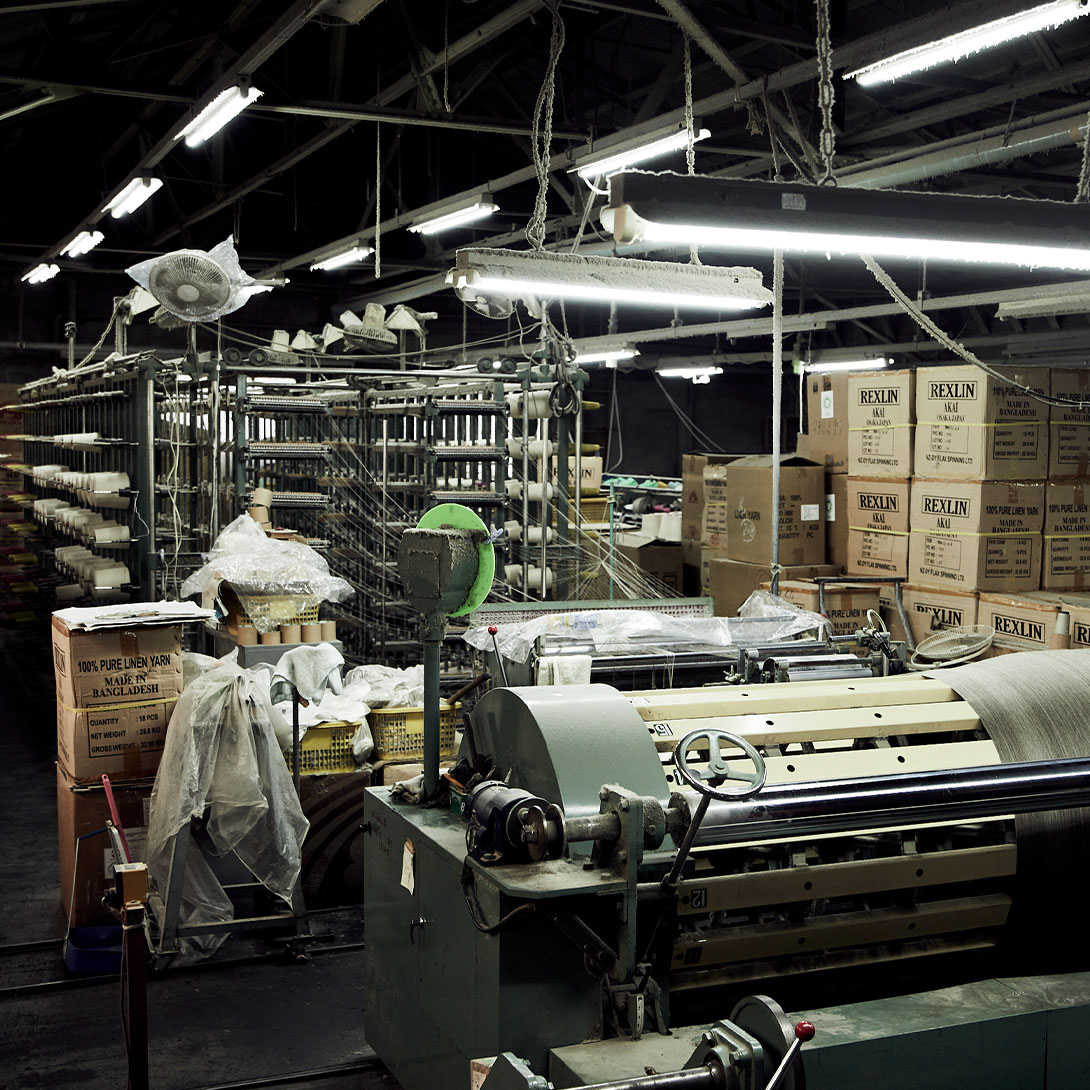
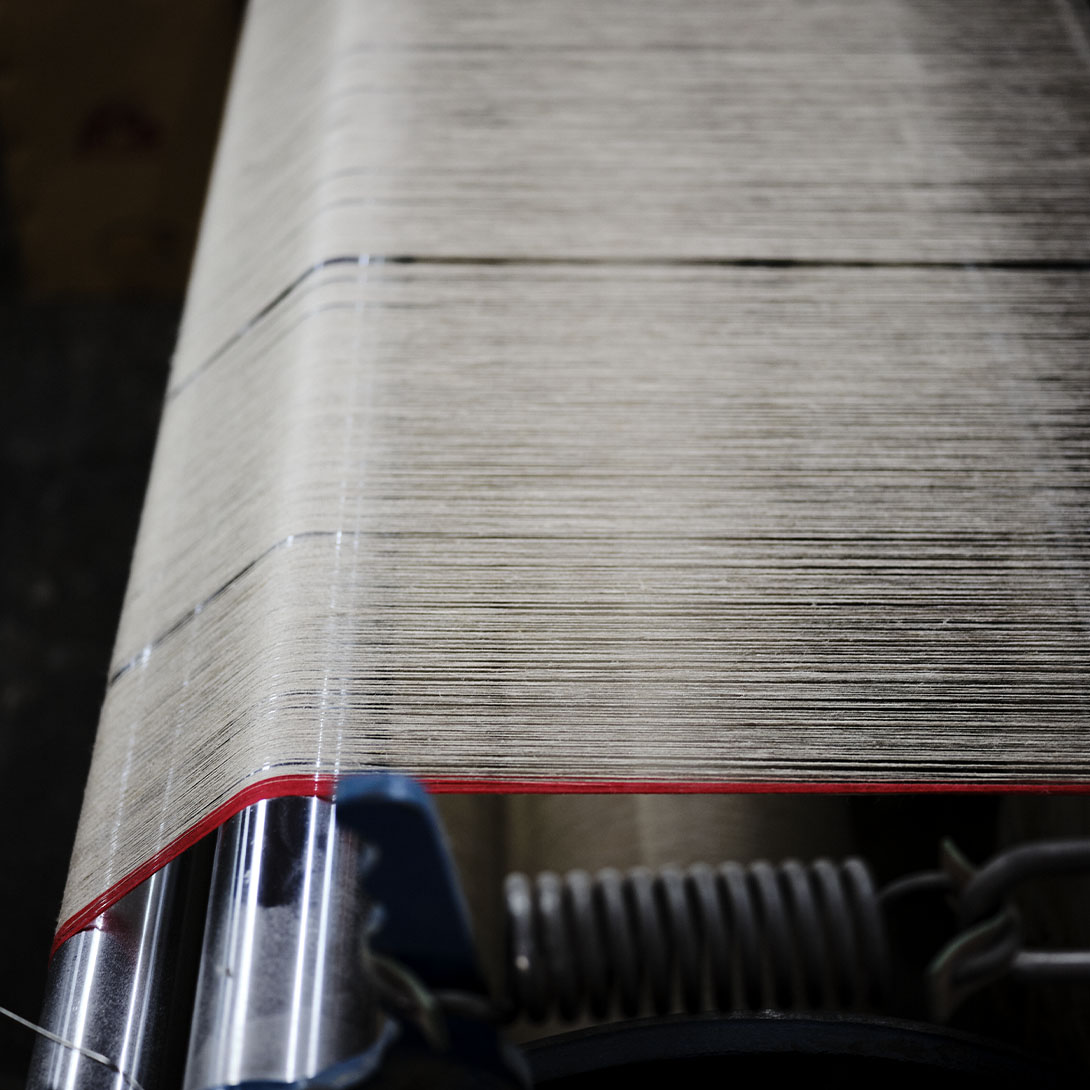
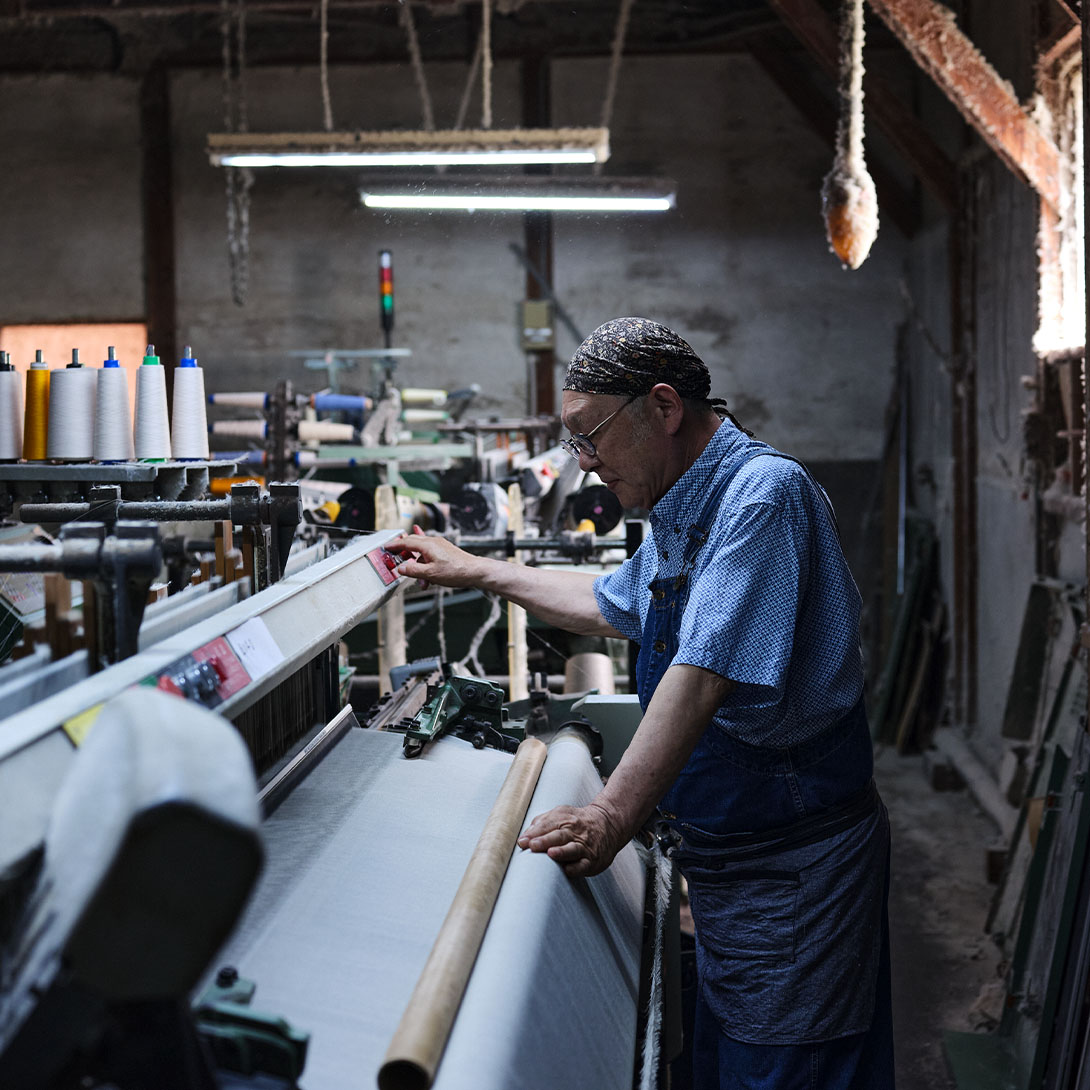
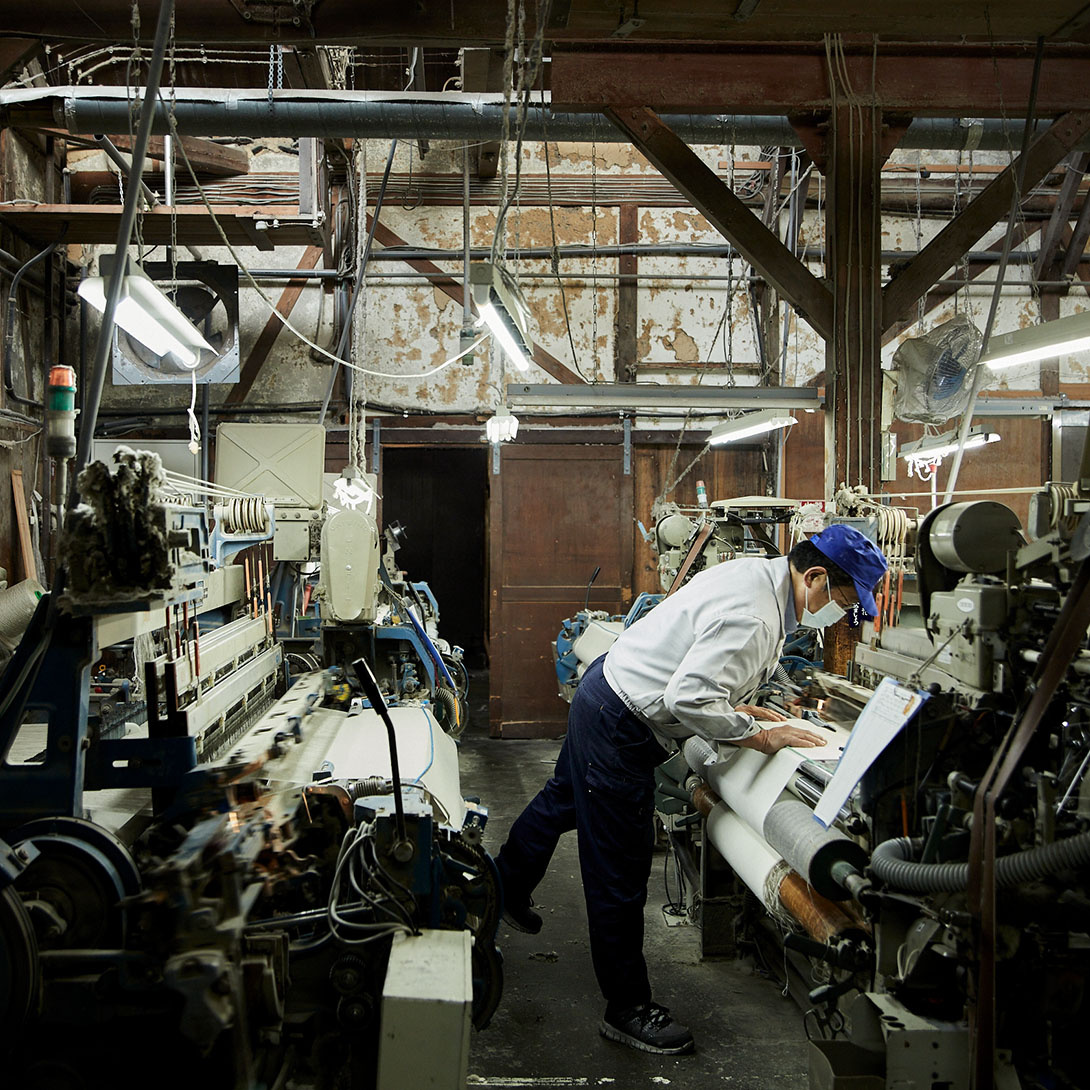
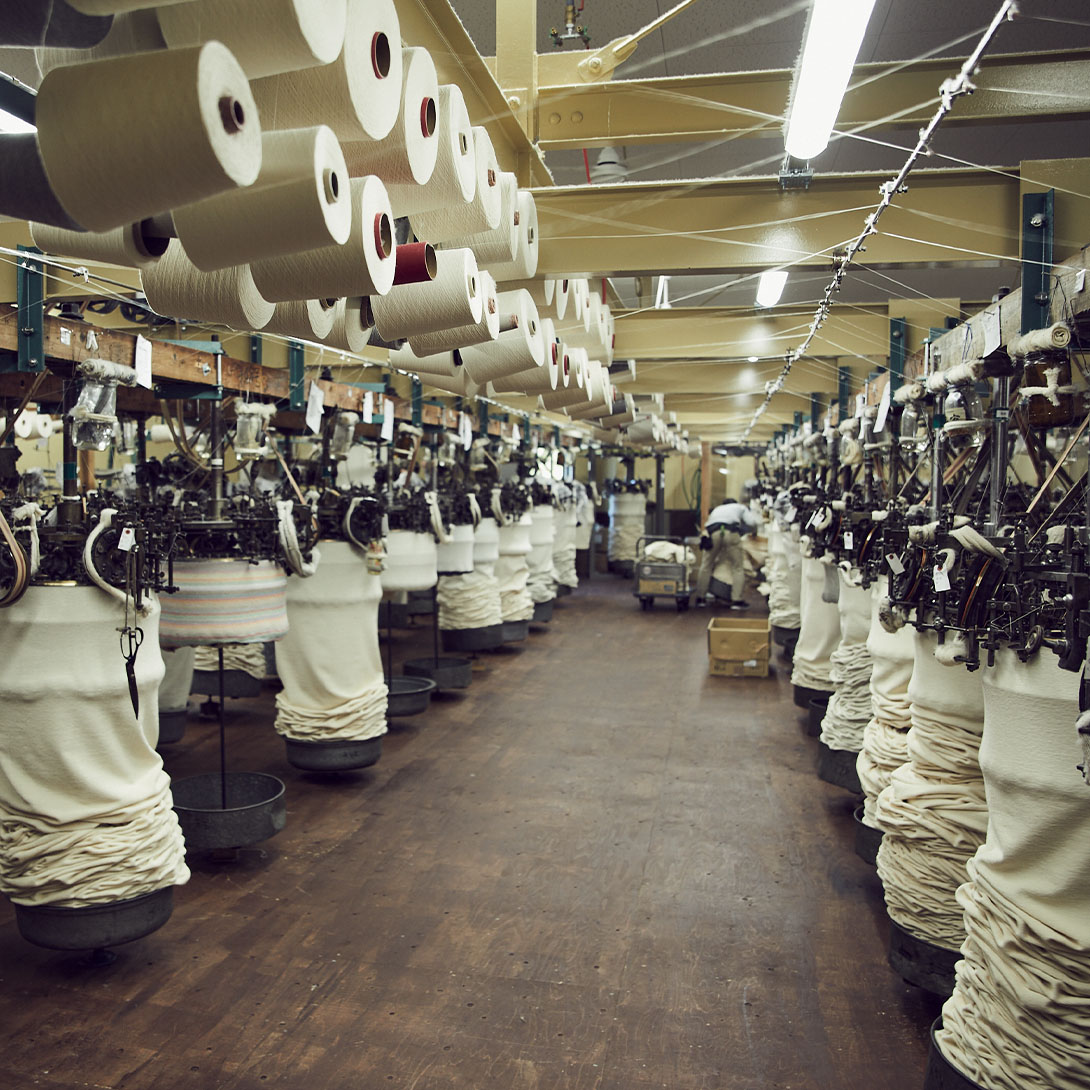
- 編立
-
メリヤス生地を編む
More
スウェットや T シャツなどのような生地をメリヤス(天竺)生地、カットソー生地といいます。〈ネストローブ/コンフェ クト〉では、なかでも吊り編み生地を多く使っています。吊り編み機というのは、上から吊るされ、回転しながら筒状に生地が編まれていく旧式の編み機のこと。糸に余計なテンションをかけずに編んでいくため、ふわっとふくらみのある生地ができます。伸縮性がいいので肌馴染みがよく、着心地は最高。長年着ていても生地がやせてこないし、機械の針の先端が丸く、糸を傷付けないので、生地へ の負荷が少ないのも特長です。4 0 ~ 6 0 年代のヴィンテージのスウェットや T シャツの多くは吊り編み機で作られていたため、この機械で作るとどこ か古着のような風合いになるのです。
ただし今は機械の製造は既に終了しており、日本で現役で使われているのは3社のみ。職人が大事にメンテナンスをしながら稼働させていますが、その技術を持つ職人も少なく、とても貴重な生地なのです。
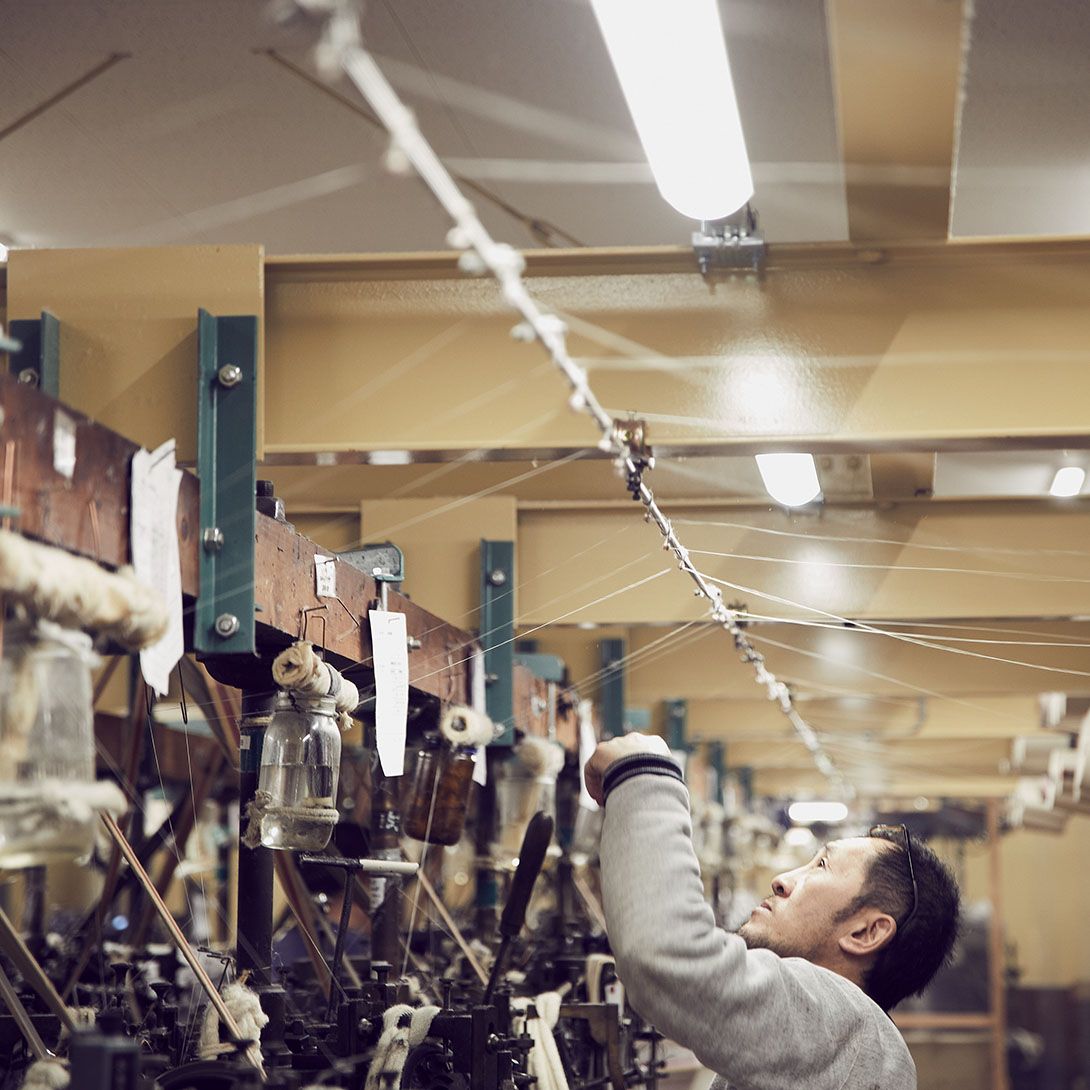
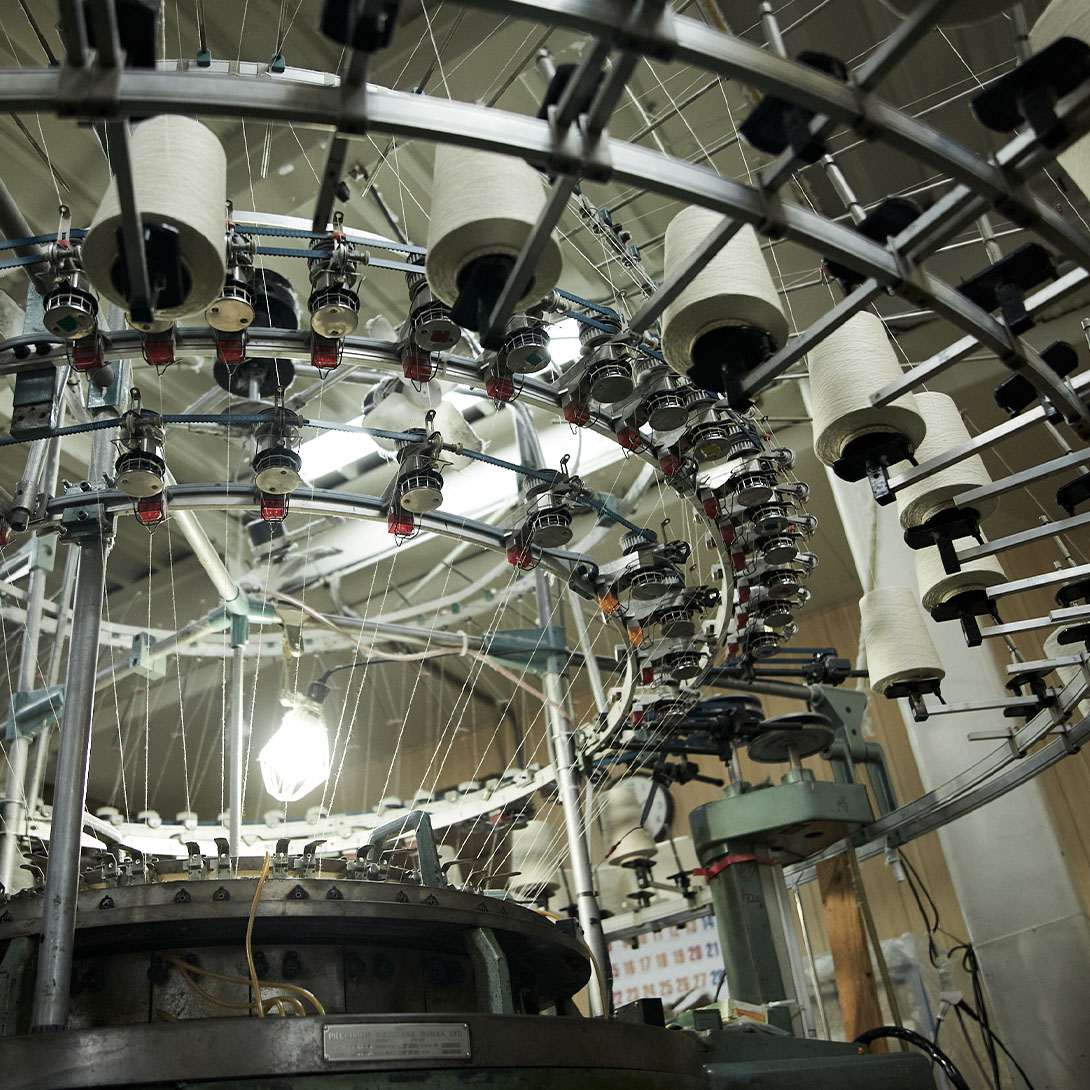
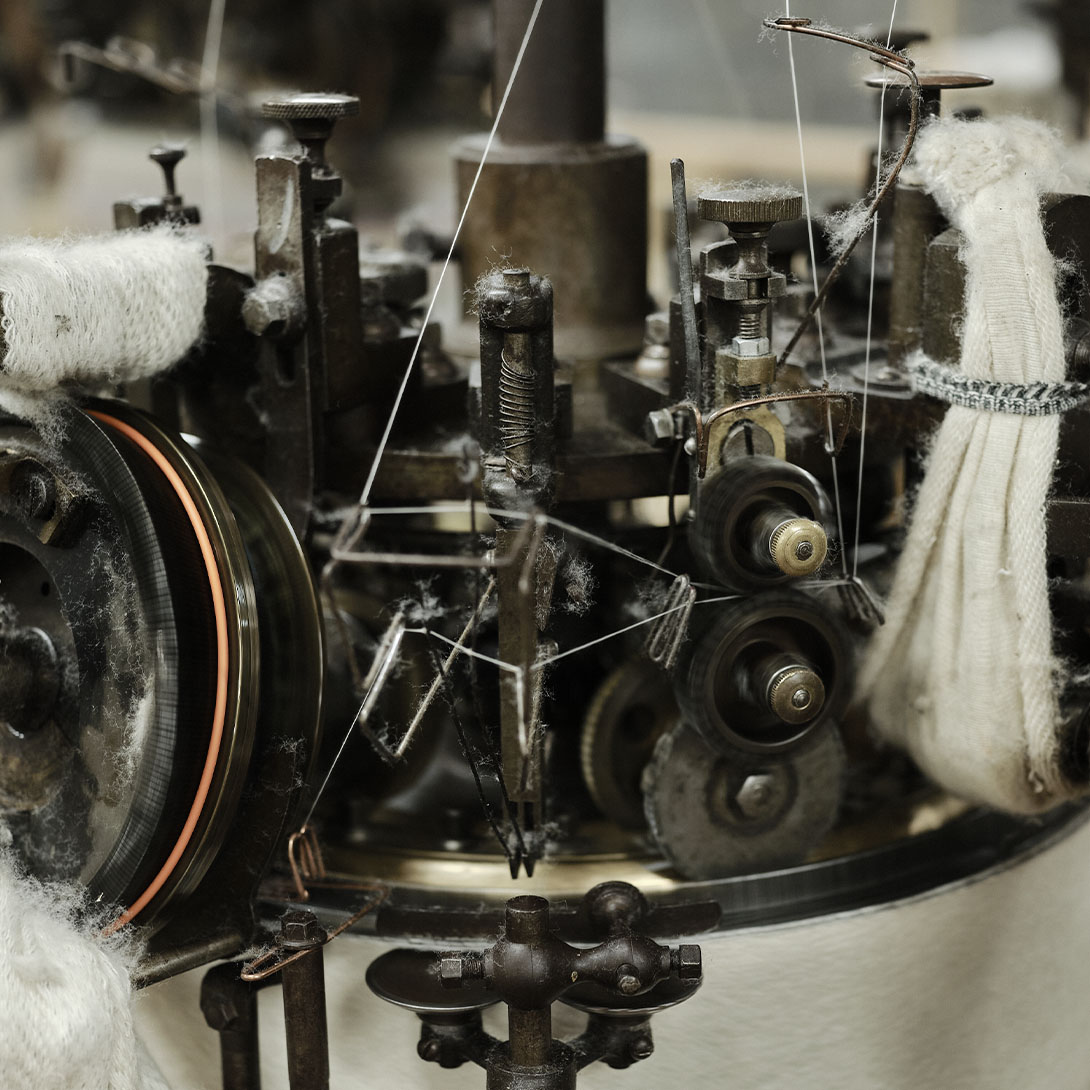
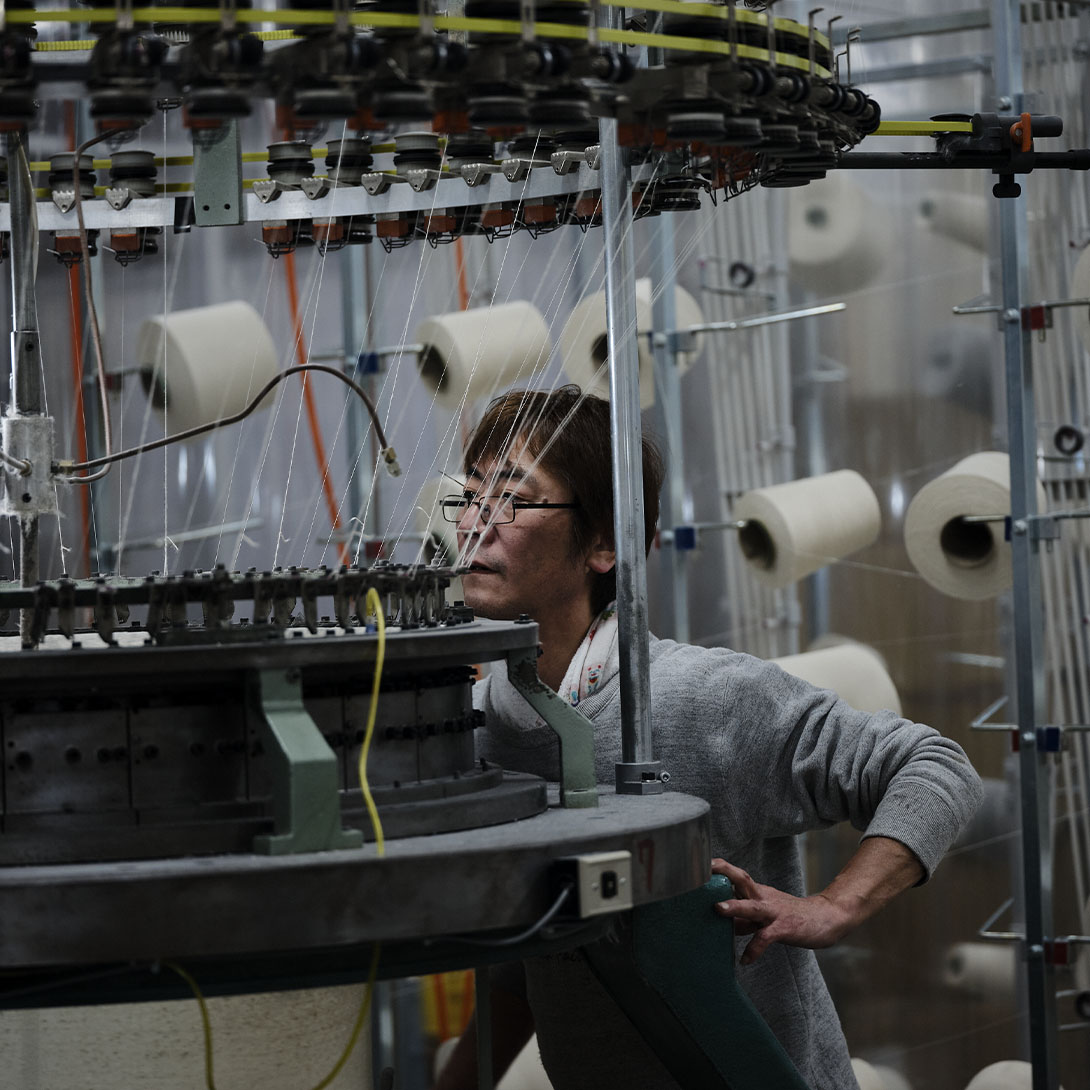
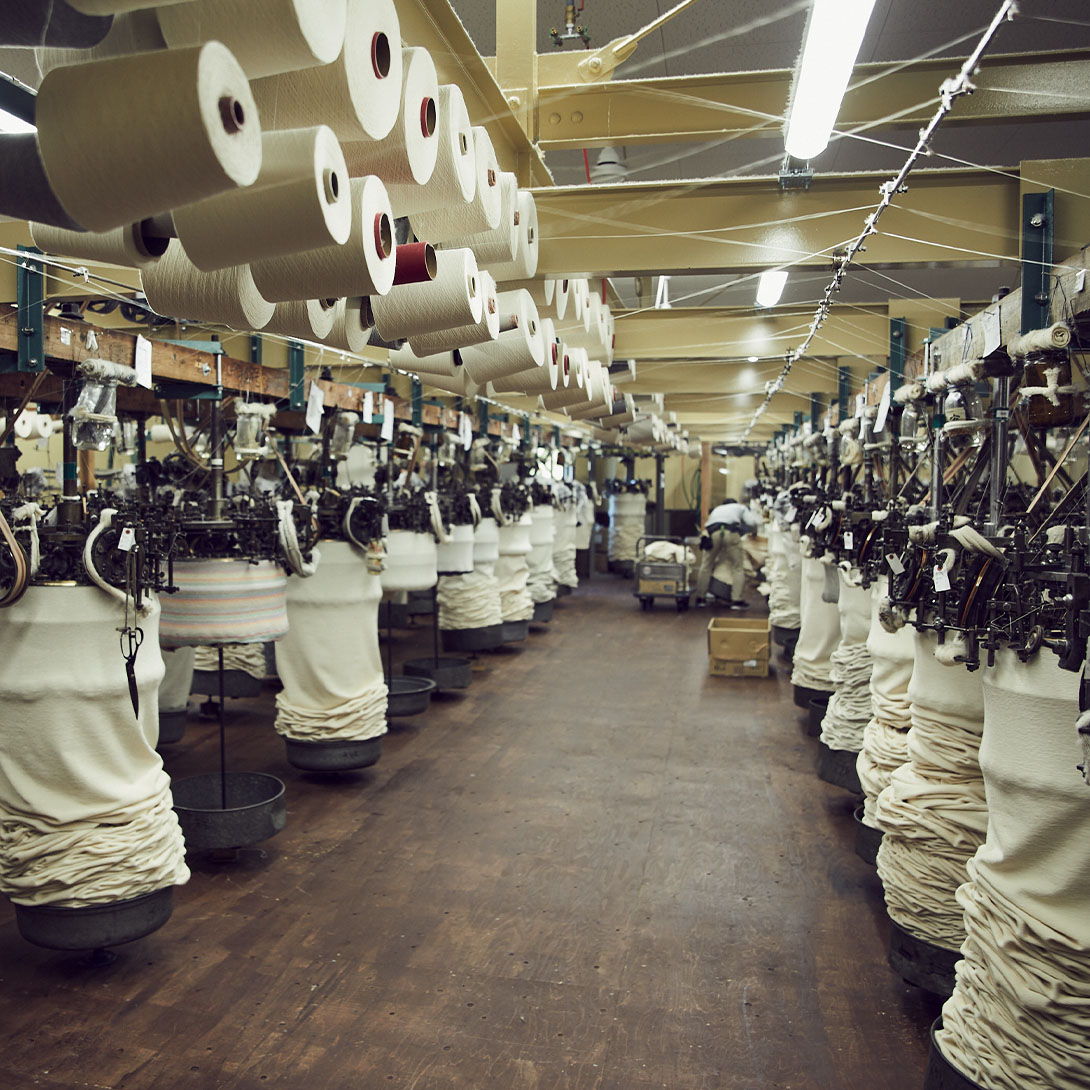
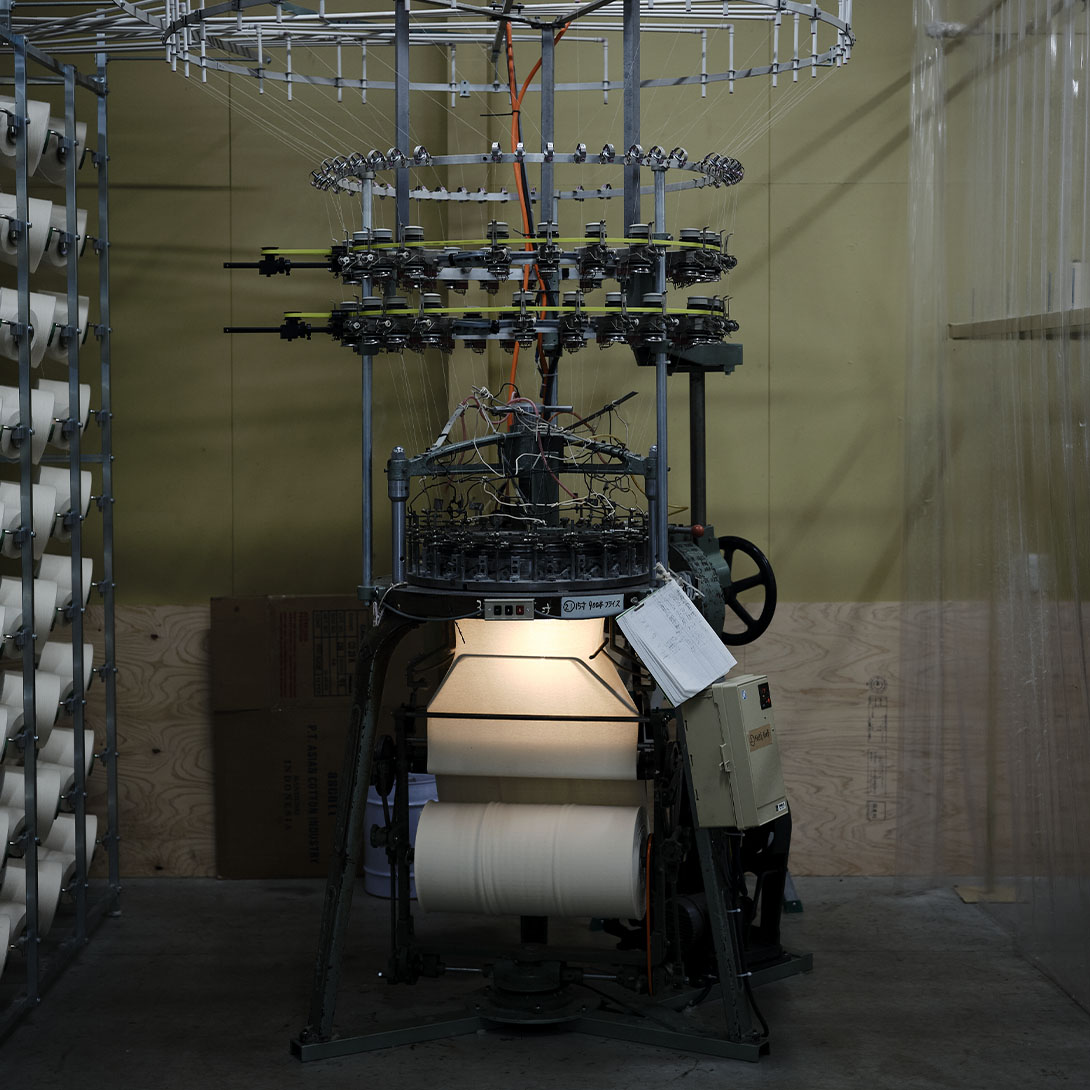
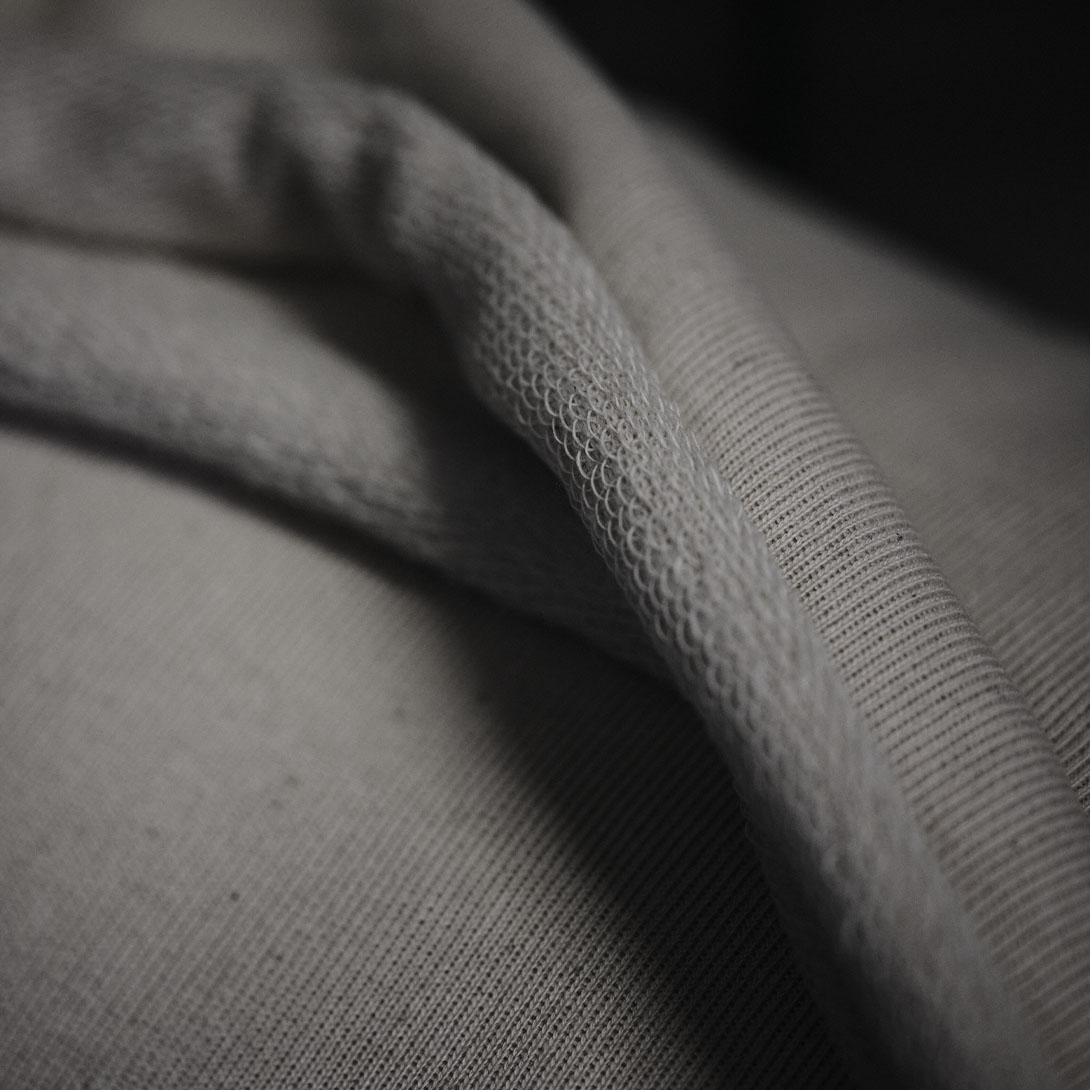
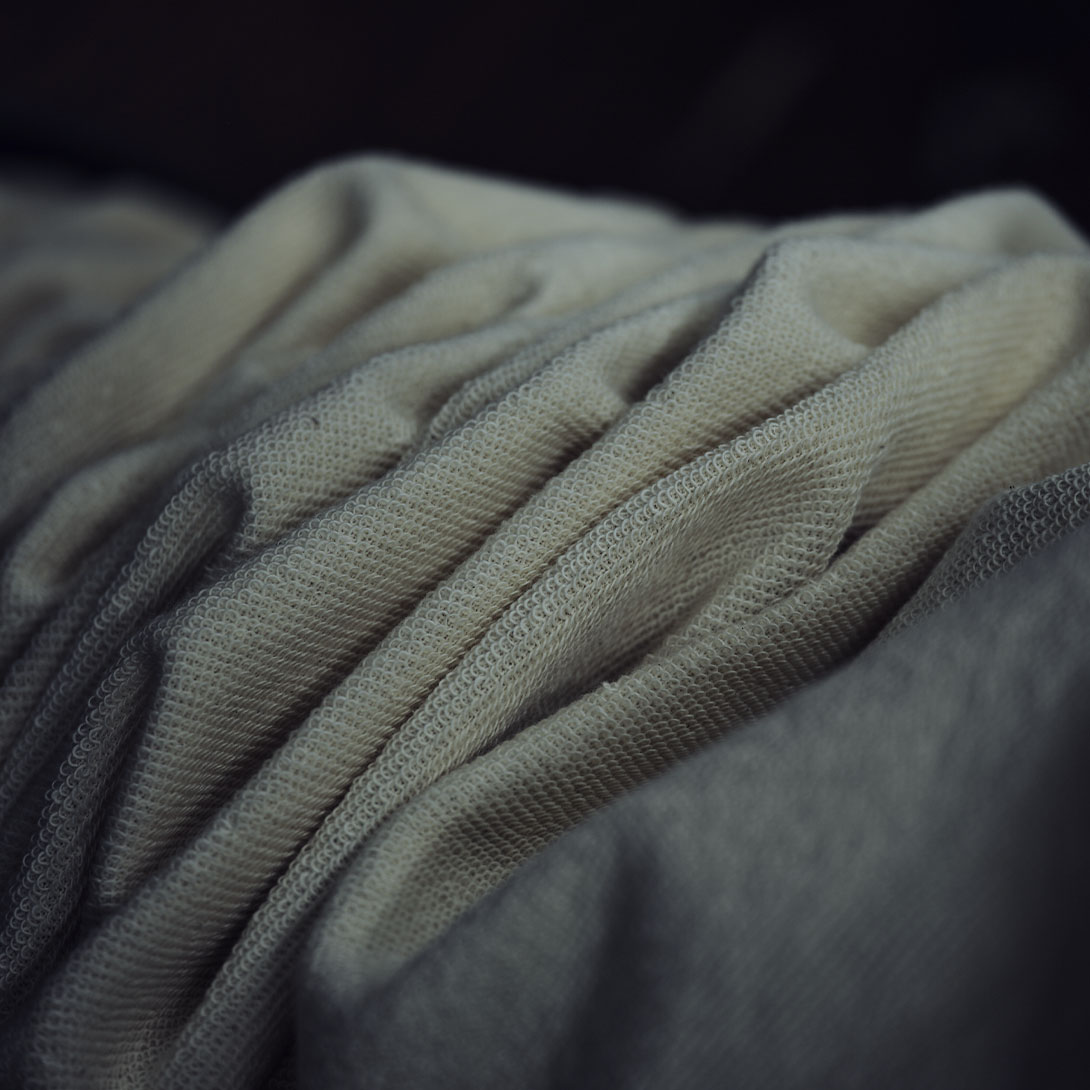

- 整理
-
生地に加工をする
More
織り上がった生地は、のり抜きや毛羽焼き、精錬といった整理作業をします。〈ネストローブ/コンフェ クト〉の多くの生地の整理加工を担当している〈大長〉は、古くから近江上布という麻の製織、染色、仕上加工を手がけてきた老舗。古来から大麻や苧麻を着用してきた日本で、そのゴワゴワと硬い繊維を柔らかくしたり、染めやすくしたりする晒しという技術を生かせるのは、麻の産地だった近江ならでは。
また生地を染める場合も、糸からこだわって織ってもらった天然素材の持つ豊かな表情を最大限に活かすべく、釜染めしてから天日干しをしています。「釜」と呼ばれている大きな洗濯機のようなワッシャー機の中に染料と精錬した白生地を入れ、正転と反転を繰り返しながら温度を上げ、染めますが、生地にテンションをかけないので、15 ~ 20% 近く縮みます。機械のなかで回転するうちにくしゃくしゃになるので、多少のムラや染料溜まり、特有のシボも出て、それが風合いになるのです。それを機械的な圧力や張力をかけることなく、天日干しでふっくらと乾燥させています。
ときにはさらに生地の表面を植物の実の刺でかき上げて、起毛加工を施すことも。
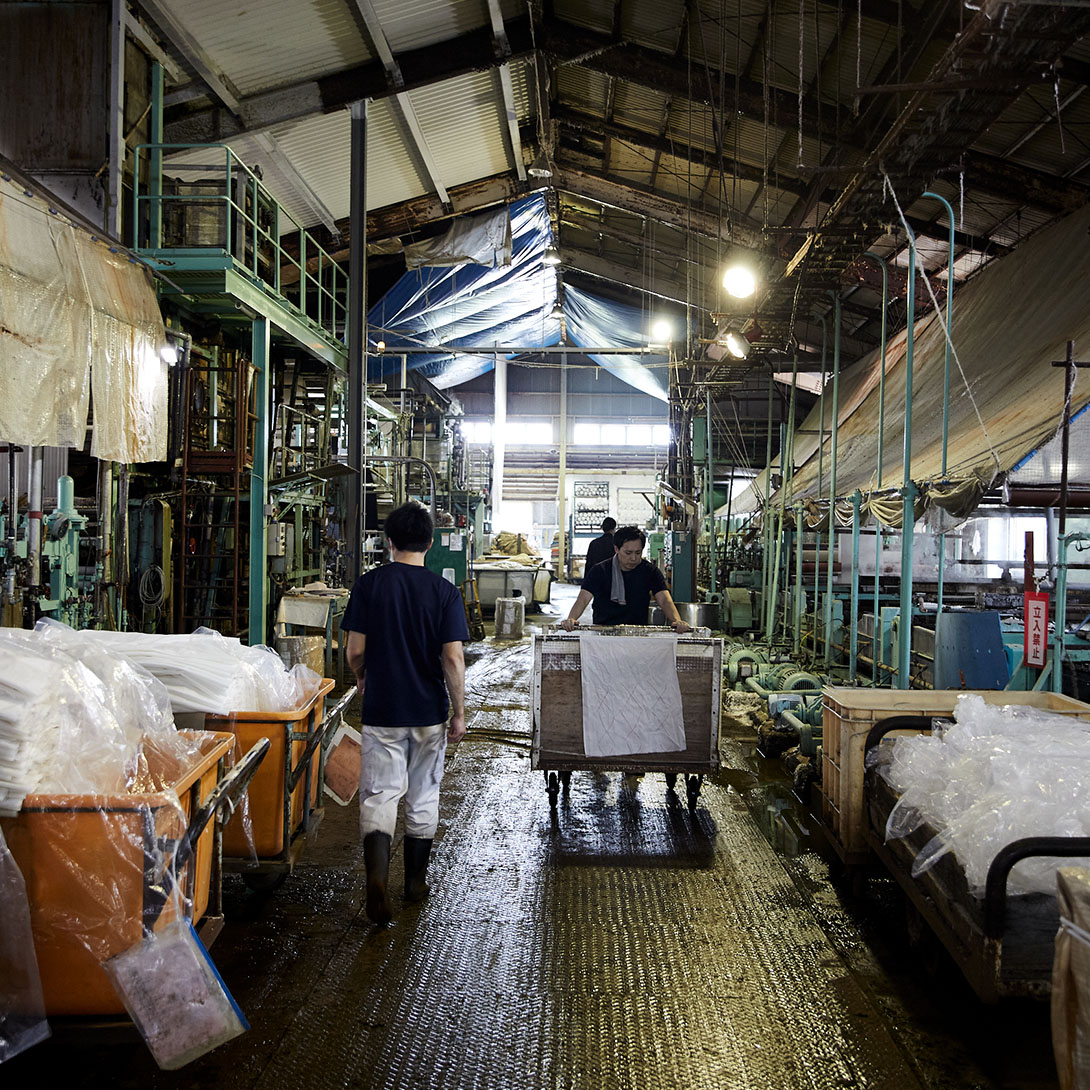
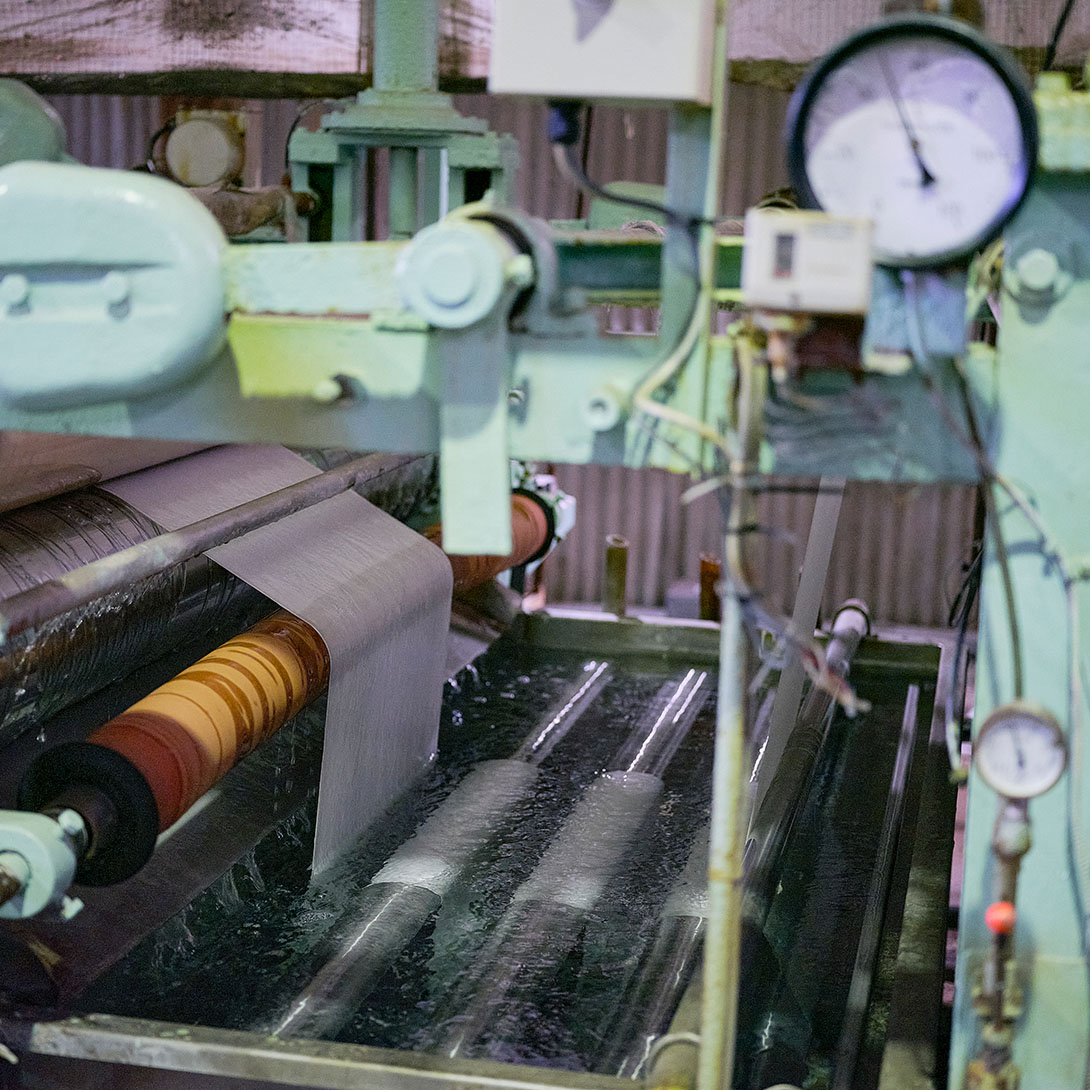
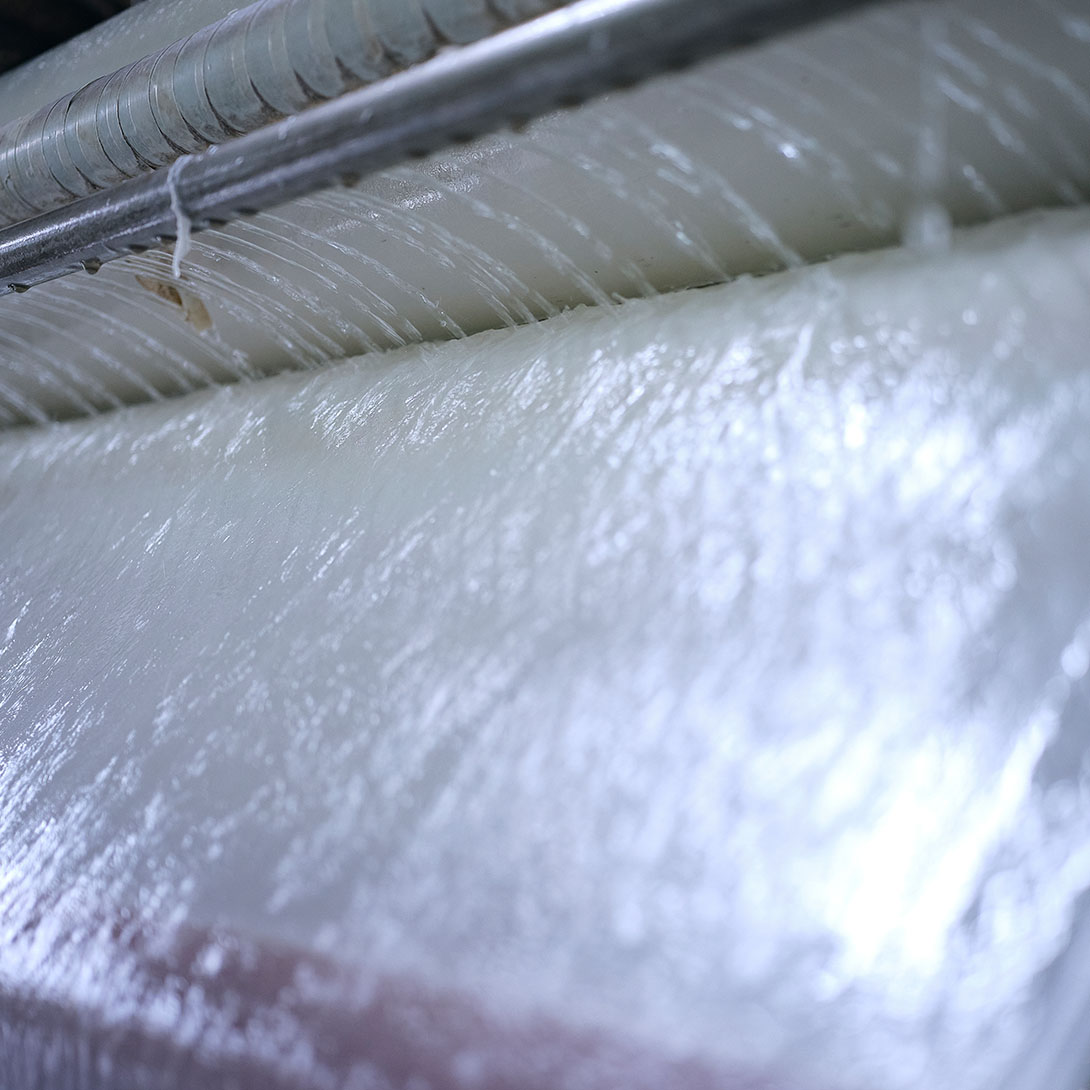
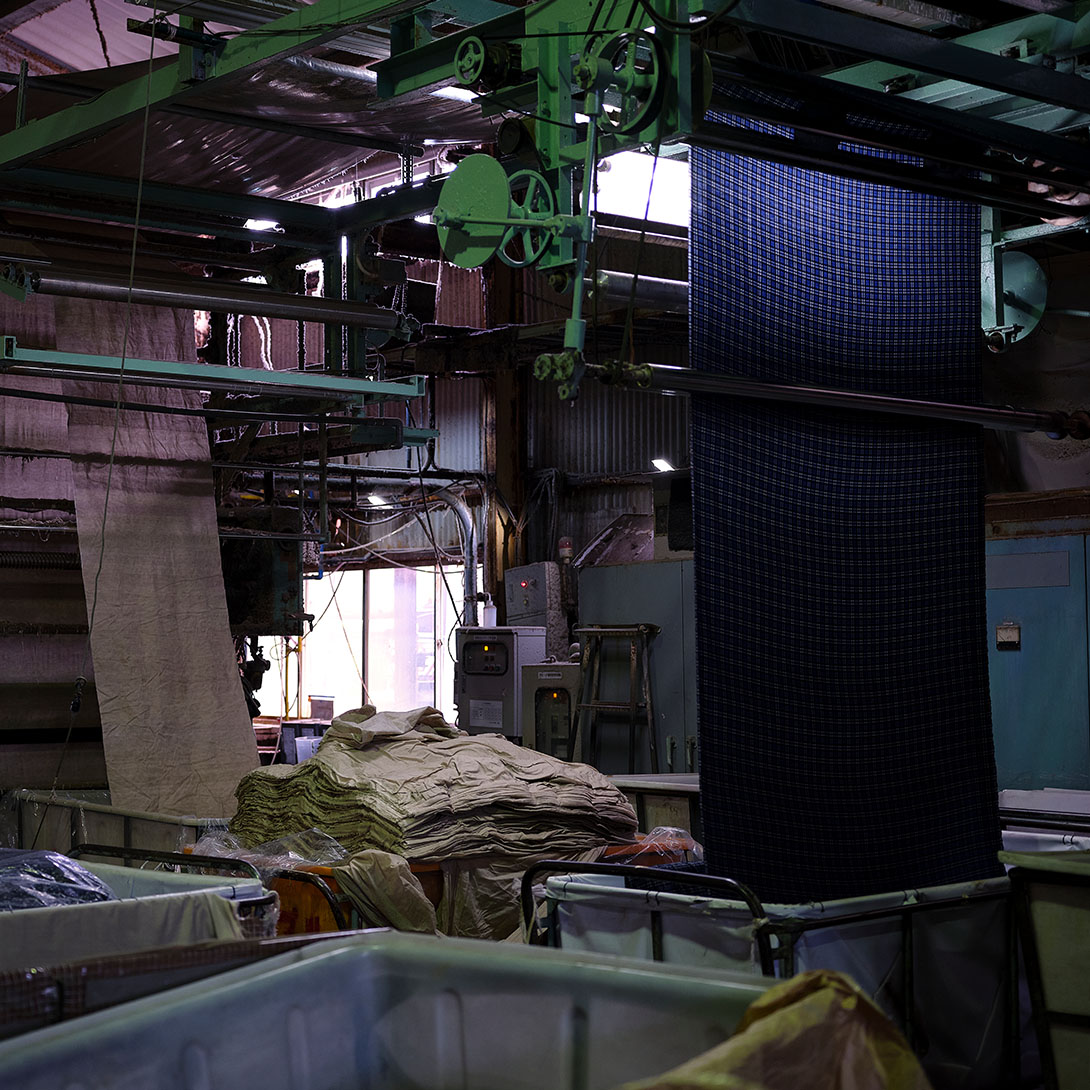
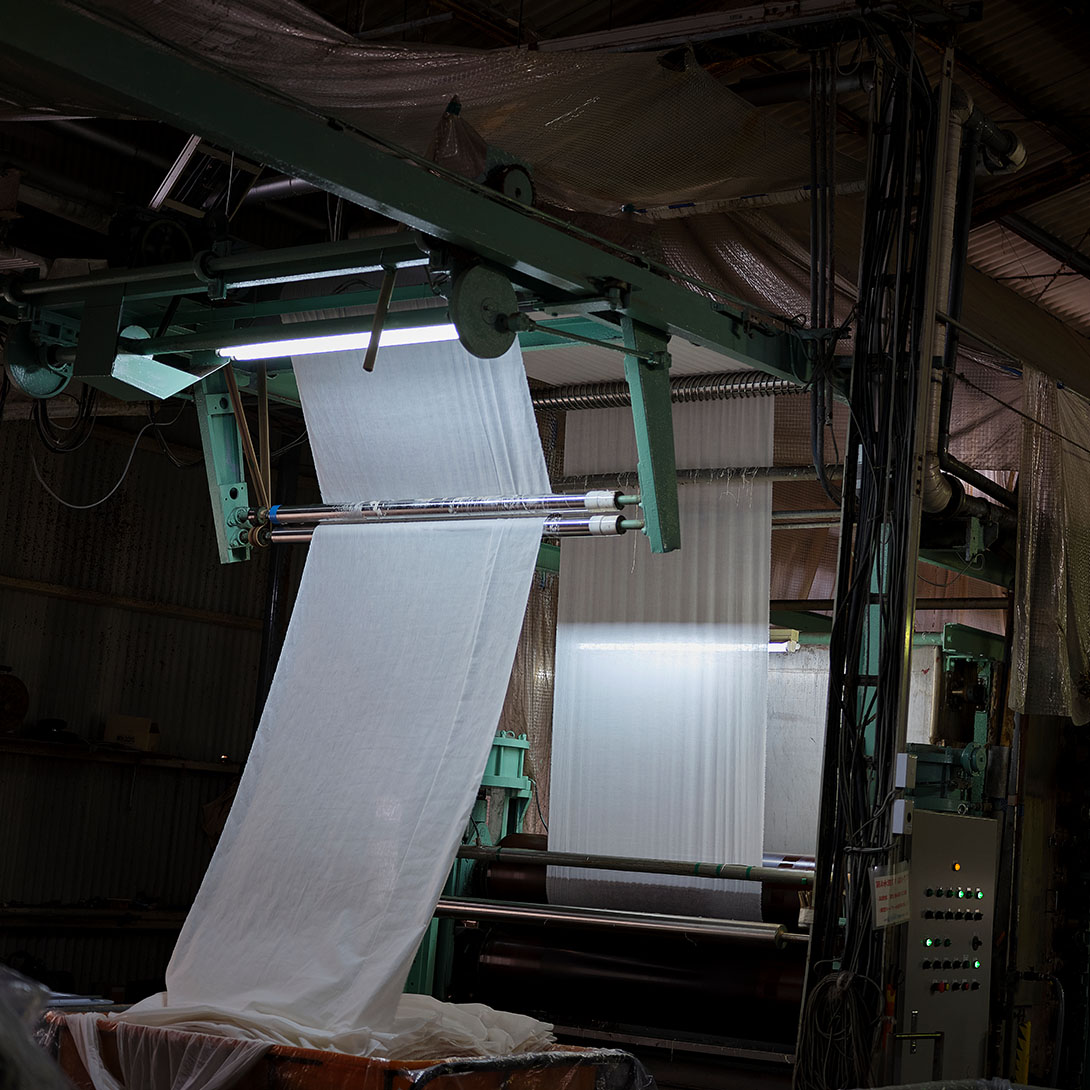
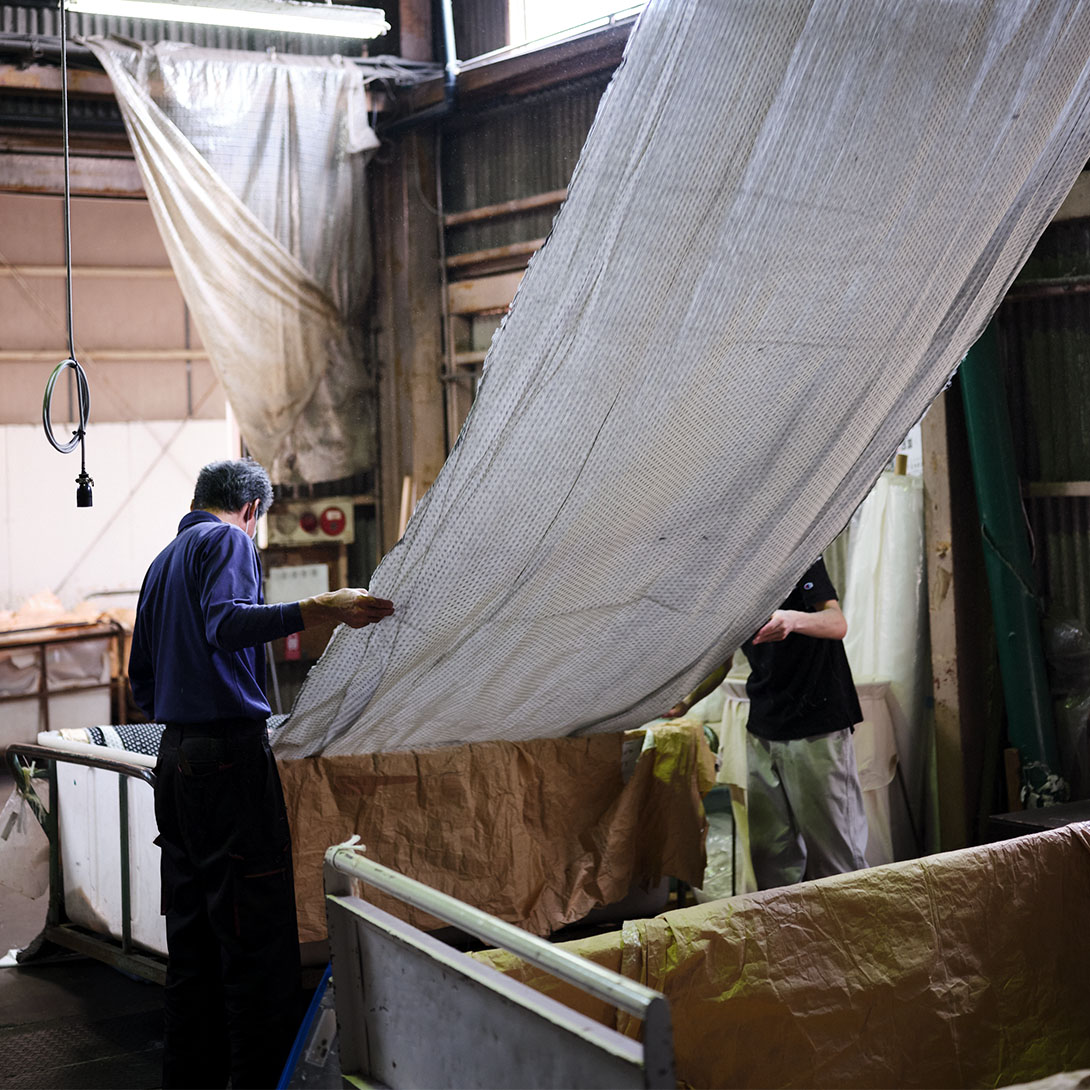
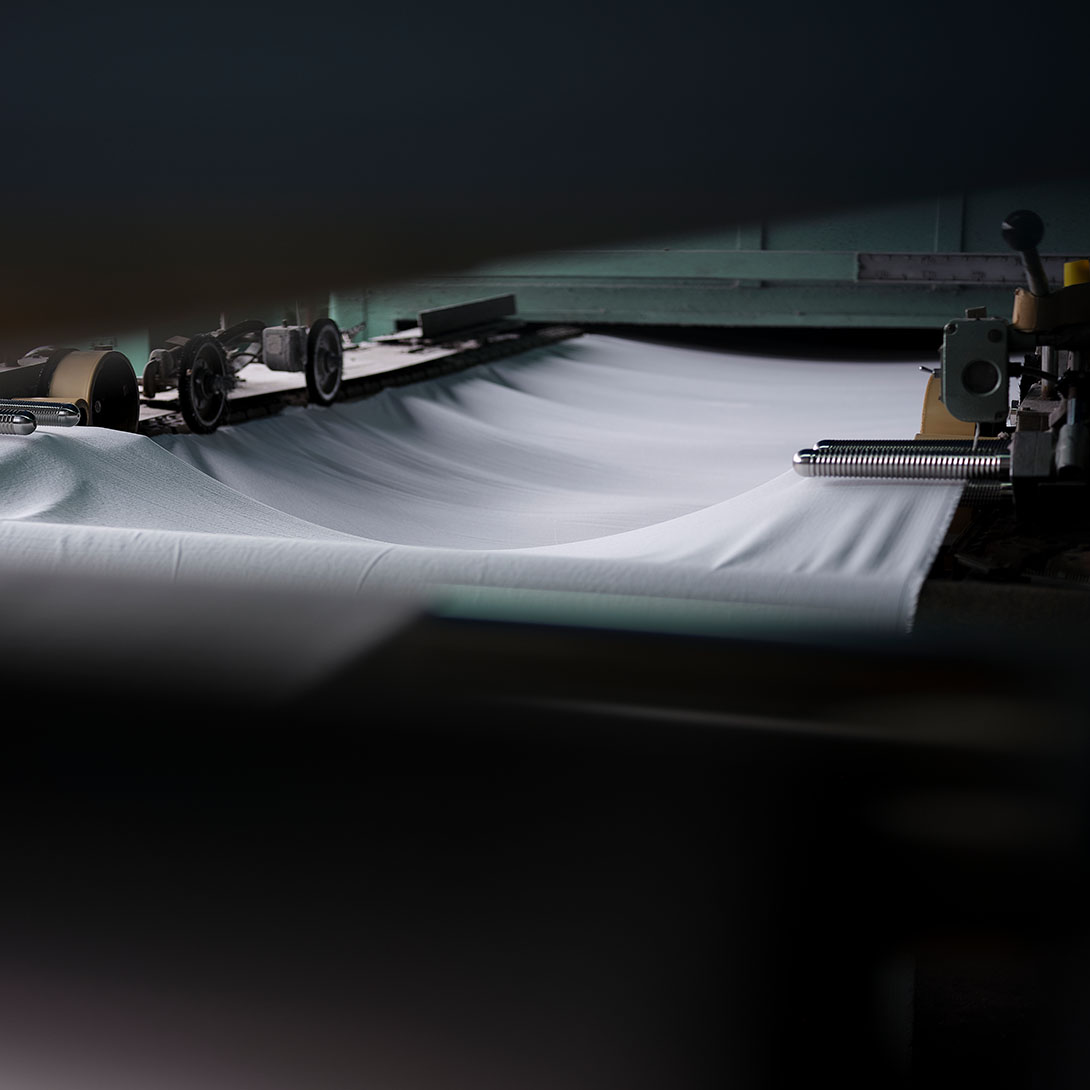
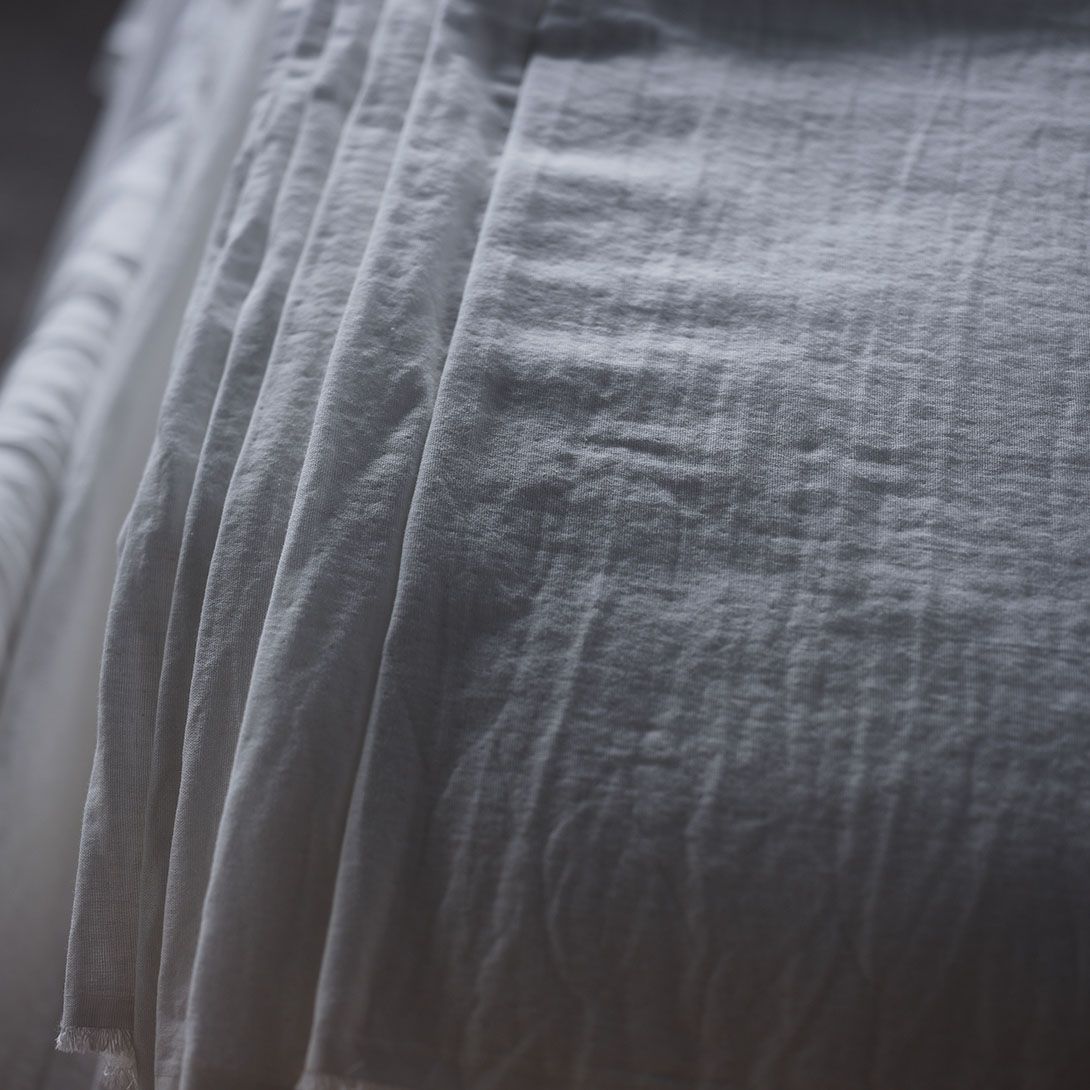
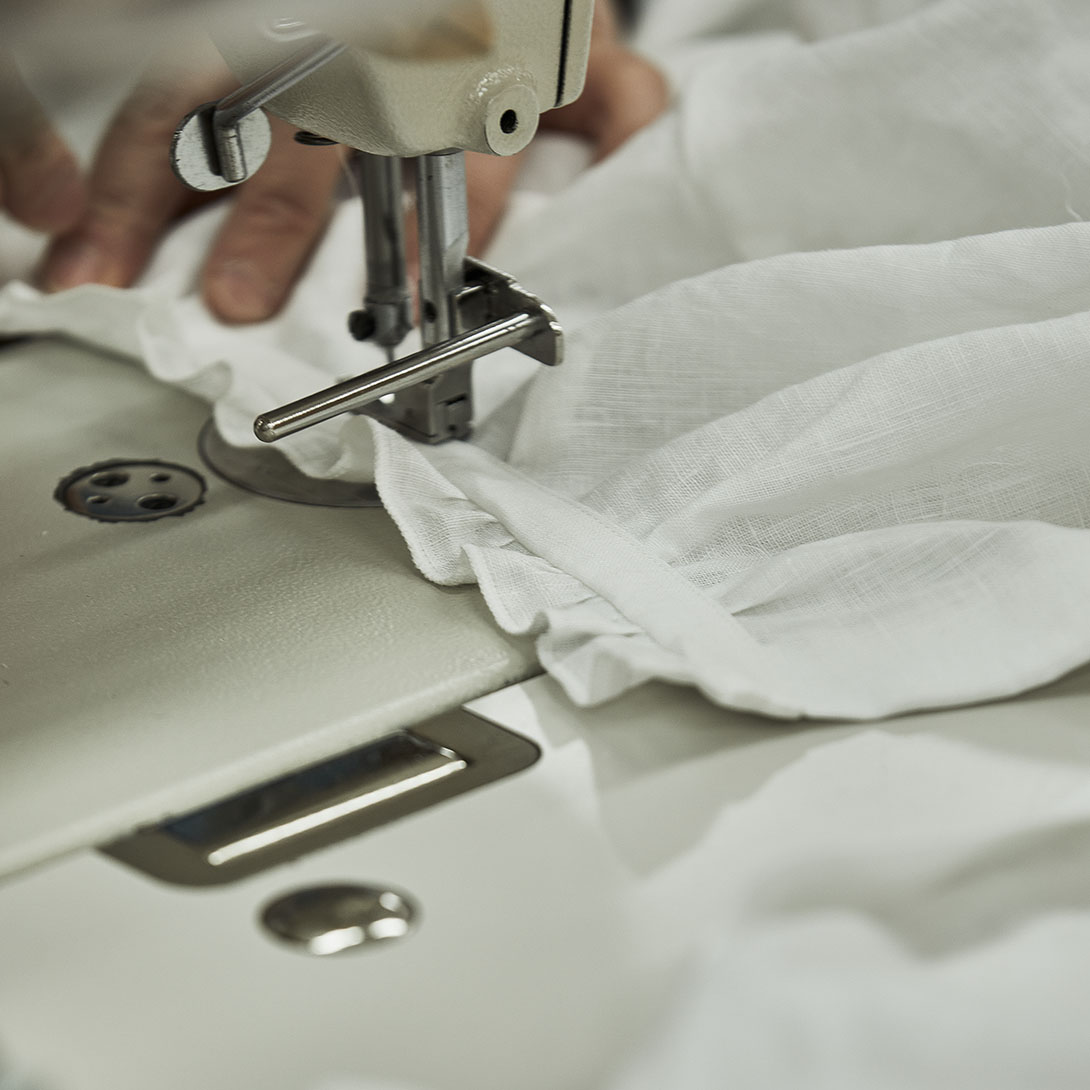
- 縫製
-
縫い上げて服に仕立てる
More
縫製工場ではまず最初に、たくさんの生地を一気に裁断できるように生地を延ばし、ズレないように重ねる延反作業をします。それから生地に傷や汚れがないかを確認しながら重ね、型紙を合わせて裁断。
〈ネストローブ/コンフェクト〉 の型は、縫い始めや縫い終わり、パーツごとを合わせる際の目安になるノッチや、人の体のカーブに添わせるための「縮めて縫いなさい」という指示であるイセが多いのも特徴です。これによって縫製は難しくなるし、作業スピードは落ちてしまうけれど、仕上がりと着心地が断然良くなるのです。微妙な調整がいる手仕事だから、熟練した職人の腕が必要となります。
〈ネストローブ/コンフェクト〉のクオリティを支えているのは、こういった一つ一つのこだわりと、それを実現してくれる職人たちなのです。
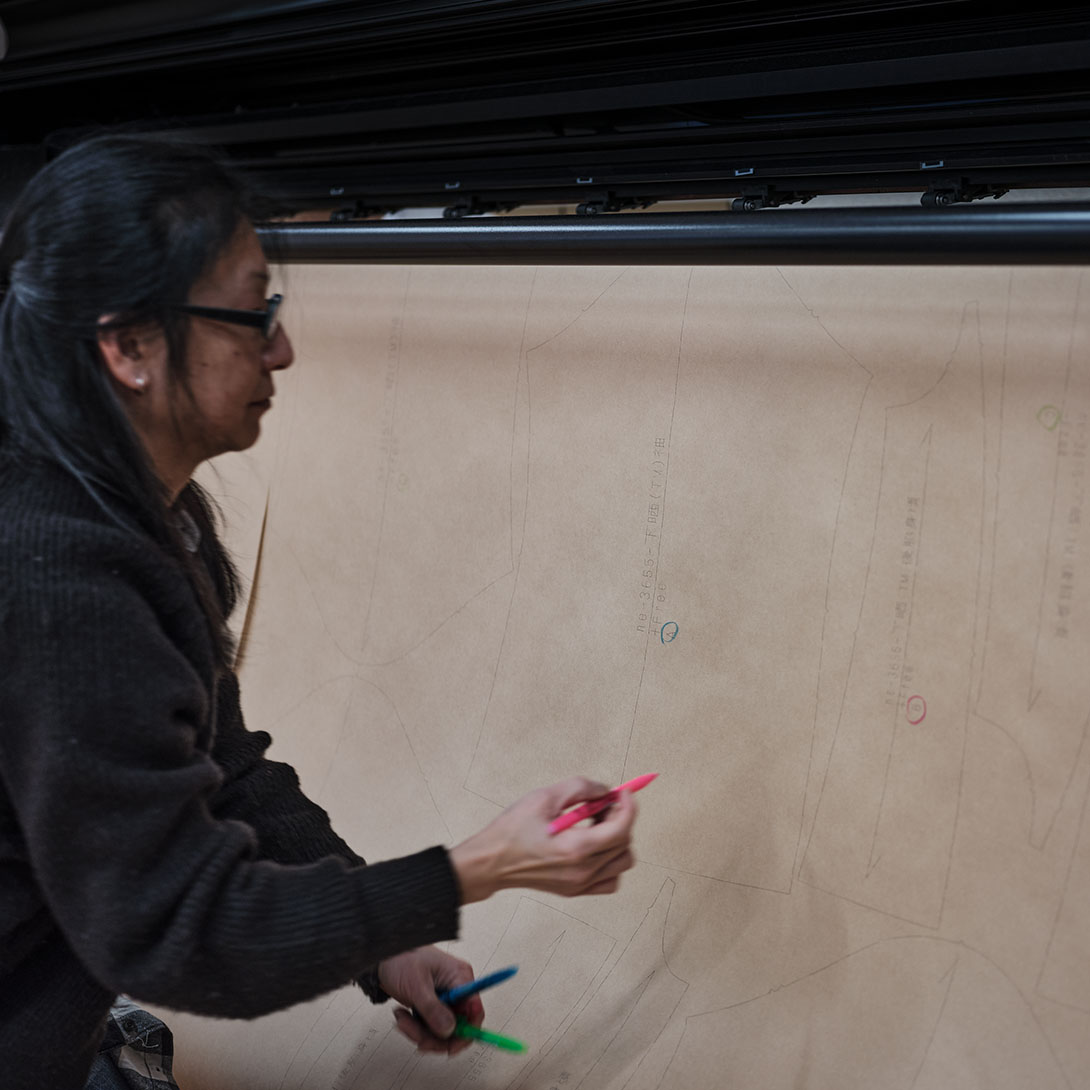
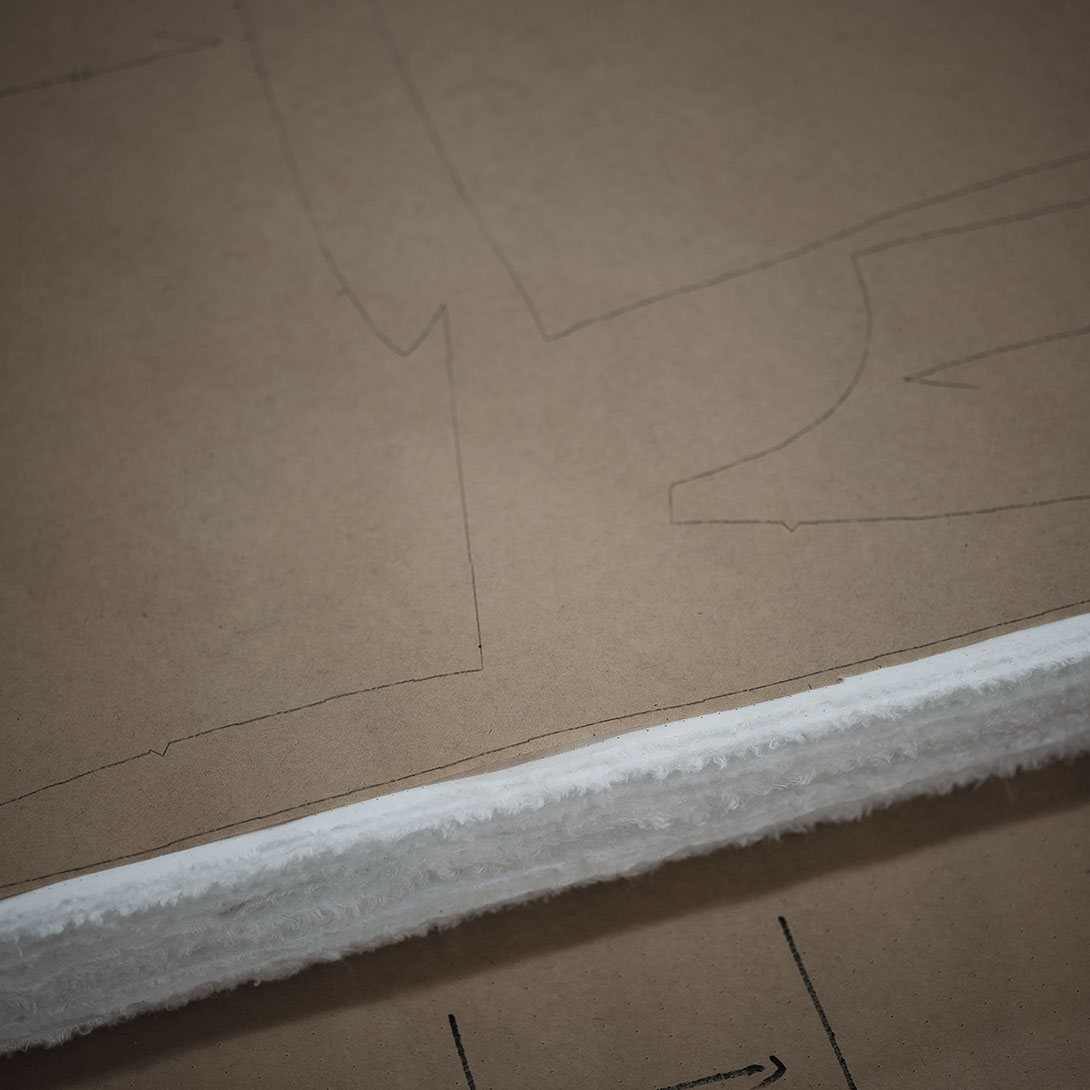
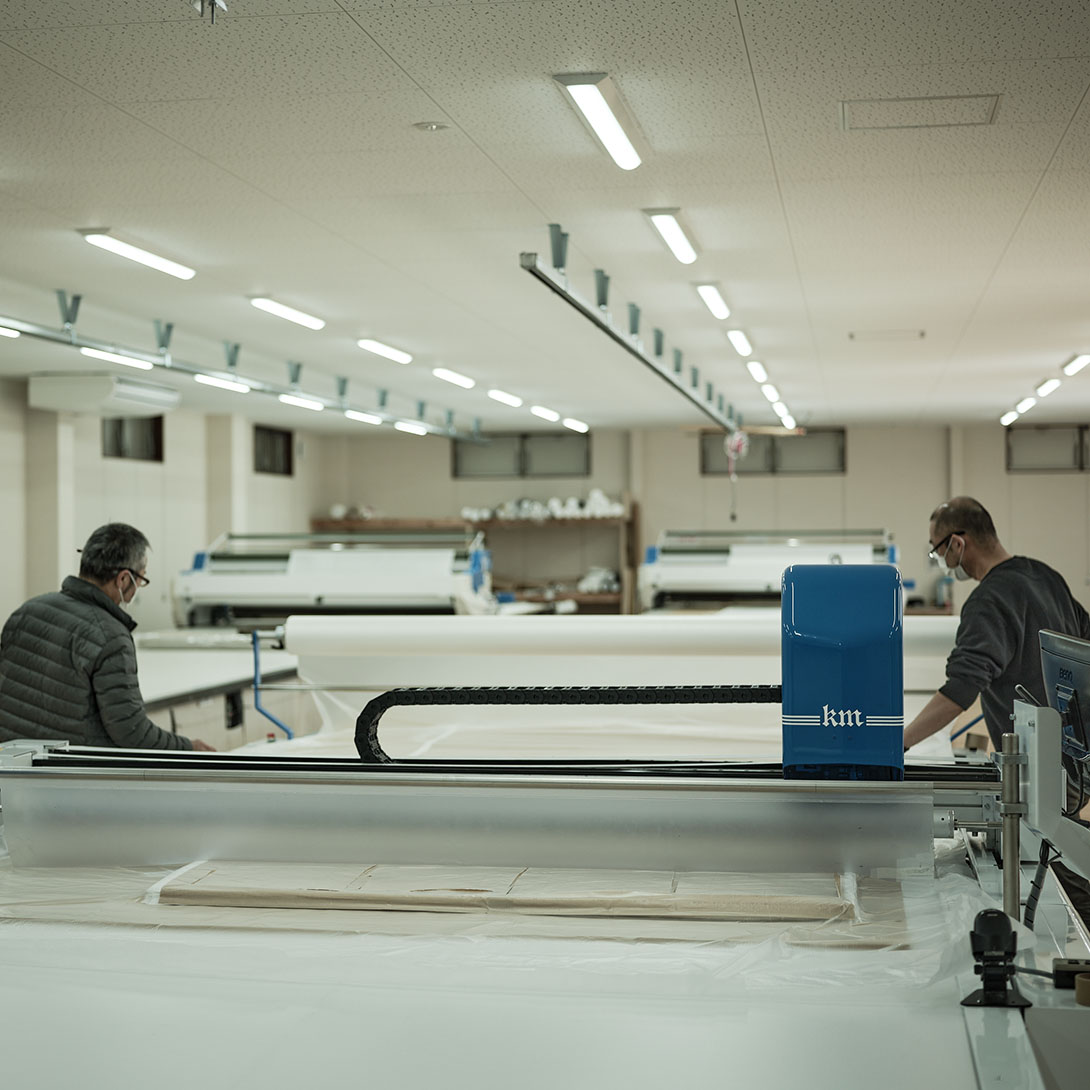
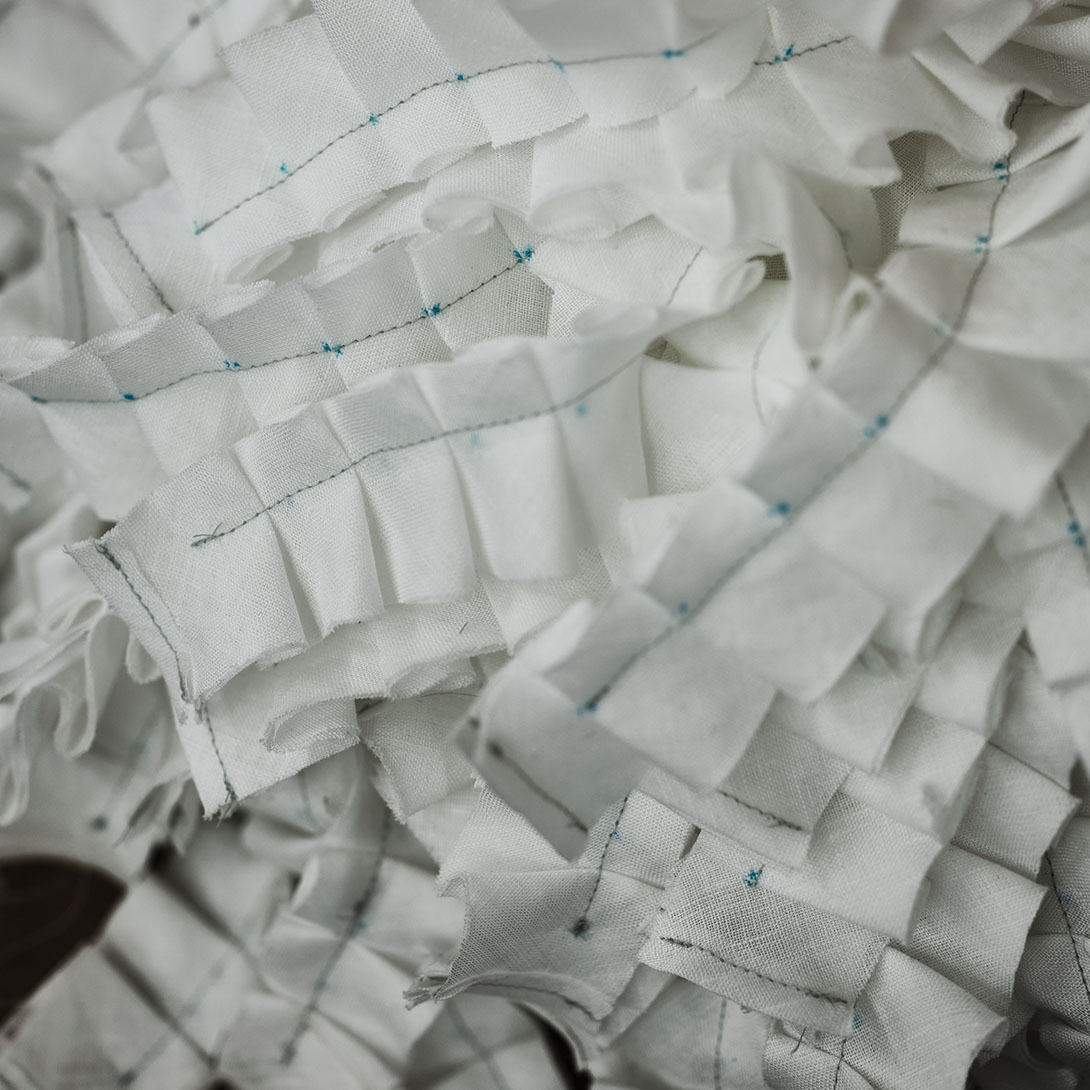
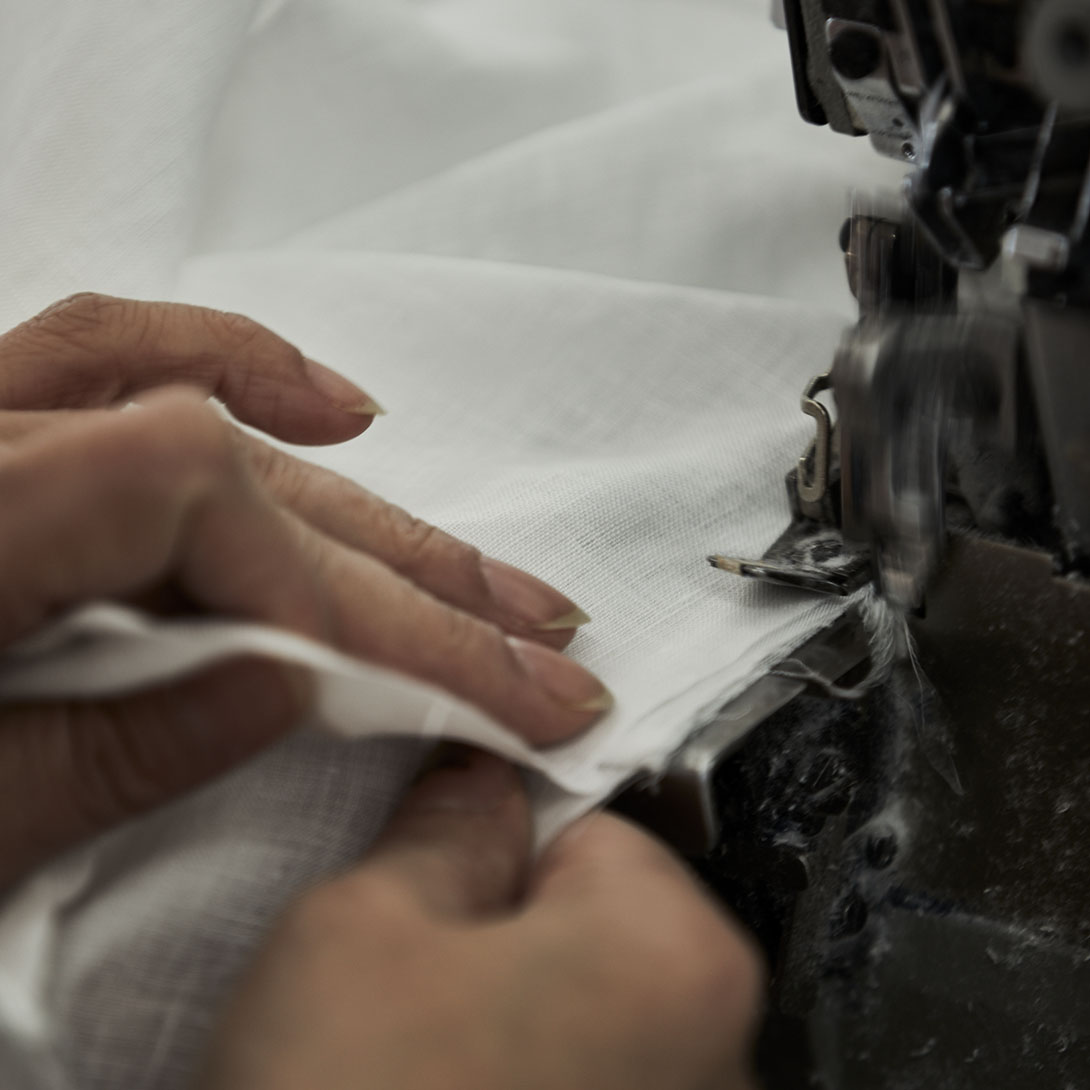
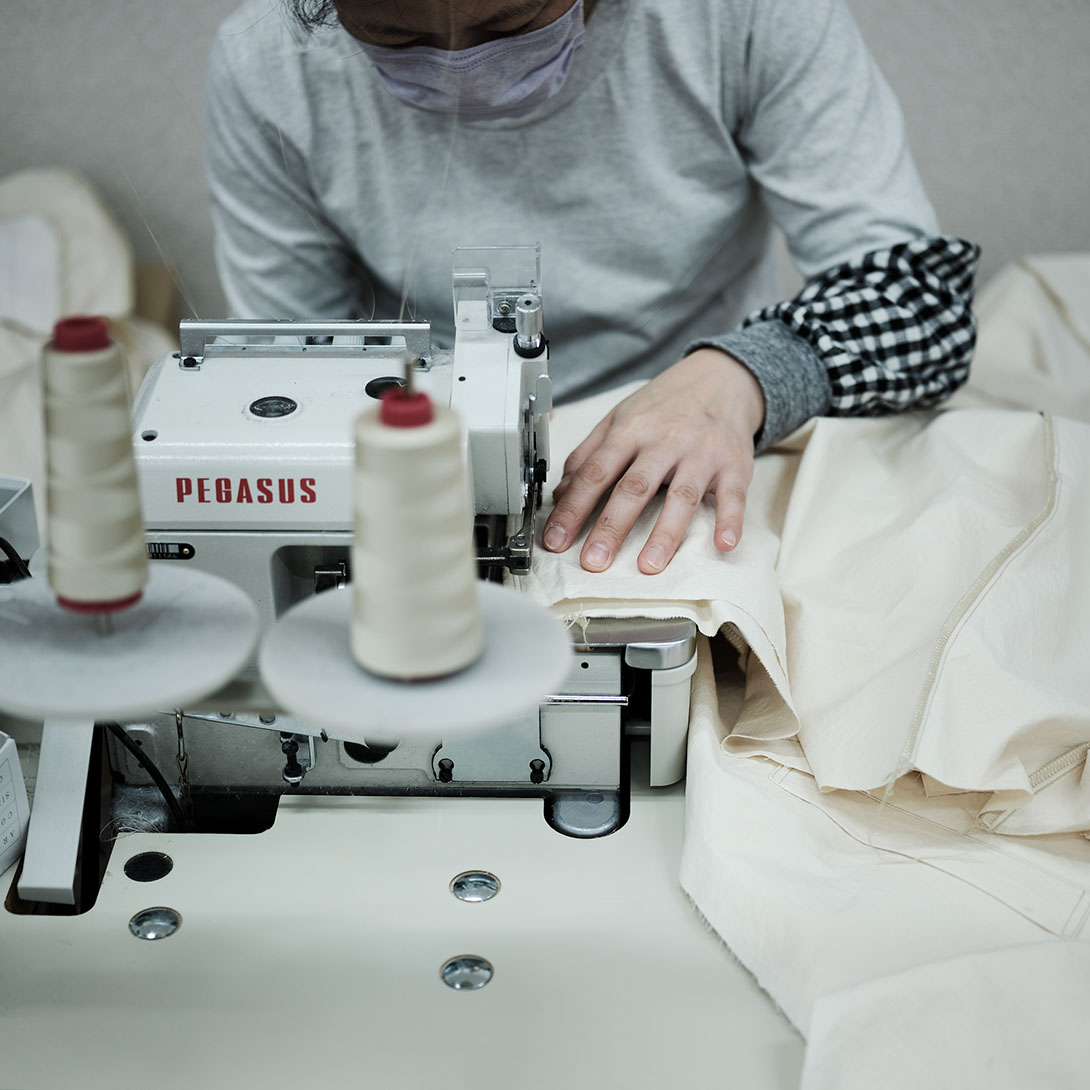
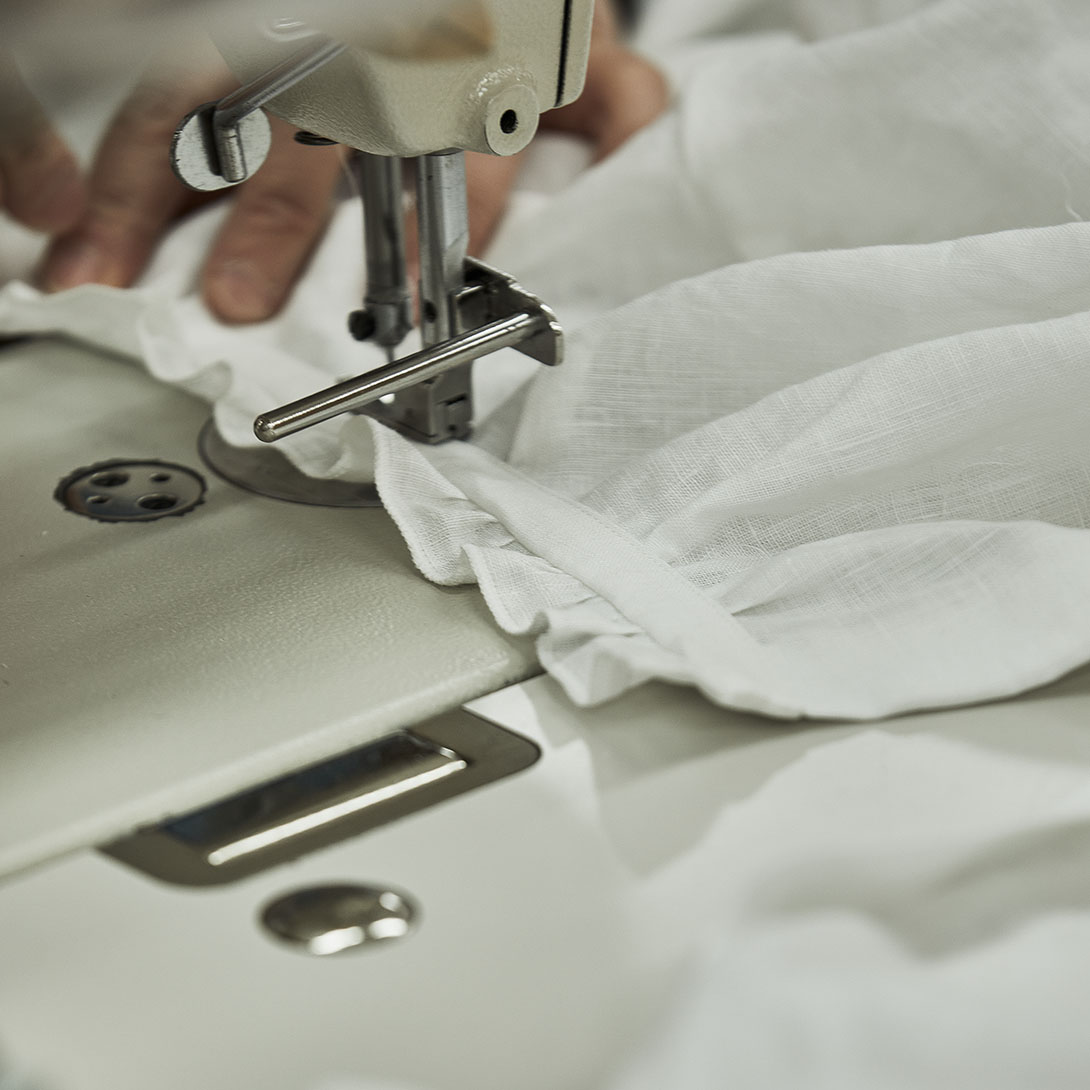
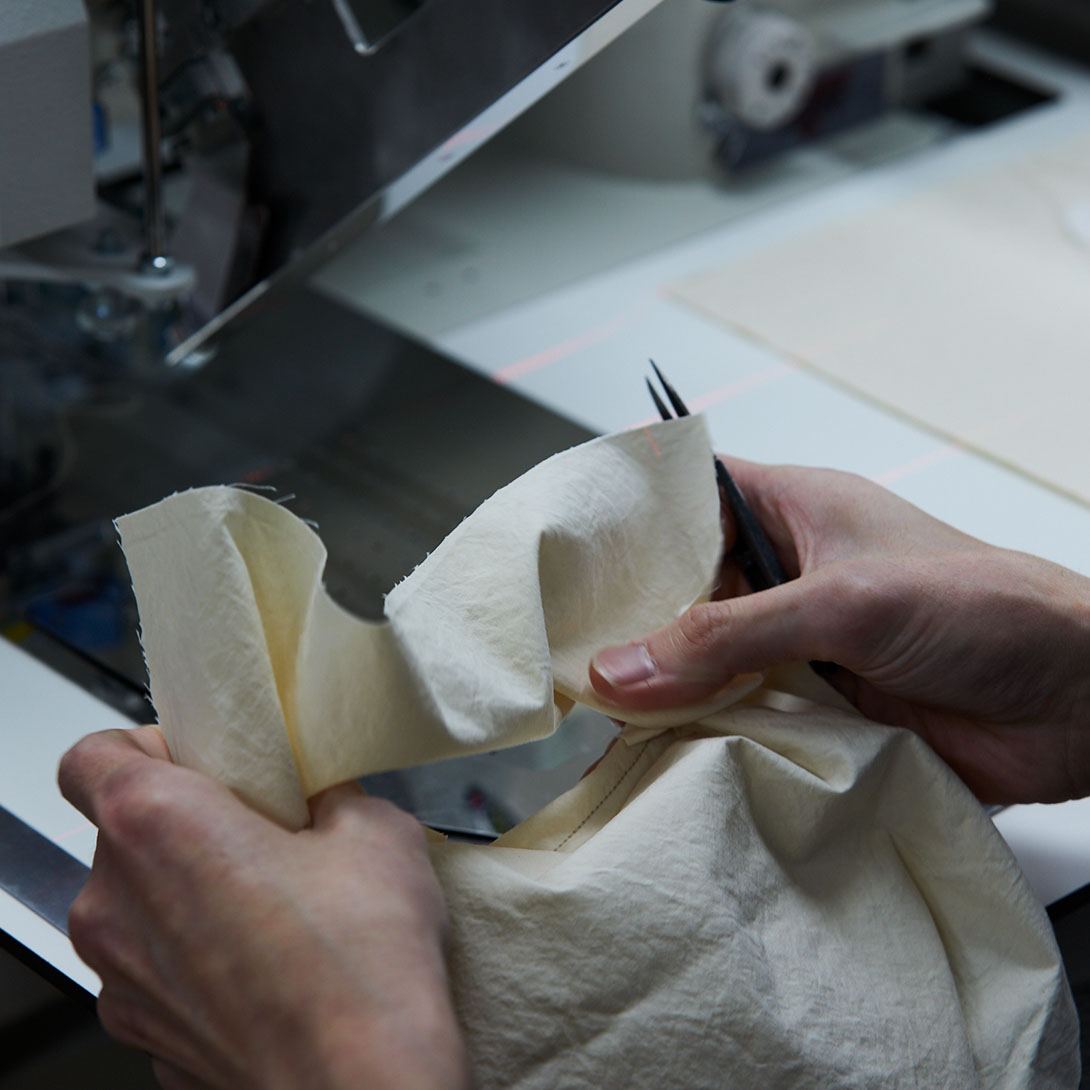
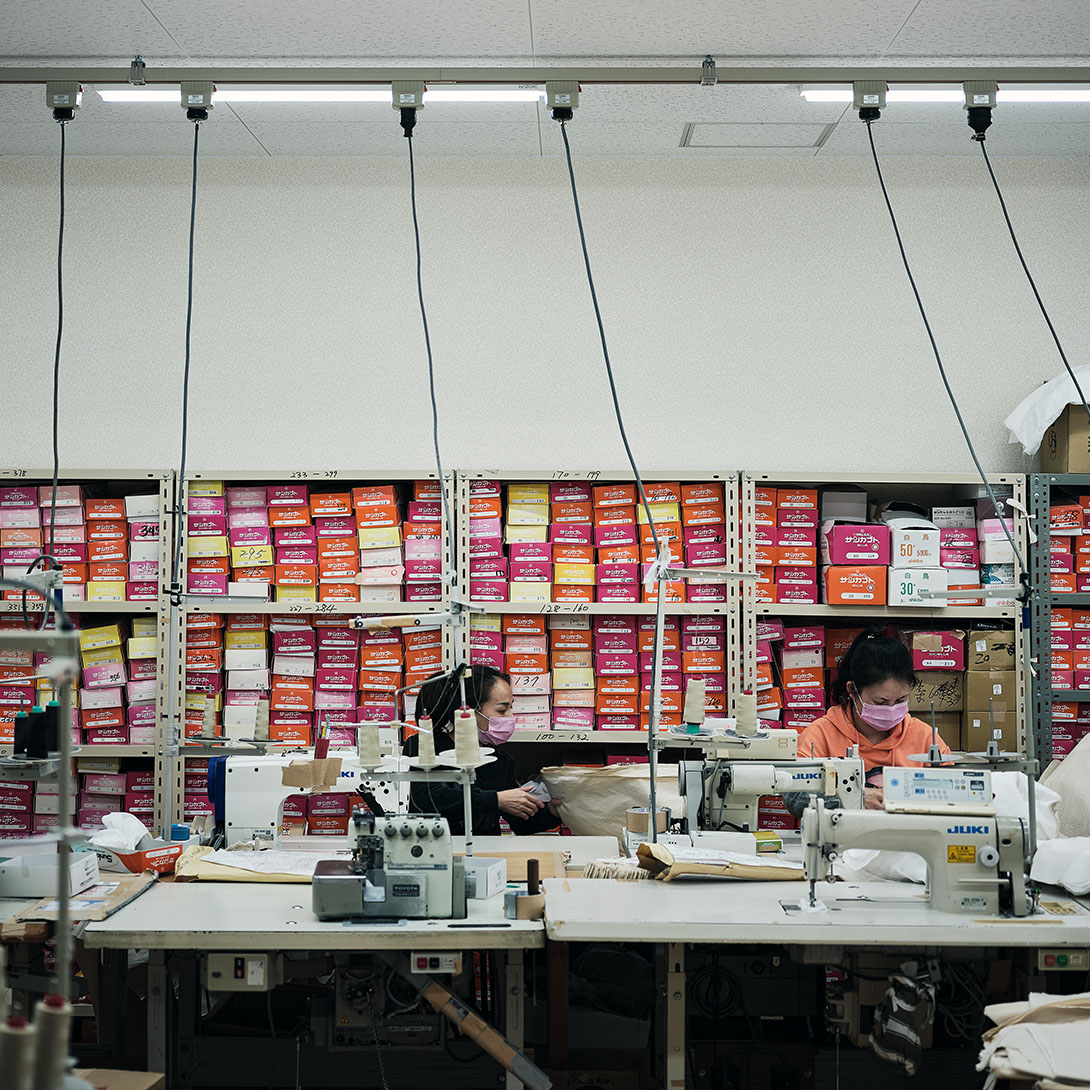
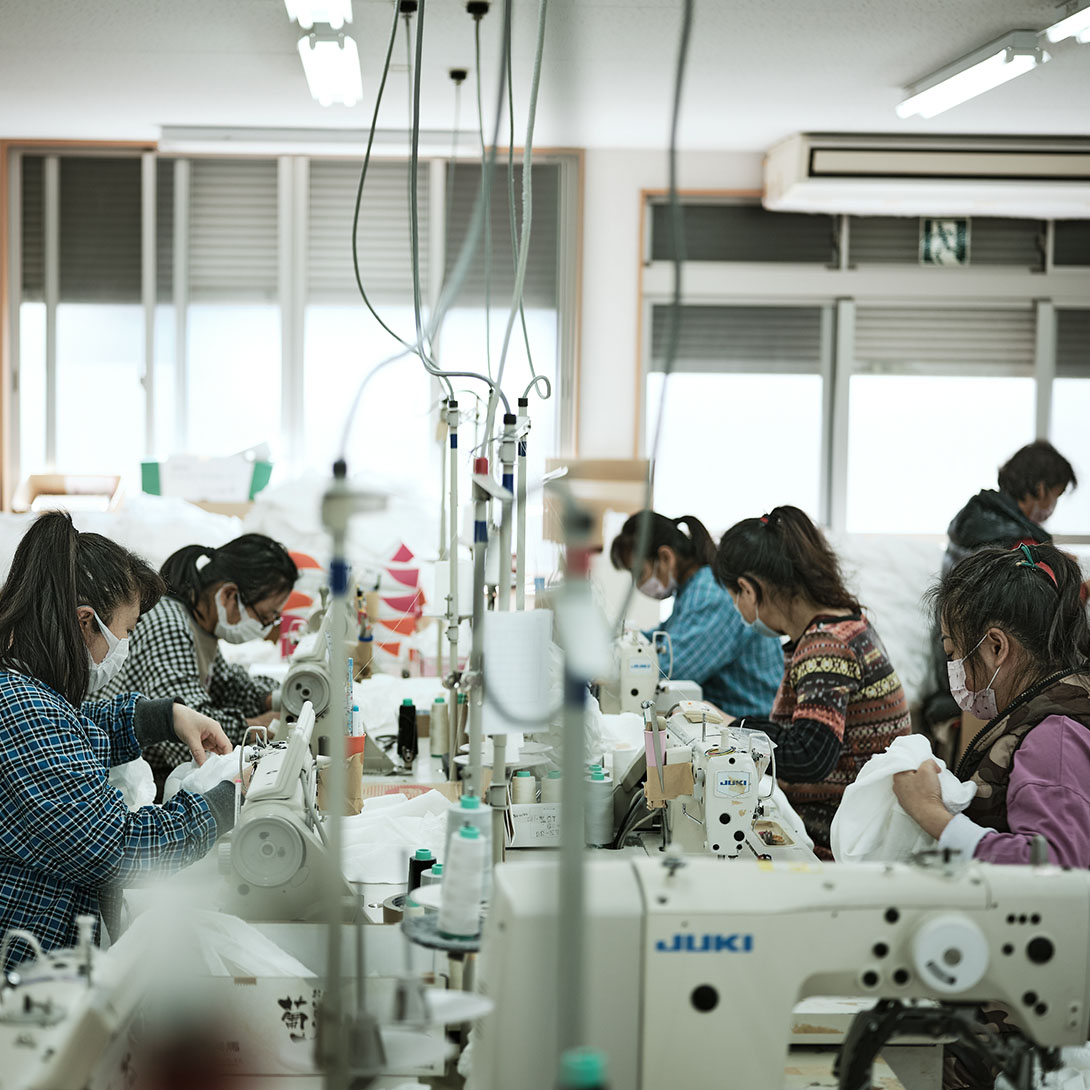
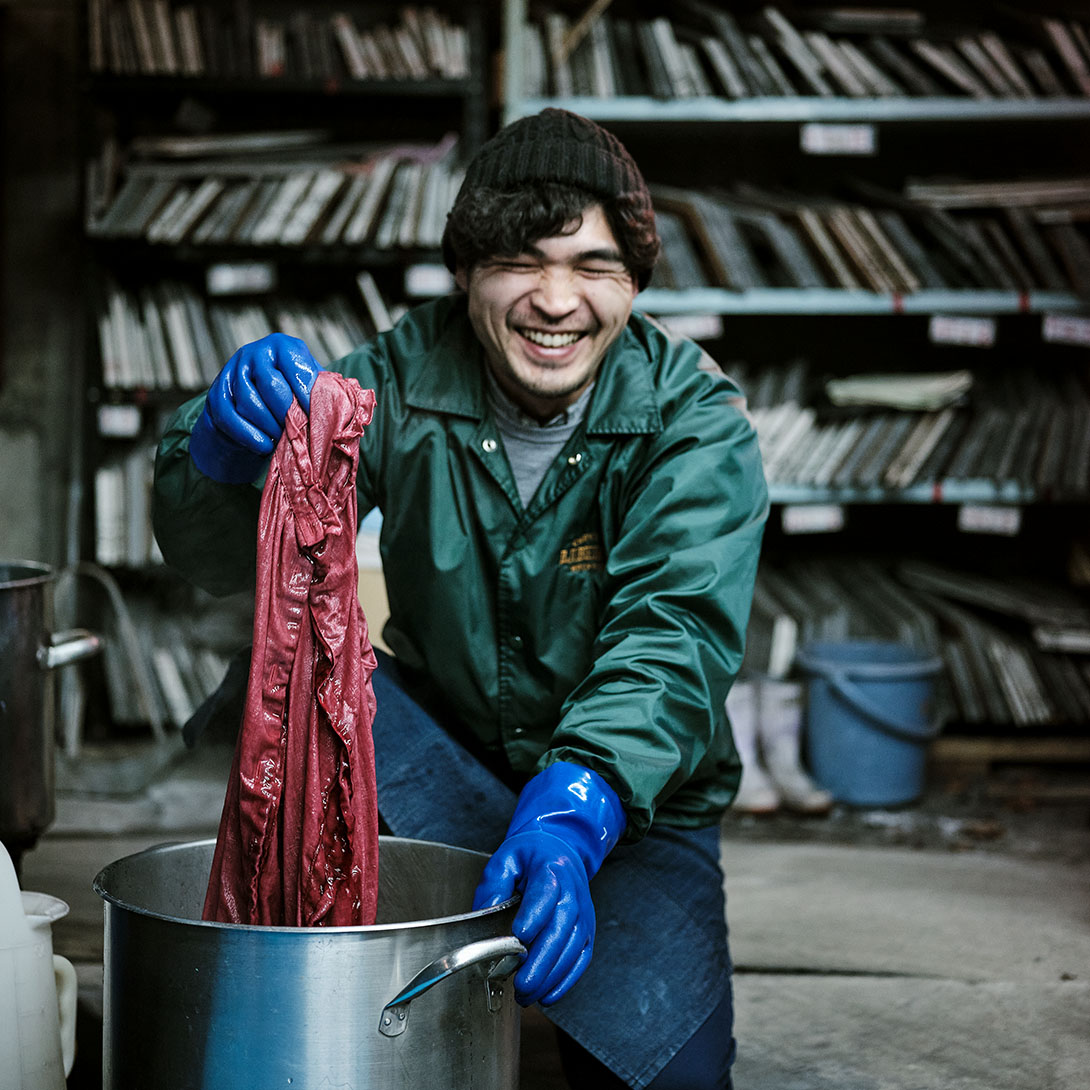
- 加工
-
製品に加工をする
More
一般的に洋服は、糸や生地を染めてから仕立てますが、〈ネストローブ/コンフェクト〉では、製品に仕立ててから染めに出す「製品染め」という手法をとることがほとんどです。その理由は、長年着込んだような立体感のある風合いが出せることと、1 着ごとに表情が微妙に異なることに価値を感じているから。だけどリネンは摩擦に弱いため従来の染色法だと破れやすく、フリルやレースなども多いので、リスクも大きいのが難点です。そこで精錬という下準備に時間と手間をかけたり、生地にダメージを与えないように温度を低めに設定したり、袖などの絡まりをほどきながら1着ずつ乾燥機にかけたりという手作業が必要となります。
またリネンデニムも人気アイテムですが、デニムの加工には「レーザー加工」や「オゾン加工」、「ミラクルバイオ」を取り入れています。一般的なサンドブラスト加工では、繊維の粉塵が舞い散るし、洗いをかければ染料の廃水が発生してしまいます。それは環境にも負荷が大きく、働く人の健康を害する不安も。新しく取り入れたオゾン脱色は、空気中にプラズマ放電を行ってオゾンを生成し、その強力な酸化作用によってデニムを脱色する仕組みで、水の使用量も少なく、使用したオゾンは自然分解して酸素に還るので安心です。ミラクルバイオも、特殊な酵素を使って微生物に食べさせて経年変化による表情を出す仕組みなので、エコロジーなのです。
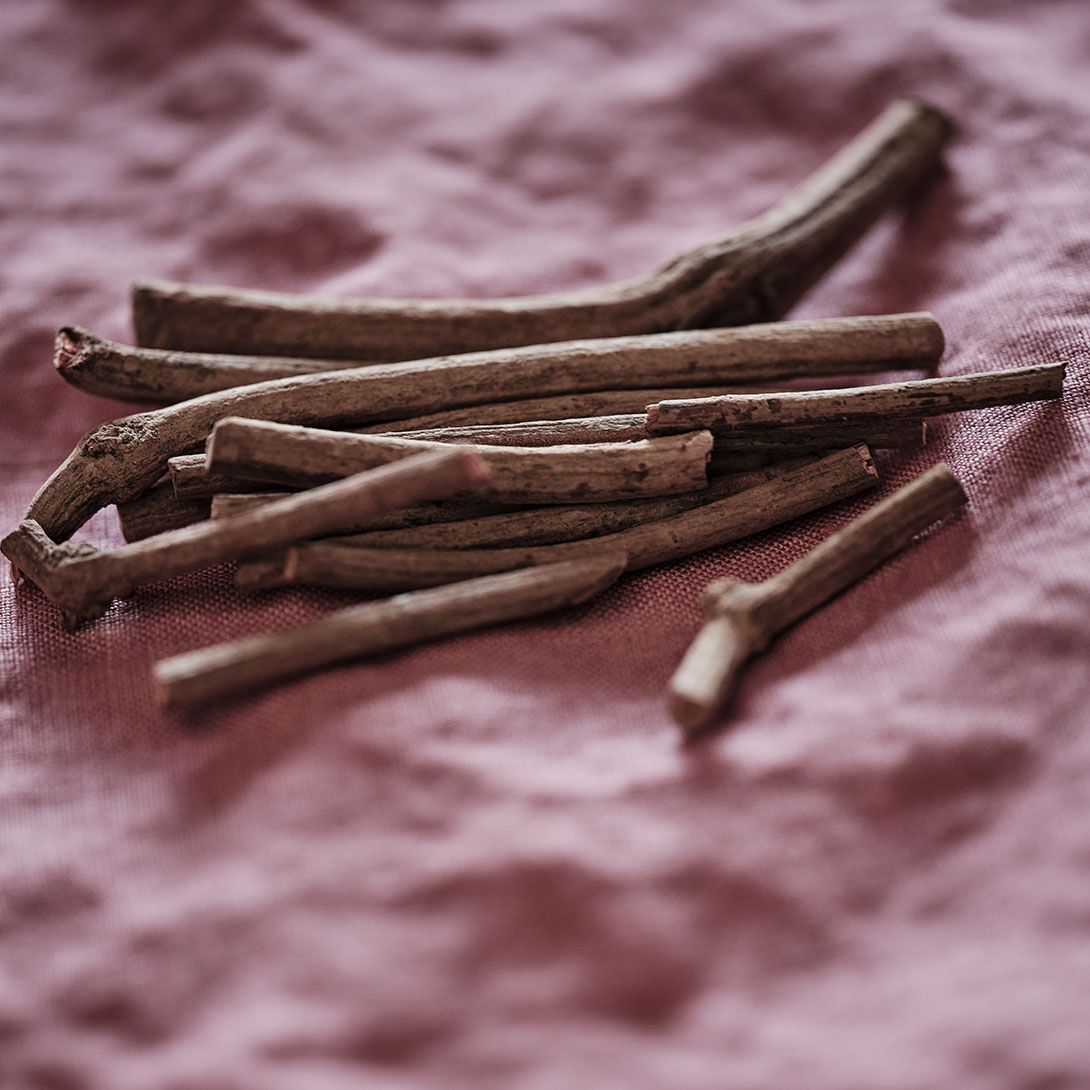
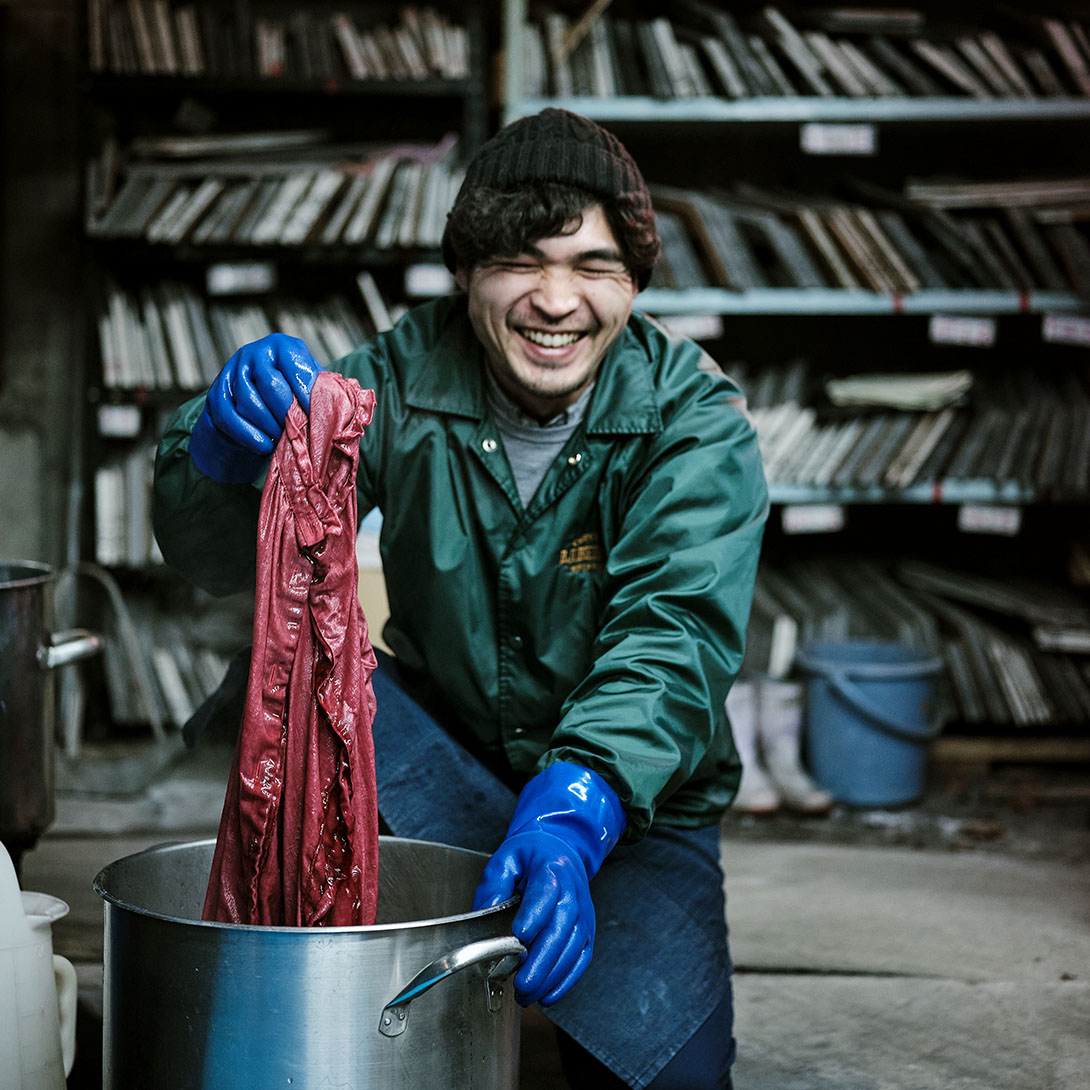
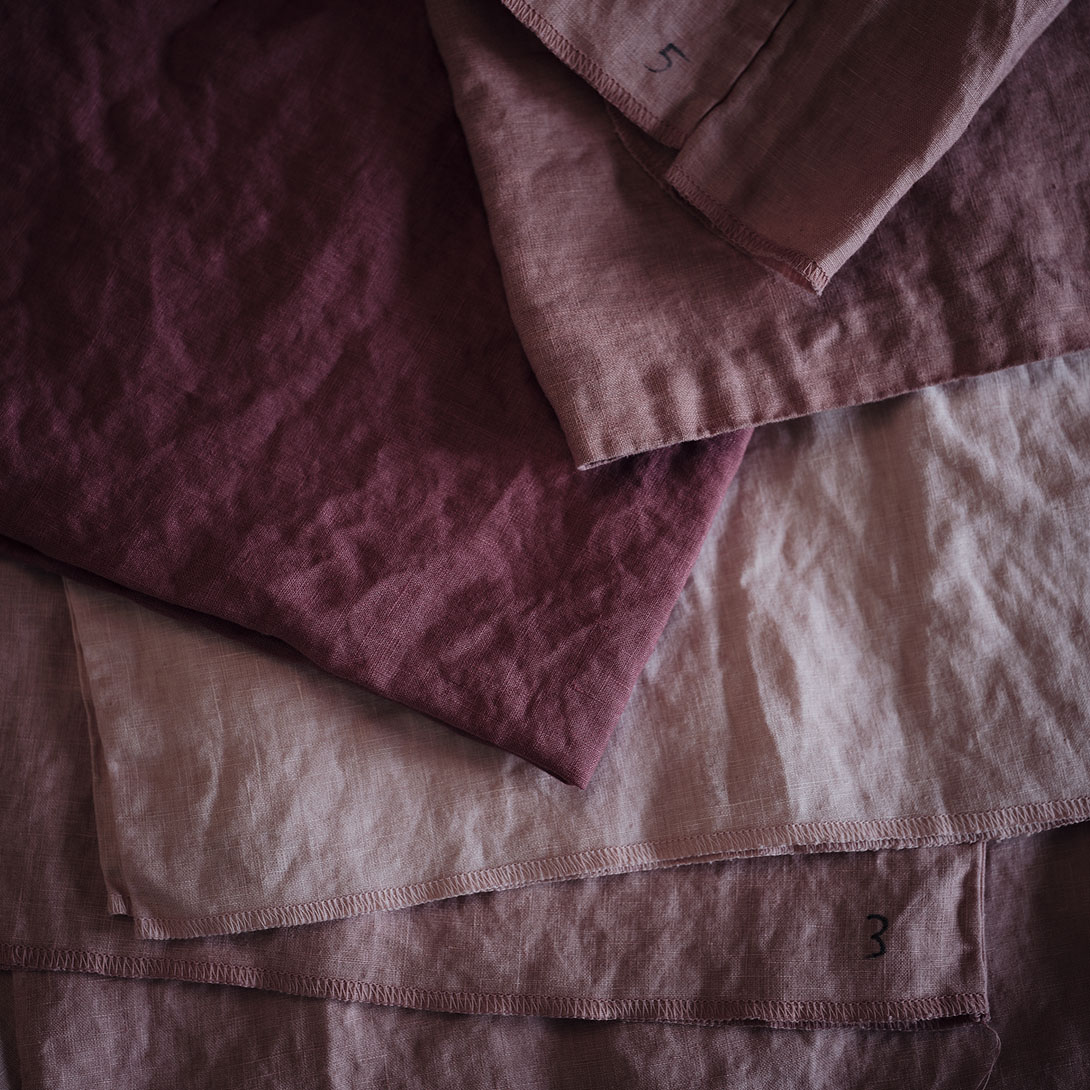
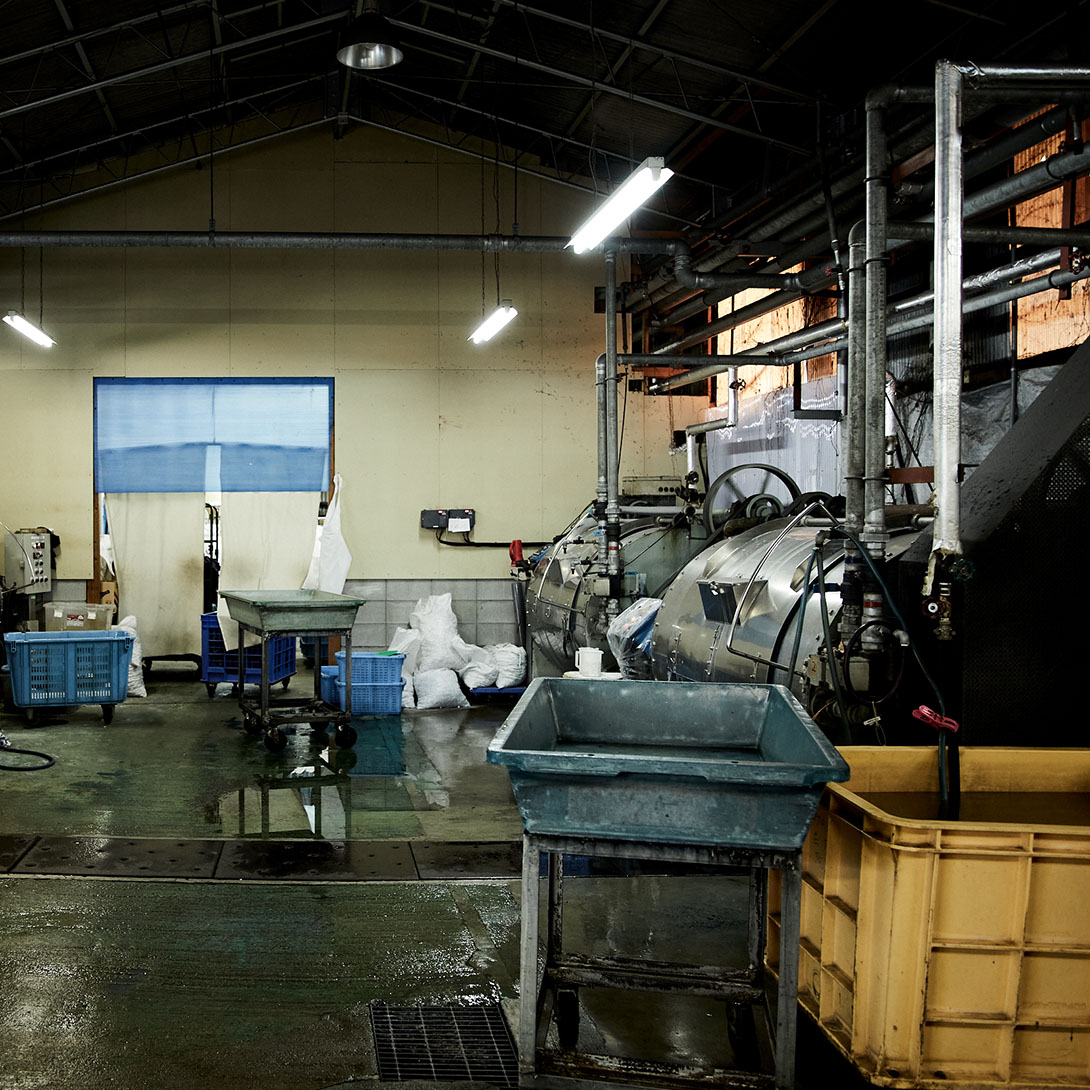
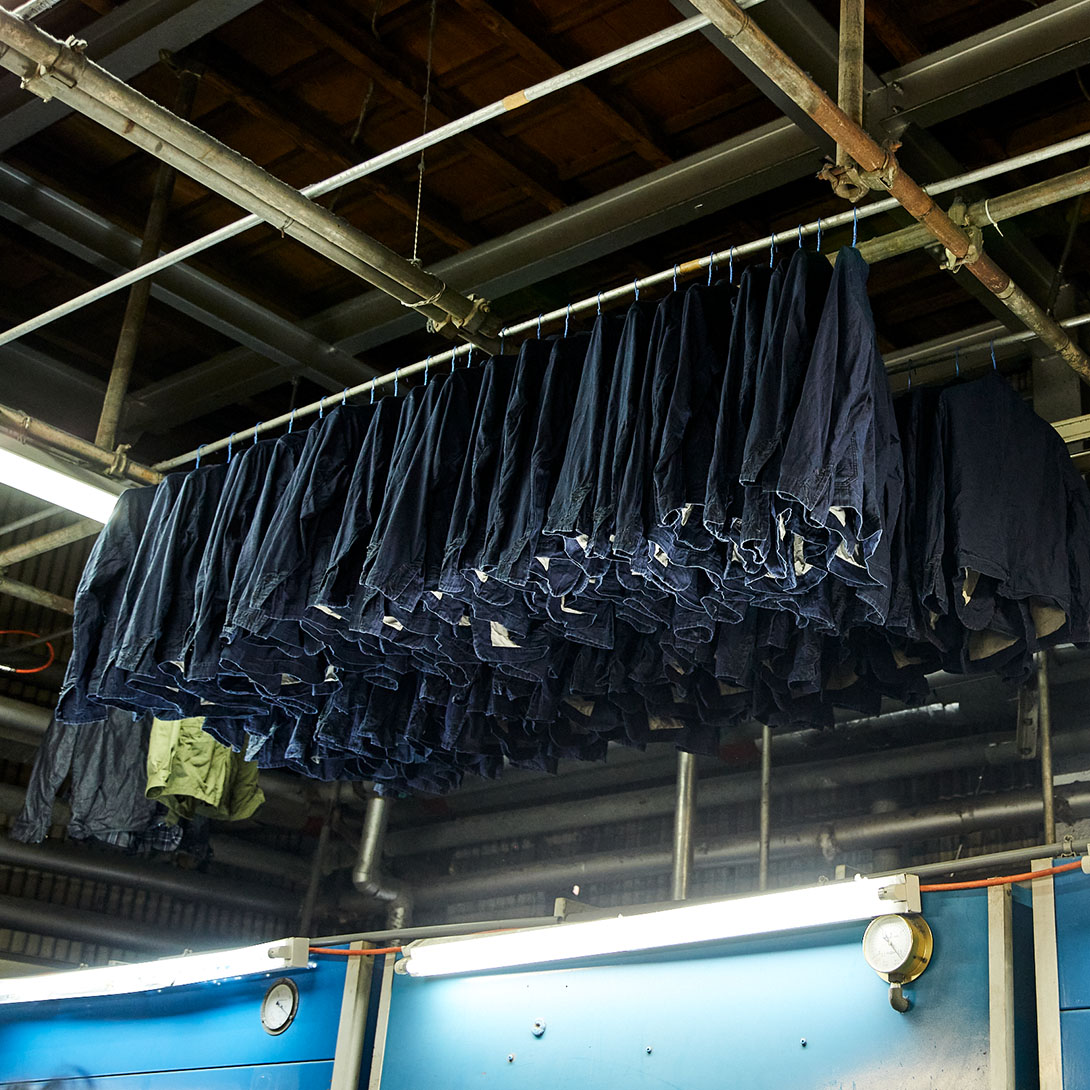
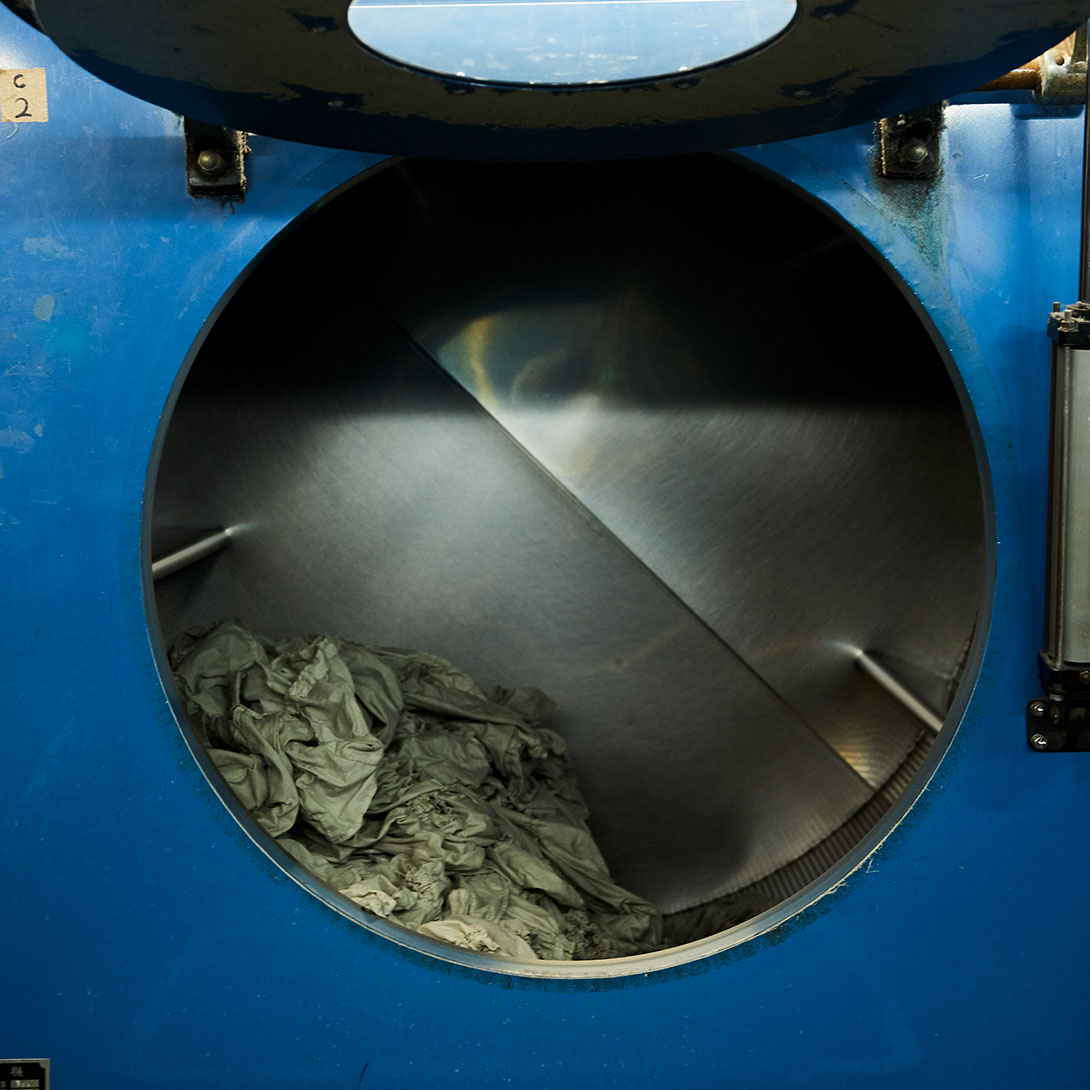
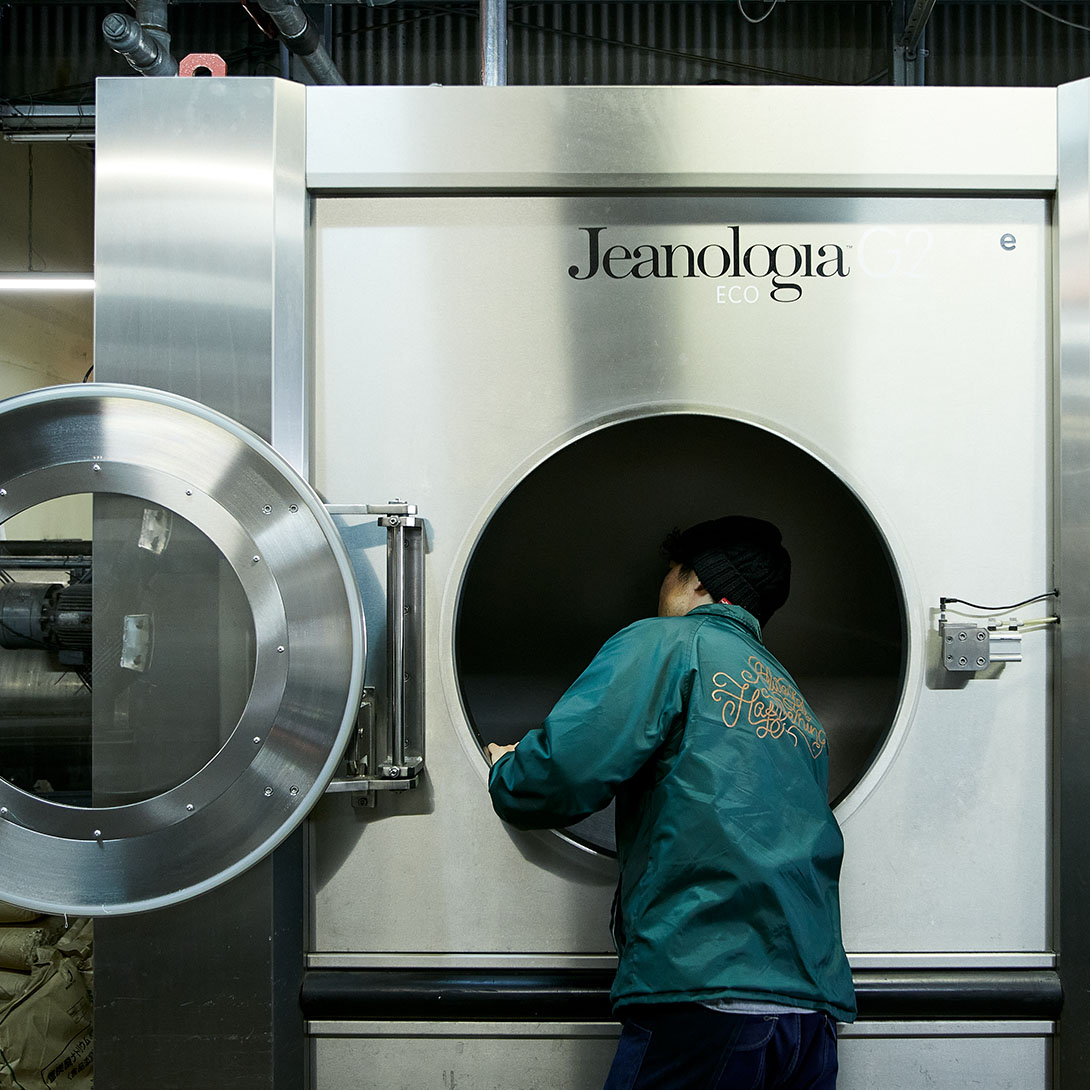
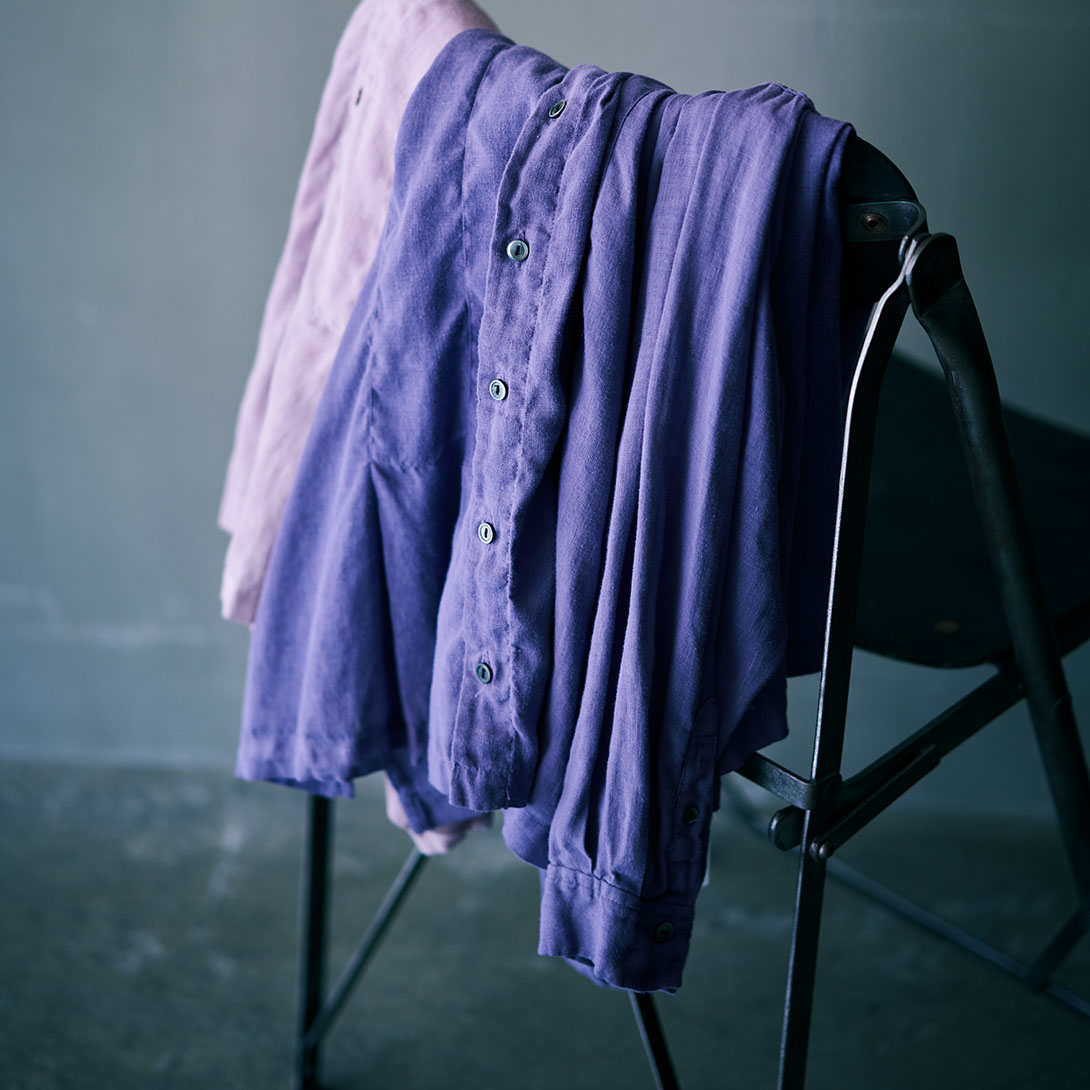
SPECIAL THANKS
- PHOTOGRAPHS : YUMIKO MIYAHAMA, KIYOKO ETO
- TEXT : SHIORI FUJII
- ART DIRECTION :
RYO SAITO, EMI NAKAMOTO(MIKATA & Co.)